大口径直埋保温管生产线
一、设备构成(工艺流程)
自动上料机--料斗式干燥机---高效单螺杆挤出机--螺旋分流式机头模具--真空定径冷却箱--多履带牵引机---行星切割机--收料台
1、高效单螺杆挤出机的优点
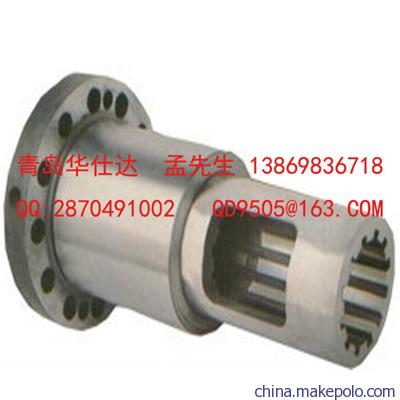
A:采用德国最新的固液相分离式螺杆,缩短PE颗粒料从固态到熔融状态过程中在机筒中的行程距离,降低耗能,增加产量;加长菱形混料段,增加物料挤出品质。
B:机筒螺杆进料段①采用强制进料,运用沟槽式机筒内胆,加快PE颗粒的进料能力,且方便更换;②采用加长式冷却段,确保PE颗粒在进料时温度较低有足够的进料摩擦力,避免机筒螺杆温度从前端往进料口段过多的导热。
C:采用江阴国茂优质减速箱,保证减速箱的使用寿命;在减速箱增加温度控制系统,实时监控减速箱内润滑油的温度,保证油温在任何时候都在合适的温度。
D:加热圈,采用陶瓷加热圈,加热均匀使用寿命长,避免了以往使用铸铝加热圈式容易烧断加热丝的弊端。
E:电机采用杭州恒力直流电机,变速器采用进口美国易泰帝品牌,电控系统电气元件采用国内外知名品牌产品。
2、机头、模具

A:采用螺旋式机头模具,使挤出的管材合模线互相叠压,增加制品的内压强度。机头主体采用铸钢镀铬材质,数控机床一体式加工,进行了严格的抛光处理,保证了机头体的整体强度和精密度,保证了高压挤出物料时的稳定性。
B:真空定径套,采用不锈钢材质,优点耐磨、硬度大,在拆卸模具时不容易磕碰上沟槽。与锡青铜制定径套相比,在导热冷却性上略现不足,但是我们在不锈钢套上增加了冷却水环结构和加长了定径套长度。另外,采用锡青铜制定径套,由于铜是软质金属,才更换定径套时不可避免会有磕碰,容易在内表面形成沟槽或者使定径套变形,并且不容易修复,所以我们采用不锈钢制定径套。
C:便携式口模芯棒转向结构,特别是针对于大机型。口模芯棒的重量实在太大,如果在竖直平面上更换,首先不方便模具的定位,其次不方便安装,最主要的问题是不安全,能威胁到安装人员的人身安全,因此我们增加了机头的转向机构,只要拆卸下挤出机和机头的法兰螺丝就可以运用此机构使机头进行90度向上旋转,将口模芯棒调整在一个水平面上,方便更换口模芯棒,更加安全可靠。
3、真空定径冷却水箱
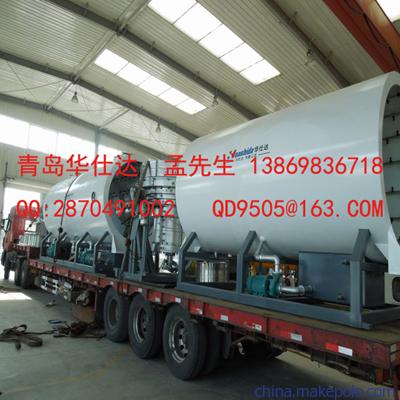
A:箱体材质:采用优质碳钢。也许有的客户认为碳钢的耐腐蚀性不如不锈钢好,但是我们将内表面做完防锈处理后进行了优质防锈漆的喷涂,并且加大了箱体板材的厚度,保证了在没有内表面破损的情况下二到三年内不出现破损现象。
B:冷却水箱的前后左右的移动。前后移动电机采用铸钢材质,避免了以前采用铸铁材质电机时出现的由于电机吃力太大将电机壳拉断扭裂等现象;左右移动采用直线滑轨手动微调,避免了以前的丝杠调节笨重费力的劣势,使左右微调轻松省力。
