
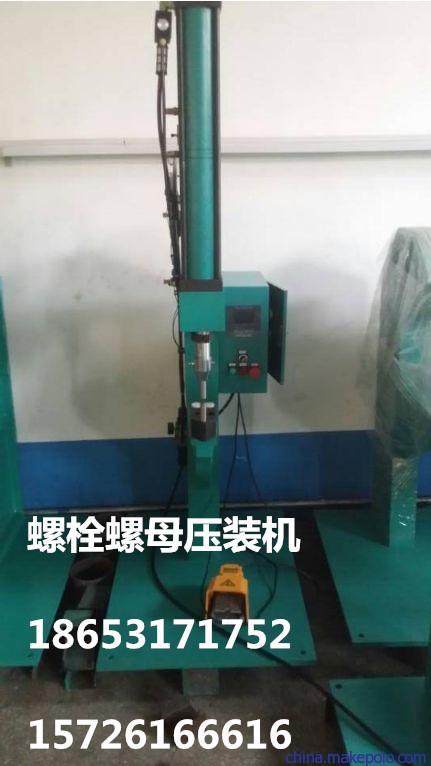

1. 原理
气液增压冲压技术及其设备的核心是-气液增力缸。它是一个内置液压油系统的气增油压的冲压动力装置,只需4bar~7bar压缩空气驱动,即可产生2kN~2000kN的冲压力。在冲压设备中,就是以此高可靠性的集成组合,取代了传统冲压设备的繁杂动力驱动系统和庞大的装机功率。而在运动特性方面,气液增力缸又以专利的三行程冲压循环改变了传统冲压设备二冲程冲压循环带来的诸多弊端,为这一新的冲压技术奠定了先进的运动学基础。
可看出每一冲压循环均由快进行程、力行程、返回行程三个行程段构成。在快进行程,由前部的快进气缸纯气动驱动上模具快速小力运动,直至在某一位置碰到工件。上模具接触工件后,由工件外阻控制气液增力缸自动开始气液增压的力行程,全力驱动上模具实施冲压加工。完成冲压加工后,转换主控阀,纯气动驱动上模具返回至静止状态,完成返回行程,并处于下一个工作循环准备。
2. 先进的技术性能
三行程气液增压冲压技术及其设备为工业界的冲压加工,尤其是汽车工业的冲压加工,带来了全新的冲压概念和冲压实践。
1)"软到位"冲压技术
在快进行程,仅由气液增力缸前部气缸驱动上模具快速小力接触工件,其接触力极小,大约为额定冲压力的1%~5%,由此实现了冲压行业一直在追求的"软到位"冲压加工。"软到位"冲压技术带来的无冲击振动和噪音的温顺的冲压加工,一方面极大地提高了冲压加工质量,解决了传统冲击式冲压设备无法解决的冲压加工难题,比如打印字号、精密压装、深拉伸加工等。另一方面还保护了冲压模具,降低了冲压模具的设计制造难度,极大地延长了模具的寿命。此外"软到位"冲压技术还简化了对设备安装基础的要求,冲压设备可安装于楼上车间工作,或安装于导轨上或机器人手臂上实现移动式全自动冲压加工,大大降低了专用组合冲压工作站或全自动压力加工生产线的设计制造难度,提高了设备运转的可靠性。
2) "增力自适应"冲压技术
冲压加工中,上模具在空行程任一位置碰到工件,气液增力缸即依此工件外阻,自动转为力行程进行全力冲压加工,实现了更换模具无需设备调整的"自适应"冲压加工。而在力行程实施过程中,气液增力缸依据其气液无极增压原理,可科学地自动适应不同冲压阶段或位置所需不同冲压力的变化要求而施加变化的主动冲压力,解决了传统二行程冲压设备只依据所配置的主动驱动系统而盲目施加过量冲压力所带来的诸如废品率过高或无法实施合格冲压加工等问题。
3) 高效节能
冲压技术将其每一冲压循环依据实际冲压加工中外载的不同而科学合理地分为三个行程段,并对不同行程段中不同外载施加不同的主动冲压力及合理的能量分配,如在空行程及返回行程,只需克服上模具的自重,故此行程段只由前部气缸小力驱动即可。由此极大地降低了设备能耗。 与传统二行程冲压设备相比,相同功能下,冲压设备高节能可达90%。
4) 控制简便可靠,自动化程度高
气液增力缸式冲压设备只需一个二位四通或五通主控气阀即可进行操作控制,气动控制系统简便可靠,标准气液增力缸上配置压力检测接口及提供各种位移检测选择,可自由编程实现冲压过程及冲压质量的全自动无人化监测控制。
3. 应用
气液增力缸式冲压技术及设备已广泛应用于以汽车工业为主的现代工业加工中,其优良的技术性能和依据现代汽车工业生产特点开发的高可靠性高自动化的质量监测及质量保证控制系统,切实有效地满足了现代工业对冲压加工越来越高的要求,实现了免维护长期可靠运转和高质量保证体系的完美结合。目前在国内外每年都有数以万计台气液增力缸式冲压设备或专用组合冲压工作站、冲压机器人以及全自动冲压加工线,取代了传统的冲床和油压机,应用到诸如发动机、变速箱压力装配、车架大梁铆接、车身及板式金属或非金属配件的冲裁、字号打印、螺栓螺母压铆以及车身及四门两盖等板件的冲压连接等各种冲压加工中,极大地提高了汽车产品冲压加工和冲压装配的质量和可靠性,降低了生产成本,提高了生产效率。
无铆钉连接技术是一种逐步取代传统落后连接工艺的新型连接方法。因为至今为止所采用的连接方法均存在着经济上及技术上的不足。仅以电焊为例,它的设备昂贵,连接费用高,很难连接多层板件以及有镀层的板件或铝、铜及不锈钢板件,而对喷漆板件、不同材质板件、厚度差异过大板件以及中间有夹层的板件则无法连接。同事电焊连接破环了板件表面镀层,会产生热变形。并且对连接加工过程中的所有不可靠因素无法进行无损伤的自动检测。
此外,采用传统的连接方法,单件连接成本过高,如在或方法中,准备工作加上相应的输送及零配件成本,就会造成很高的费用。
无铆钉连接技术利用板材压接机和专用连接模具,通过一个瞬间强高压加工过程,依据板件本身材料的冷挤压变形,形成一个具有一定抗拉力和抗剪强度的无应力集中内部镶嵌圆点,即可将不同材质不同厚度的两层或多层板件连接起来。无铆钉连接技术对板件表面无任何要求,连接点处板件表面原有的镀层、漆层不受损伤。连接过程自动化程度高,可单点或多点同时连接,并能进行无损伤连接强度检测及全过程自动监控,生产效率极高。
在无铆钉连接过程中,凸模首先与上层材料接触,材料在上模的压力下,开始往凹模内拉伸变形,同时凹模的活动部分向外张开,以使金属材料充分的在凹模的型腔内变形,形成一个紧密的连接点,然后凸模返程,凹模的活动部分在弹簧力的作用下回到原始位置。
无铆钉连接VS焊接编辑
与无铆钉连接工艺相比,点焊工艺有很多缺点。比如,焊接会烧灼图层面;在焊接镀锌金属板材时会产生有毒烟雾;焊接铝型材的效果也不好。与此相对,无铆钉连接工艺在连接涂层材料时,不会烧灼涂层表面;在压接镀锌材料时,无铆钉连接工艺
也不会释放有害的热量和烟雾;而且连接铝型材和复合金属板材的效果也很好。所以,无铆钉连接工艺比焊接工艺更节约成本。