在飞机上起到的性能影响 航空铝件的精度要求较高,所以在铣削的过程中需要基于精度做具体的操作,这样,件的质量才能够得到保证。就现阶段的航空铝件铣削加工来看,件存在着明显的变形,这种变形情况的存在对件的质量提升十分不利,对其的安全利用也会产生显著的影响,所以需要对变形做有效。从现实分析来看,对具体的变形做预测分析,然后给予预测做相应的铣削参数调整,变形情况能够做到有效遏制。基于数字图像相关,研究了老龄飞机机身外蒙皮含铆钉孔和裂纹的-T3铝板材剩余强度性能。首先,通过拉伸实验研究了铆钉孔行距和列距对剩余强度的影响;其次,预制了4类裂纹,模拟飞机蒙皮多部位损伤现象,分析了其向变化对含交错孔试样剩余强度影响,并进一步对裂纹扩展路径进行了讨论;最后,对净截面屈服准则进行了修正。结果表明:剩余强度随着铆钉孔列距的增加而增大。当列距一定时,试样剩余强度随行距的增大而升高,当行距大于32 mm时,剩余强度出现下降。修正后的净截面屈服准则可以较好地预测含多部位损伤交错孔结构的剩余强度值,预测误差在8%以内。针对A-型材结构件,利用ABAQUS软件建立π型截面型材拉弯成形有限元模型,对该铝型材结构件拉弯成形进行数值模拟,并分析预拉量、补拉量、弯曲半径及摩擦系数的变化对回弹的影响。结果表明:预拉量、补拉量、弯曲半径和摩系数都会影响回弹量,在相对应的变化范围内,回弹随着预拉量、补拉量的增大有明显减小的,而回弹量与弯曲半径和摩擦系数均呈正相关。其中对回弹量的变化影响较为明显的为拉伸量;当预拉量为1%,补拉量为2%,摩擦系数为0.08,弯曲半径为200 mm时,回弹最小。采用快速超塑成形对高铁车辆侧壁外板进行成形试验,结果表明,其生产效率高、成本低,能够成功解决传统冲压工艺无法实现复杂空间曲面铝零件以及传统超塑成形工艺成形周期长、效率低的难题。通过系列试验研究,确定了热冲压工艺与超塑成形工艺相结合的快速超塑成形,成功使用厚度为4 mm的工业用铝薄板制造了圆角极小(R≤4 mm)的高铁边缘蒙皮和直壁拉深成形的大型地铁门框零件(h≈80 mm),该成形件具有尺寸精度高、壁厚分布均匀、形状稳定性高等优点,同时其力学性能满足使用要求。定做6061-t6铝管,厚壁铝管铝型材CNC深加工,空心铝管折弯

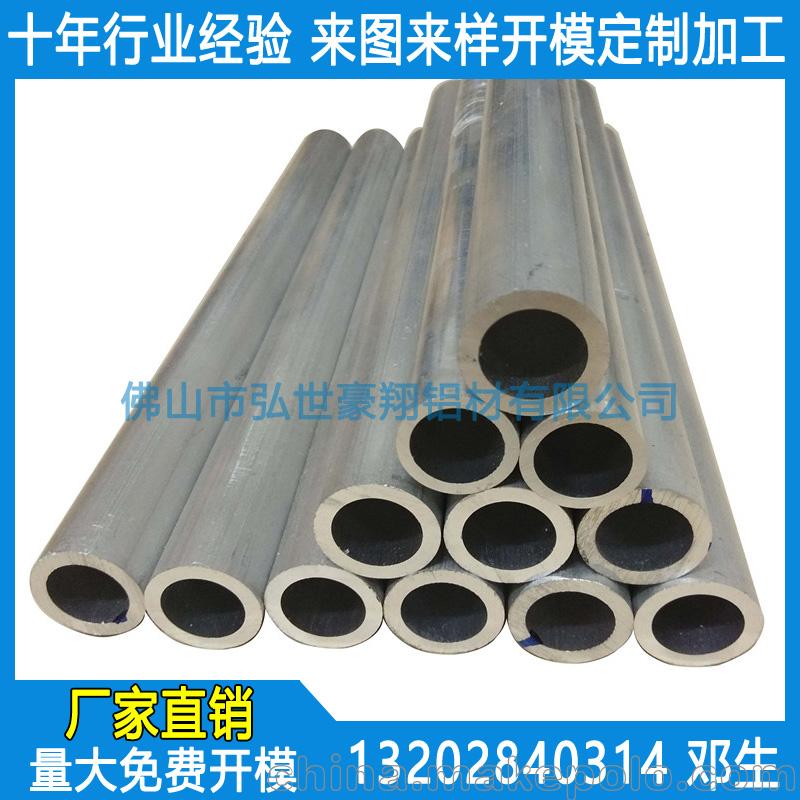
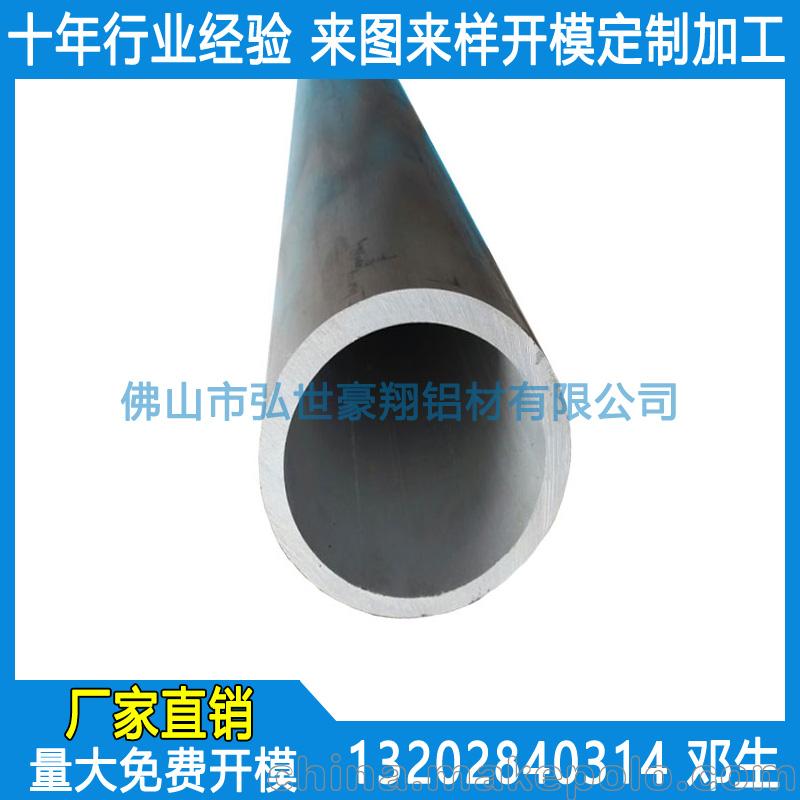