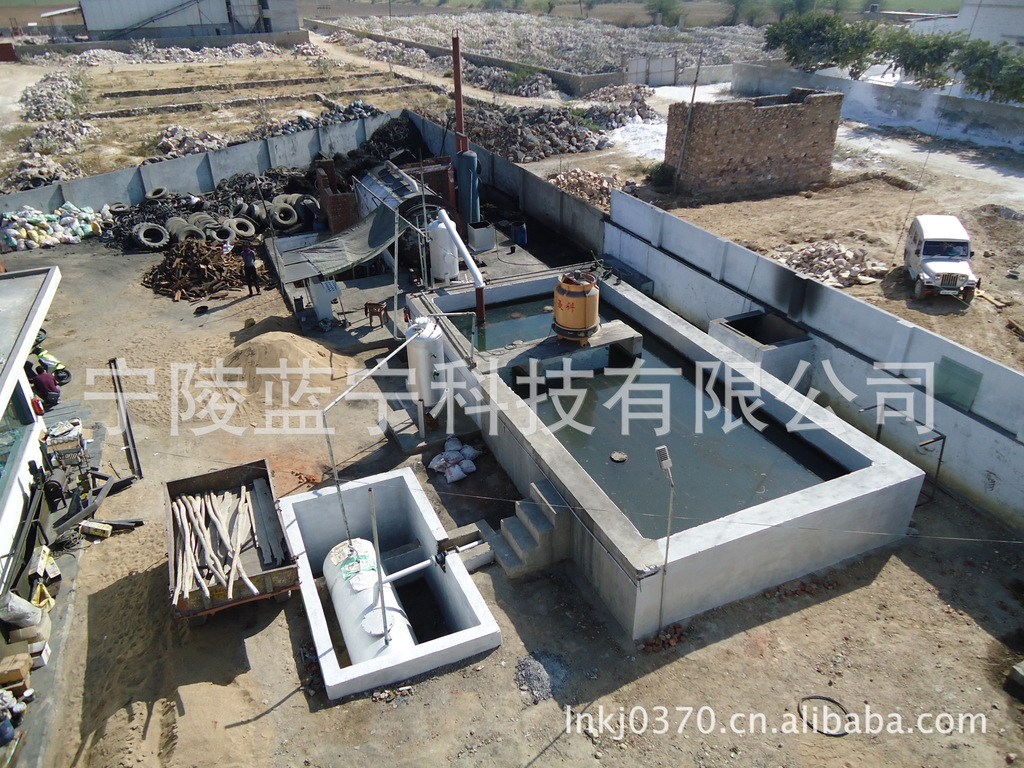
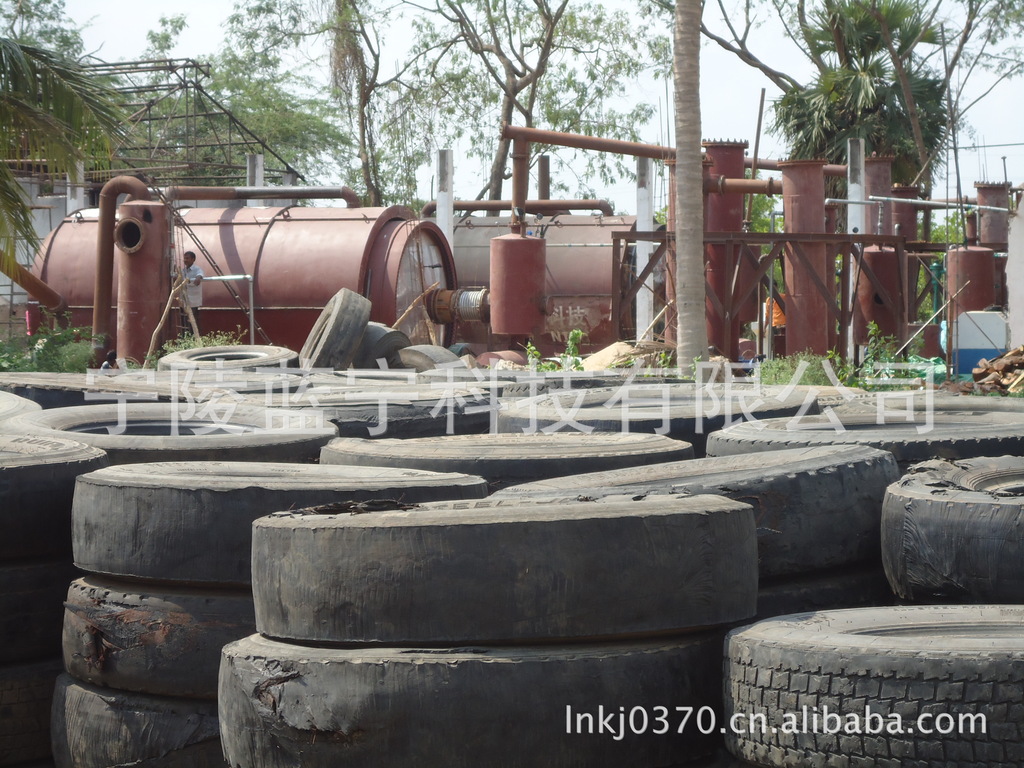
日本三菱重工开发的分解槽生产燃料油的工艺
首先将废塑料破碎成一定尺寸,干燥后由料斗送入熔融槽(300-350摄氏度)熔融,再送入400-500摄氏度的分解槽进行缓慢分解,各槽均靠热风加热。焦油状或腊状高燃点物质在冷凝器冷凝分离后需返回分解槽内再经加热分解成低分子物质。低点成分的蒸汽在冷凝器中分离成冷凝液和不凝性气体,冷凝液再经过油水分离器分离可回收油类。这种油粘度低,发热量高,凝固点在零摄氏度以下,但燃点广,着火点极低,是一种优质燃料油,使用时最好能去除低燃点成分。不凝性气态化合物经吸收塔出去氯化氢后可作燃料使用。所回收油和气的一部分可用作各槽热风加热的能源。
德国汉堡大学开发的废塑料流化床热分解为燃料油反应器。
废旧塑料从料斗中流出,由螺旋加料器输送进入电热反应器,其中流化层约20M深。每小时需要50L液化加热,热分解气体在电力除尘器中除尘,再在深度冷却器中部分液化,未经冷凝的气体可作为液化介质返回反应器再用。
美国肯塔基大学燃料化学家班迪塔格希艾等发明了用沸石分子筛作催剂将各种塑料放入沙浴器内混合,然后把这种浆液倒入反应器中,加氢加压,最后再加热导致高分子塑料分解成高质燃料油的方法。
