PC吹塑泡壳之一步法工艺介绍
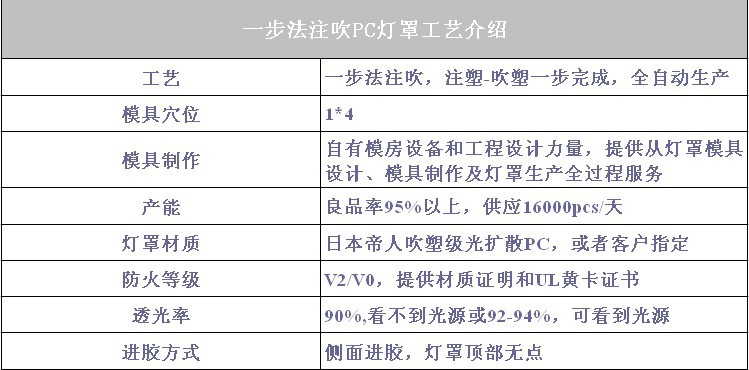
PC吹塑泡壳之一步法与二步法的工艺区别
1.成型方式:一步法注吹,模具由三件相同的循环工作的上模,注塑模和吹塑模二件下模,共五件模具组成,配一套热流道。生产时先注塑,后吹塑,灯罩成型过程一步完成;二步法吹塑为传统的吹塑工艺,模具由注塑模和吹塑模二套模具组成,生产时,先注塑灯罩的胚胎,等胚胎冷却后,人手放置加温炉重新加热,再人手放置吹塑模里吹气完成。
2.产能和损耗:一步法注吹,整个生产过程全自动,一台机器一出二,每天产能6-8K,一出四,每天产能12K以上,生产效率高,损耗低于5%;二步法吹塑,整个过程需要人手操作,效率低下,每天的产能3K左右,且因人手操作,工艺不稳定,损耗率高于30%。
3.后加工:一步法注吹基本不涉及后加工,如有涉及后加工,我们会建议客户修改图纸,以求量产时最快、最低成本;而二步法吹塑,灯罩口径为满足吹塑而加长的部份需要切割等等,基本都涉及后加工,从而增加了损耗、时间成本和人力成本。
4.品质:一步法注吹,注塑-吹塑一步完成,品质稳定,泡壳表面镜面光滑,泡壳口径位置的尺寸和泡壳壁厚都可以控制在公差范围内;二步法吹塑在生产过程中,注塑生产时,胚胎在外容易受潮和受空气尘埃污染,导致泡壳生产出来表面不够光亮,很多麻点;在加温炉重新加温时,温度很难把握,容易加温不均,导致灯罩壁厚不均。
5.装配设计:一步法注吹工艺,泡壳口径处是注塑而成,尺寸稳定,在设计上,可撇弃传统的粘胶方式,灯罩口径处设计卡扣,直接卡进灯杯,而这种省时省力的装配方式也为越来越多客户选择;而二步法吹塑工艺,由于受热不均及后加工切割易导致灯罩口径变形,装配时可能会无法与灯杯吻合,对尺寸要求精确的灯罩卡扣的设计就更无法实现了。
由此可见,对于新兴的LED球泡灯泡壳,从质量、产量、产品单价等各方面综合考虑,一步法注吹工艺是不二的选择。
LED球泡罩之玻璃灯罩与PC吹塑泡壳的优劣比较
- 外形:二者无太大区别,都可以做到超半圆或全周圆泡壳,实现大角度发光,而玻璃工艺更可以制作高难度的灯罩,如口径小或蜡烛拉尾等外形;
- 表面瑕疵:PC吹塑泡壳的表面镜面光滑,精湛的模具技术,令泡壳表面无进胶点,合模线也尽量做到完美,肉眼无法辨认,但整体外观无法达到玻璃灯罩晶莹剔透的效果;
- 透光率:新兴的光扩散PC,透光率90%以上,灯珠隐蔽性强,光照效果不逊于玻璃灯罩;
- 损耗:玻璃易碎,在生产、运输、工厂装配到客户使用过程中损耗率达到60-70%,采购、挑选、退货、换货的过程繁杂,并存在售后服务的困难和未知的赔偿等等,浪费大量的人力、物力和时间;而PC材料的泡壳正好弥补这一缺陷;
- 尺寸:玻璃灯罩尺寸不稳定,公差大,影响装配,必须打胶水;PC泡壳与灯杯的接口处为注塑而成,公差容易控制,尺寸稳定,容易装配,而且可以设计卡扣,直接卡在灯杯上,节省了装配的时间和打胶水的费用和人工;
- 产能和后加工:PC吹塑泡壳,不涉及后加工,模具穴位1*4,产能16000pcs天,玻璃吹制工艺,涉及喷砂、口径切割等后加工,所以要赶上这个产能,需要多台机器并配备多个人手;
- 产品单价:随着市场日趋成熟,LED也会进入量大微利时期,PC吹塑泡壳的产品单价也会向玻璃灯罩的价格靠拢;
- 模具费:玻璃灯罩的模具费几乎可以忽略不计;PC吹塑泡壳前期模具费投入大,但对于产量大的订单,分摊在单个产品上是可以接受的;
- UL认证:玻璃灯罩易碎,存在安全隐患,日本、欧盟等国家和地区都在逐步出台限制,出口认证难,PC泡壳取代玻璃灯罩已经是大势所趋。