冷拉方钢: 138 2186 1958 ,
扁钢扣QQ扣:27 988 1858 ,
NH热处理淬火油催冷剂以无灰分中、低分子油溶性高聚物组成,能最大限度提高淬火油的淬火冷却能力,具有较高的热稳定性和热氧化安定性,是调配超速、快速光亮淬火油的基本原料。
特点:
NH淬火油催冷剂能实现无灰分分解,可使经保护加热的工件淬火后表面光亮;其分子量控制在一定范围内,可有效地提高催冷剂的热稳定性和热氧化安定性,维护淬火油冷却性能的稳定性。
NH淬火油催冷剂,可有效地提高淬火油的高温冷却能力,减小淬火工件不均匀畸变,提高工件淬火表面硬度及淬硬层深度。
[size=10.5pt]NH[size=10.5pt]淬火油催冷剂,已经油溶性处理,在常规淬火温度,可均匀溶解在机械油中,使淬火工件均匀冷却,表面硬度均匀。
使用:用于提高淬火油的冷却能力,提高淬火工件淬火后表面硬度和淬硬层深度,改善淬火工件心部组织。
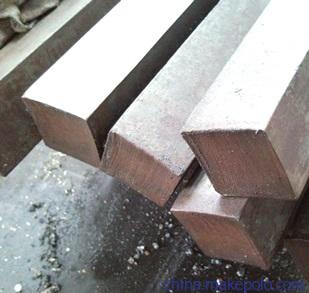
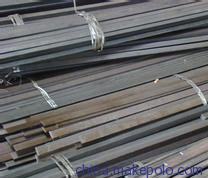
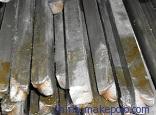
感应加热工艺是感应加热技术水平的主要体现,是技术发展的基础,先进的感应加热工艺技术可以有效地发挥感应加热的特点,实现高效、节能的局部热处理。
(1)纵向感应加热淬火 半轴纵向感应加热淬火已用于汽车、拖拉机工业。半轴纵向加热是一次淬火。在德国、美国有半轴一次淬火专用机床,将加热、校正和淬火在一台机床上完成,提高了生产率,一次淬火与连续淬火相同产量的设备占地面积各为40m2与115m2。
(2)曲轴颈圆角淬火 曲轴颈圆角淬火后,疲劳强度比正火的提高一倍,我国生产的康明斯与 NH发动机曲轴均已采用此种工艺。
(3)低淬透性钢齿轮淬火 早在20世纪70年代我国曾进行55DT、60DT、70DT钢研究并取得初步成果,以后因钢的淬透性不稳定等原因,低淬钢未继续用于生产。1992年俄罗斯低淬钢创始人,K.3ЩЕПЕ ЛЯКОВСКЦЦ博士来中国讲学,并到某一钢厂调查冶炼低淬钢的条件,认为该厂完全具备生产低淬钢条件。
YB 2009—1981《低淬透性含钛优质碳素结构钢》中对合金元素的控制与俄罗斯不同,(俄)1054—74、58(55П П)钢的元素含量对 Mn、Cr、Ni、Cu四元素之和规定要求<0.5%(质量分数),而YB2009—8155Ti钢对Cr、Ni、Cu三元素之和规定<0.5%(质量分数),这可能是关键所在。
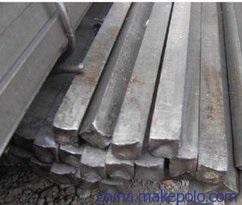
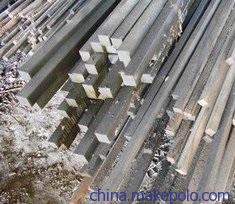
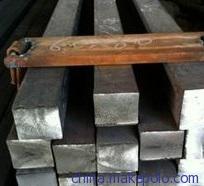
NH淬火油催冷剂添加前应对长期使用的淬火油进行沉降、过滤,去除油品中杂质,采用普通机械油调制快速、超速淬火油不需此工序。
NH淬火油催冷剂添加前应对长期使用的淬火油进行加热脱水,加热时油品处于流动状态,使油槽底部的水份充分蒸发。
[size=10.5pt][size=10.5pt]NH[size=10.5pt]淬火油催冷剂添加时,应对油槽中油品加热搅拌,缓慢倒入添加剂,使添加剂均匀溶解;添加比例根据油品的冷却特性要求控制在[size=10.5pt]2[size=10.5pt]~[size=10.5pt]5%[size=10.5pt]。
1、裂纹类型:纵向裂纹
特征:由表及里、深而长。
形成条件:淬透工件易发生,原材料有碳化物带状偏析或非金属夹杂物延伸。
防止措施:控制原材料质量,公道选择预热处理以改善原始组织。
2、裂纹类型:网状裂纹
特征:位于工件表面、深度0.01~2mm。
形成条件:表层脱碳件、化学热处理和表面淬火件易出现。
防止措施:采取加热保护,避免脱碳、延缓淬火冷却,降低淬火温度。
3、裂纹类型:弧形裂纹
特征:常位于工件角落处,隐于表面层下。
形成条件:易发生于未淬透工件或渗碳淬火件。
防止措施:改变工件设计、截面过渡圆角公道化。
4、裂纹类型:剥离开裂
特征:表现为淬硬层剥离。
形成条件:表面淬火件或化学热处理件。
防止措施:公道选择介质,延缓冷却。
5、裂纹类型:显微裂纹
特征:在显微组织缺陷处。
形成条件:淬火件高碳马氏体针四周。
防止措施:避免加热过热和晶粒粗大。

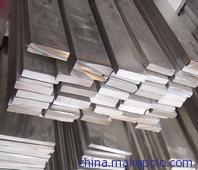
减少大型行星齿轮渗碳淬火变形的工艺措施大行星齿轮材料为20Cr2Ni4A钢,要求齿面渗碳淬火。层深1.9-2.3mm,齿面硬度58-63HRC,心部及其它表面硬度35-45HRC,端面平面度≤0.6mm。
因为要求齿面渗碳淬火,所以工艺过程为锻件正火粗车后整体镀0.08~0.10mm的防渗铜层,然后插齿,渗碳淬火。考虑到防渗铜层会吸氢产生氢脆,为避免渗碳淬火后发生氢致延迟裂纹报废,渗碳淬火采用渗碳后空冷排氢到室温,重新加热淬火、冷冻及回火处湿。大行星齿轮直径Φ601.32mm,幅板厚只有17.5mm,两面不对称,属于热处理易变形的盘状零件,加之材料为20Cr2Ni4A钢,淬火组织转变应力大。
淬火后变形大,变形大的主要原因是渗碳后空冷,重新加热淬火引起畸变叠加。为此改进装挂方法,使齿轮两面冷却速度接近一致,渗碳后直接淬火比重新淬火变形小。将重新加热淬火改为渗碳后充氦排氢、直接淬火工艺取得了很好的效果。端面平面度≤0.4mm。最小达到0.1mm,留磨量减少到0.5mm,齿面硬度提高到60-62HRC,磨齿后硬度≥58HRC,齿轮使用寿命达到10000h以上。解决了生产难题,如果淬火时打开油循环泵冷却,效果会更好。