以上三家国外具有代表性的废塑料油化设备,在生产过程中的三废处理都可以达到各自国家的环保要求,但投资都在2000万人民币以上,每天产量只有5吨左右的燃料油,无法推广,不具备商业价值。
中国大陆目前采用的废塑料油化设备主机主要采用立式固定处理器,工艺流程如下:废塑料首先从裂解处理器的顶部人工加入,接着封闭进料口,然后处理器底开始用煤或木柴做燃料缓慢加热,裂解处理器通常有5个立方米的容积,加料1吨,一般需要12个小时炼完一炉。结束后,停12个小时。等处理器温度充分下降后,打开处理器底下部的出渣口出渣,开始从处理器进料口进料,进入下一循环。
国内立式炼油处理器设备,在生产过程中的三废处理无法达到环保要求,而且产量低,不具备连续生产的能力,想有经济效益需要多个炼油处理器联合生产。
我们在各家研究的基础上,扬长避短,立足实际,从实际国情出发,经过多年的科技攻关,设计推出了“商丘市金源独具特色的系列炼油设备”。
二、最新系列炼油设备几大特色
1、每套设备由十部分组成:
1.1主机卧式旋转裂解处理器。
1.2进料系统。
1.3出渣系统。
1.4中央电控系统。
1.5冷凝系统。
1.6精致燃料油的各种系统。
1.7燃气加热系统(废气处理系统)。
1.8废液处理系统。
1.9烟道除尘系统。