耐火粘土的化学成分是影响其质量的重要因素之一。Al2O3是耐火粘土的有益组分,主要赋存于氢氧化铝矿物(一水硬铝石、勃姆石、三水铝石),其次赋存于铝硅酸盐矿物(高岭石、伊利石、蒙脱石等)中。一般来说,软质和半软质粘土含Al2O3为22%~38%,硬质粘土为35%~50%,高铝粘土为55%~70%。SiO2主要赋存于粘土矿物中,亦有微量的原生石英残屑存在。SiO2含量变化较大,高铝粘土中一般为3%~35%,硬质粘土中为43%~66%。Fe2O3主要赋存于赤铁矿、磁铁矿、针铁矿、菱铁矿中,是耐火粘土的主要有害成分。Fe2O3含量无明显规律,高铝粘土中含量在0.5%~2.2%,硬质粘土中含量在0.5%~2.5%,软质粘土中一般为1.0%~2.5%。K2O和Na2O也是耐火粘土的有害杂质,主要赋存于伊利石和云母类等矿物中,含量变化较大。CaO和MgO等虽为有害杂质,但含量一般甚微。
【耐火粘土的分类】
耐火粘土按可塑性、矿石特征和工业用途分为软质粘土、半软质粘土、硬质粘土和高铝粘土四种。软质粘土一般呈土状,在水中易分散,与液体拌合后能形成可塑性泥团;半软质粘土的浸散性较差,其浸散部分与液体拌合后亦可形成可塑性泥团。这二种粘土在制作耐火制品时常用作结合剂。硬质粘土常呈块状或板片状,一般在水中不浸散,耐火度较高,为耐火制品的主要原料。高铝粘土Al2O3的含量较高,硬度和比重较大,耐火度高,常用以制造高级粘土制品。
【耐火粘土的应用】
耐火粘土主要用于冶金工业,作为生产定型耐火材料(各种规格的砖材)和不定型耐火材料的原料,用量约占全部耐火材料的70%。耐火粘土中的硬质粘土用于制作高炉耐火材料,炼铁炉、热风炉、盛钢桶的衬砖、塞头砖。高铝粘土用于制作电炉、高炉用的铝砖、高铝衬砖及高铝耐火泥。硬质粘土和高铝粘土常在高温(1400~1800℃)煅烧成熟料使用。
粘土火泥是由煅烧粘土(熟料)、废粘土砖粉和结合粘土(生料)配制而成的。熟料是粘土火泥的主要成分,约占75%~80%,生粘土是结合剂,它的加入是为了增加粘土火泥的可塑性,降低透气性和失水率。但配入量不宜过大,否则易产生裂纹,以配入20%~25%为宜。粘土火泥在温度低于1000℃的焦炉上使用。
砌筑焦炉用的耐火泥,要求在常温下具有良好的可塑性和粘结性,以利施工;干燥后具有较小的收缩性,防止开裂;在使用温度下能发生烧结或固结,有一定的强度,以保证炉体的坚固性和严密性;其耐火度和荷重软化温度应高于使用温度。炼焦炉用耐火泥分为硅火泥和粘土火泥。砌筑硅砖时用硅火泥,砌筑粘土砖时用粘土火泥。硅火泥是由硅石、废硅砖和结合粘土配制而成的。硅石是主要成分,硅石中SiO2含量较高耐火度就越高。加入废硅砖粉是为了改善硅火泥与硅砖的高温粘结能力,因废硅砖粉与硅砖的膨胀基本相同,可使砖缝贴靠砖面。在硅火泥中废硅砖粉含量在20%~30%之间。硅火泥中加入结合粘土,可增加火泥的可塑性,降低透气性和失水率,一般加入量为15%~20%左右。
砌筑焦炉时,根据各部位的砖种和温度的不同而采用不同的耐火泥。从燃烧室顶部到斜道区中、上部采用中温硅火泥,从斜道区下部到蓄热室中部采用低温硅火泥,蓄热室下部则采用加有水玻璃的低温硅火泥。粘土火泥主要用于砌筑粘土砖部位和修补焦炉。
耐火粘土在建材工业上用以制作水泥窑和玻璃熔窑用的高铝砖、磷酸盐高铝耐火砖、高铝质熔铸砖。高铝粘土经过煅烧,然后与石灰石混合制成含铝水泥,这种水泥具有速凝能力及防蚀性和耐热力强的特点.