C:水箱内管材托架方便、耐用。小口径管材使用尼龙腰棍托架,采用角度调节以便适用于不同的管径生产;大口径管材使用尼龙托板支撑,既加大了支撑力度不至于管材变形,又不缺乏润滑性使管材前进时增加摩擦力加大后续设备的工作负荷。
D:喷水嘴使用尼龙注塑工艺。尼龙首先自润滑性好,不像普通材质的喷嘴容易容易堵塞;另外,尼龙材质机械性能好,不普通喷嘴更耐用结实。
E:排水喷水系统管路均采用不锈钢材质,且在水泵进出水区增加了过滤系统过滤杂质使之不进入水循环系统。
4、多履带牵引机
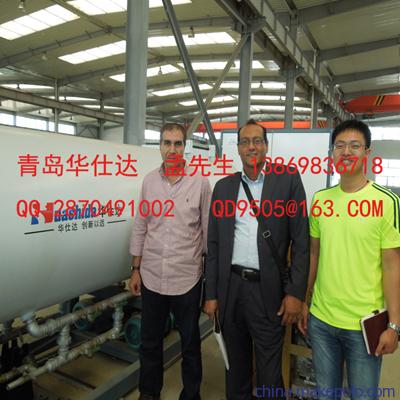
A:牵引爪:主体支撑架使用济钢优质冷轧钢板,在焊接过程中降低热胀冷缩变形,另所有的切割均采用激光切割精确、美观、整洁。牵引硅胶快:均采用纯原料胶块,摩擦系数大、强度高。牵引爪加紧系统:采用铸钢件发黑处理,机械强度高、耐磨。牵引爪转动变速系统:采用高精密度变向变速箱,齿轮机构耐用程度高,外壳采用铝合金材质美观、整洁,一改传统的普通铸铁变速箱选择。
B:端面安装板材均采用16mm厚济钢冷轧优质钢板,保证钢板的平整度,使前后端面始终保持在绝对的平行面上。
C:牵引机左右观察窗均采用机车用有机玻璃,美观、大方。
5、行星切割机

A:行星导轨采用铸钢材质,数控机床一体式加工,精密度高,在进行自转是不会因为自身的重心不稳定而出现滑轨。
B:进刀方式:机械或油压进刀两种方式客户自选。刀具采用塑料管材切割专用刀具。切割机道轨采用专用铸钢道轨,耐磨、实用,使用寿命延长。
C:机械定尺切割。采用触点式计长方式,一改原来从用光电计长时受环境影响大的劣势。
D:切割机带有自动正圆装置,在切割时保证了管材的圆整度使切割面光滑,平整,误差小。
6、生产控制系统
采用世界先进的PLC塑料设备专用控制系统,一体式操作,即可全线整条联机操作又可在主机电控位置低整条生产线的单机进行独立操作。可加装远程操控系统,对整条生产线进行全程监督生产。对操作人员的素质要求一般,只要敢操作,培训两三天就可独立上机操作,操作简单,使用人力少。
二、与内压法生产线对比
1、人力方面:内压法生产线需要三到五人同时操作一条生产线,并且管材切割需要人力切割,劳动强度加大。由于管材切割采用人力,造成切割面不平整,在灌注聚氨酯时端面的闭气性不好要进行端面的二次加工,造成人力和时间的浪费。
2、效率方面:以120生产线作为比较,生产标准外径500mm长度11600mm管皮子,内压法生产效率为每天生产30-40根,而采用高效真空定径法生产线每天的产量为90-110根,是内压法的2.5-3倍的效率,且耗电低,普通主机主电机为180KW生产率为300KG/H,高效主机主电机为132KW生产率为400-450KG/H,耗电和经济性能显而易见。
3、废料率方面:内压法由生产工艺决定每生产30-40M管材就要做一次闭气操作,也就是每生产30-40M管材就要有0.5-1M的管材废料,而真空定径法生产线只有在开机生产时由于刚开机生产有一段0.5-1M的废管,在其他时候在不是误操作的情况下不会出现废品。