西安切片试验集成电路失效分析
切片试验(Slice Test),也称为横截面分析(Cross-Sectional Analysis),是一种破坏性测试技术,广泛应用于电子元器件的质量管控中。它通过对样品进行切割、研磨、抛光和蚀刻处理,然后使用显微镜(如光学显微镜或扫描电子显微镜)观察其内部微观结构,从而评估材料性能、工艺缺陷和可靠性。这种方法能够揭示肉眼无法看到的隐藏问题,如焊接异常、层间结合不良或微小裂纹,为制造过程提供关键的质量验证依据。切片试验的核心优势在于其高精度和直观性,但需注意它是破坏性的——样品无法复原,通常在抽样检查或失效分析中使用。
切片试验步骤
-
样品制备:选择代表性样品,用金刚石锯或激光切割机将其切割成薄片(厚度通常在毫米级)。
-
包埋固化:将样品嵌入环氧树脂或类似材料中,以提高稳定性并防止变形。
-
研磨抛光:使用砂纸或研磨盘逐步打磨至镜面光滑,确保表面平整无划痕。
-
蚀刻处理:针对不同材料(如金属或陶瓷)施加化学蚀刻剂,以增强微观结构的对比度。
-
显微观察:在高倍显微镜下分析截面,测量层厚、检查缺陷,并记录图像数据。
切片试验在电子元器件质量管控中的应用
-
焊接质量评估(如SMT焊点和BGA焊接)
-
用于检测表面贴装技术(SMT)和球栅阵列(BGA)焊点的内部缺陷,如虚焊、空洞(voids)、裂纹或焊料不足。切片试验能直观显示焊点内部的微观结构,确保电气连接可靠。这在智能手机、计算机主板的生产中尤为重要,能预防因焊接失效导致的设备短路或功能故障。
-
多层结构分析(如PCB和芯片封装内部检查)
-