耐火粘土在研磨工业、化工工业和陶瓷工业等方面也有重要的用途。高铝粘土经过在电弧炉中熔融,制造研磨材料,其中电熔刚玉磨料是目前应用最广泛的一种磨料,占全部磨料产品的2/3。高铝粘土可以用来生产各种铝化合物,如硫酸铝、氢氧化铝、氯化铝、硫酸钾铝等化工产品。在陶瓷工业中,硬质粘土和半硬质粘土可以作为制造日用陶瓷、建筑瓷和工业瓷的原材料。
高铝粘土还用于油井中,作为净化石油用的支撑剂,在农业上作为促肥剂,以及用作抗滑、抗磨的铺路材料,等等。硬质粘土还用于制新型耐火绝热材料——耐火纤维,它具有耐高温、导热系数小、耐酸碱、吸音和质轻等优点,在冶金、机械、电子、玻璃、陶瓷等工业上应用广泛。
耐 火 粘 土 细 粉 理 化 指 标
指标/品级 | 特级 | 一级 | 二级 | 三级 |
Ai2O3% min | 31 | 29 | 27 | 25 |
Fe2O3% max | 1.2 | 1.6 | 2.0 | 2.5 |
耐火度℃min | 1710 | 1680 | 1630 | 1580 |
烧失量% | 0.9 | 11 | 13 | 15 |
关于邮费问题请亲咨询我们,期待与您的合作。
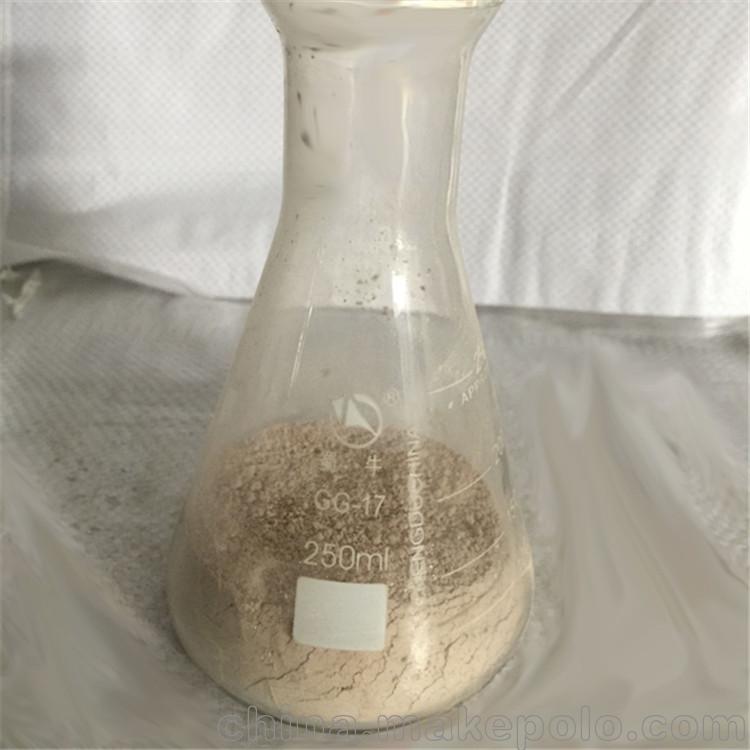

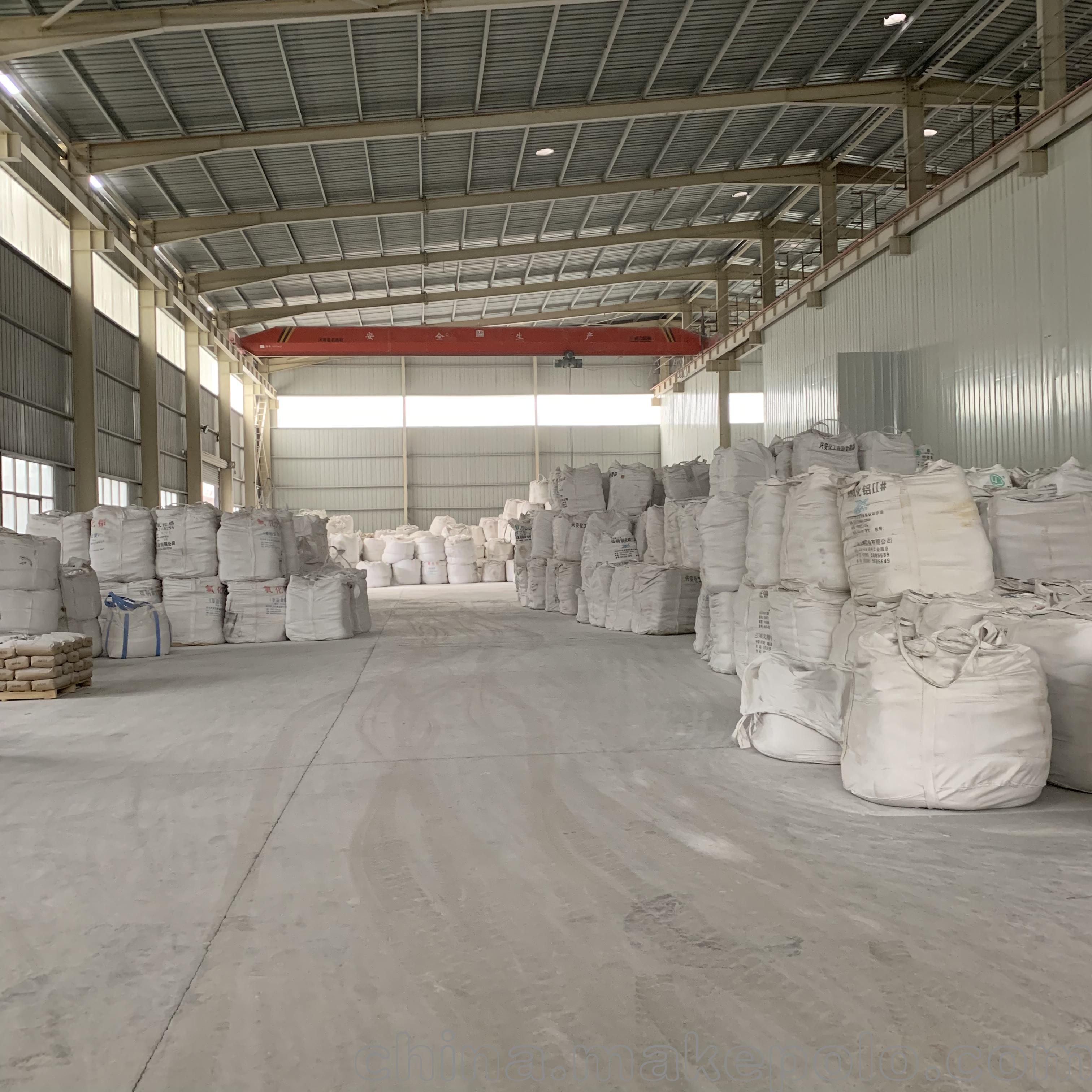