【模具型腔】1出1,或1出左右件,1出2或多型腔
【模具结构】根据产品大小和结构特征、以及产品需求量确定最合理的模具结构
【产品材料】冷轧板,镀锌板,SPCC,SECC等
【模具材料】模座一般选用45#材料,冲头镶件可使用SKD11,这样可以保证产品的生产精度,而且模具寿命比较长。如果要模具质量更有保证可以选用SKH-9, DC53,ASP-23等 (更多其它钢材性能了解
请来电咨询)
【模具寿命】不低于100万次
【冲头配件】盘起,米思米等
【模具制造时间】45-60天
【模具首试成功率】80%以上
【最小起订量】1套
【加工能力】50套/月
【加工方式】定制加工,来图加工
【地理位置】海培德位于山东青岛市城阳区,距离青岛流亭机场仅有15分钟车程,交通方便
【厂房面积】20000平方米
【员工人数】包括一线生产人员和管理人员在内,海培德现有员工300多人,其中,工程师:20人,车间人数:210人,模具技师人数:80人
【质检人员】拥有专业的质检人员20人,负责从原料到模具出厂前的所有流程检测,严格控制模具加工过程中的质量状况,且从业人员都有正规认证上岗证书,对工作负责,对客户负责。


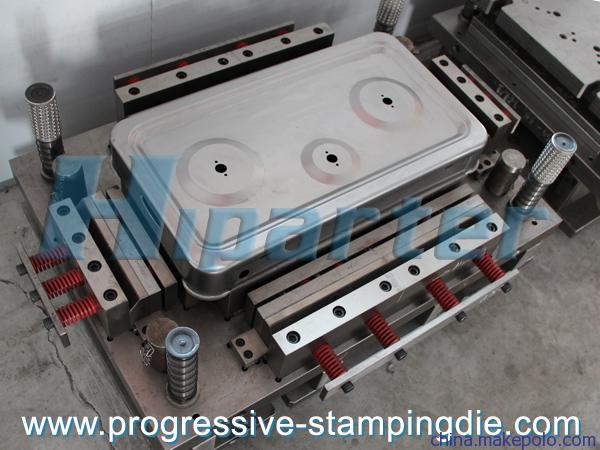
冲压模设计要求模具零件要有足够的强度,材料的选择不能有误。模具应避免有与机构无关的外部凸、凹部分,外部应有倒棱。原则上导柱安装在下模并远离操作者,模具中心力靠近模柄中心线,导向定位等重要部位要使操作者看得清楚。设计要考虑到操作、调整、安装、修理、搬运和储藏方便,对操作人员比较安全,除此之外,通常我们还需注意以下事项。
a. 要合理地确定工步数:冲压模的工步数等于分解的单工序之和,如冲孔——落料冲压模的工步数,通常是等于冲孔与落料两个单工序之和。但为了增加冲模的强度和便于凸模的安装,有时可根据内孔的数量分几步完成.其工步数的确定原则,主要是在不影响凹模强度的原则下,其工步数选用得越少越好,工步数越少,累积误差越小,则所冲出的工件尺寸精度越高。
b. 在冲孔与落料工序次序安排时,应把冲孔工序放在前面,这样不但可以确保带料的直接送进,而且又可借助冲好的孔来作为导正定位孔,以提高工件的精度。但在与某些弯曲后的尺寸或某突出部分位置成关联尺寸时,就要根据实际确定冲孔的位置。
c. 在没有圆形孔的工件中,为了提高送料步距的精度,可以在凹模的首次步序中设计有工艺孔,以使此工艺孔作为导正定位,提高冲件精度。比如在冲压模预冲Φ3.04mm,引导冲Φ3做在脱料板,以便折模尽量只折脱料板,下模单边+0.02mm,上脱两侧设Φ3顶销;上脱在最后出料处设顶销防粘模。冲压模若手工送料,定步距可以先冲工艺切舌,下一步设浮升挡块,用脱料板把切舌打平;自动送料要考虑设计安全销。但作为现在的模具设计中,我们对一些精密件的冲压已经逐步或全部采用了外框式的导料带。这样有利于保证复杂工件的加工精度。
d. 同一尺寸基准的精度要求较高的不同孔,在不影响凹模强度的情况下,应安排同一工步成形。
e. 尺寸精度要求较高的工步,应尽量安排在最后一工序,而精度要求不太高的工步,则最好安排在较前一工序,这是因为工步越靠前,其积累误差越大。
f. 在多工步的冲压模具中通常依次优先安排冲孔、切口、切槽、弯曲、成形、切断等工序。
g. 冲不同形状及尺寸的多孔工序时,尽量不要把大孔与小孔同时放在同一工步上,以便修模时能确保孔距精度。
h. 在设计时,若成形及冲裁在同一冲模上完成,则成形凸模与冲裁凸模应分别固定,不要固定在同一固定板上,尽量把成形凸模固定在脱料板上面,后面加装背板。
i. 在设计时,一定要使各工步已成形部分不受破坏,使带料保持在同一送料线上。
j. 对于工序步数很多且带有较多弯曲工步的模具,其凹模刃口应尽量采用镶件结构,可实现快速更换和修磨。