应用于印刷电路板(PCB)和集成电路(IC)封装的质量管控,切片试验可评估层压板、铜线路、介电层或硅芯片的厚度均匀性、分层(delamination)和界面结合强度。例如,在高密度互连(HDI)PCB中,它能识别层间微裂纹或孔壁镀铜不均,从而优化蚀刻工艺,避免信号传输问题。
-
缺陷识别与工艺验证(包括空洞、裂纹和异物分析)
-
针对制造过程中的常见缺陷,如电镀气泡、材料夹杂物或热应力裂纹,切片试验提供微观证据,帮助追溯工艺问题(如回流焊温度不当或材料污染)。此场景广泛应用于半导体器件、连接器和被动元件(如电阻电容)的生产线,支持快速故障排查和质量改进。
-
镀层厚度测量和成分分析(如金属镀层和涂层)
-
用于精确测量金、镍、铜等金属镀层的厚度和均匀性,确保其符合设计规范(如防止氧化或腐蚀)。切片试验结合能谱仪(EDS)还能分析镀层成分,检查杂质扩散(如Kirkendall空洞),这在接插件、端子或射频元器件的可靠性测试中必不可少。
-
失效分析与可靠性验证
-
当元器件在测试或使用中失效时,切片试验是失效分析的核心工具。它能定位故障根源,如内部短路、老化裂纹或因环境应力(热循环或振动)导致的微观损伤。此场景应用于汽车电子、航空航天等高可靠性领域,帮助验证产品寿命和设计缺陷,减少召回风险。
切片试验虽强大,但需结合其他非破坏性测试(如X射线或自动光学检测)以优化质量管控体系。其局限性包括高成本和破坏性,因此建议在关键工序或批次抽样中使用。随着技术进步,自动化切片设备(如精密切割机)正提升效率,使其在5G、物联网等高密度电子制造中更显重要。总之,切片试验是电子元器件质量管控的“显微镜”,能显著提升产品良率和可靠性,减少潜在失效带来的经济损失。
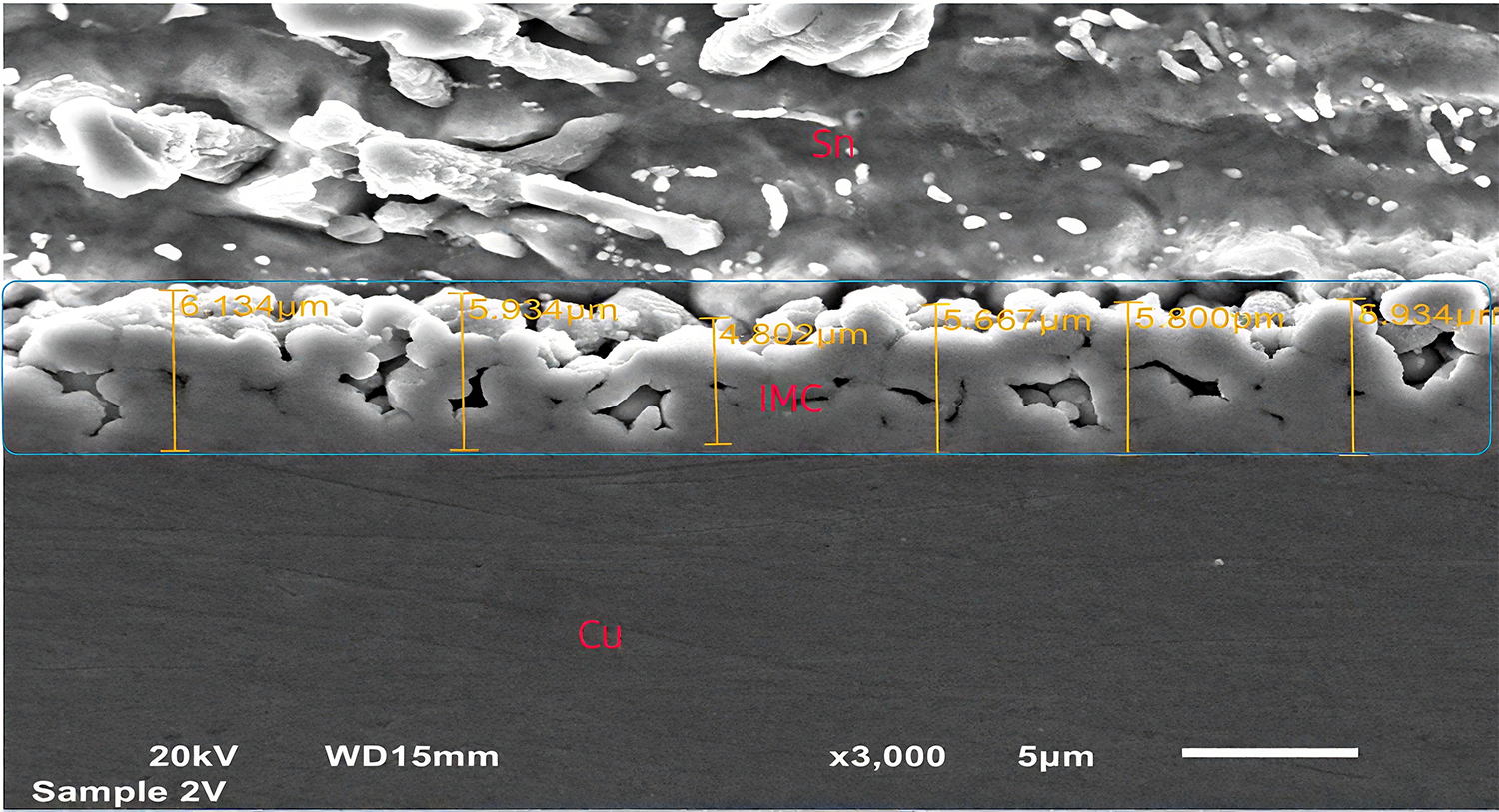
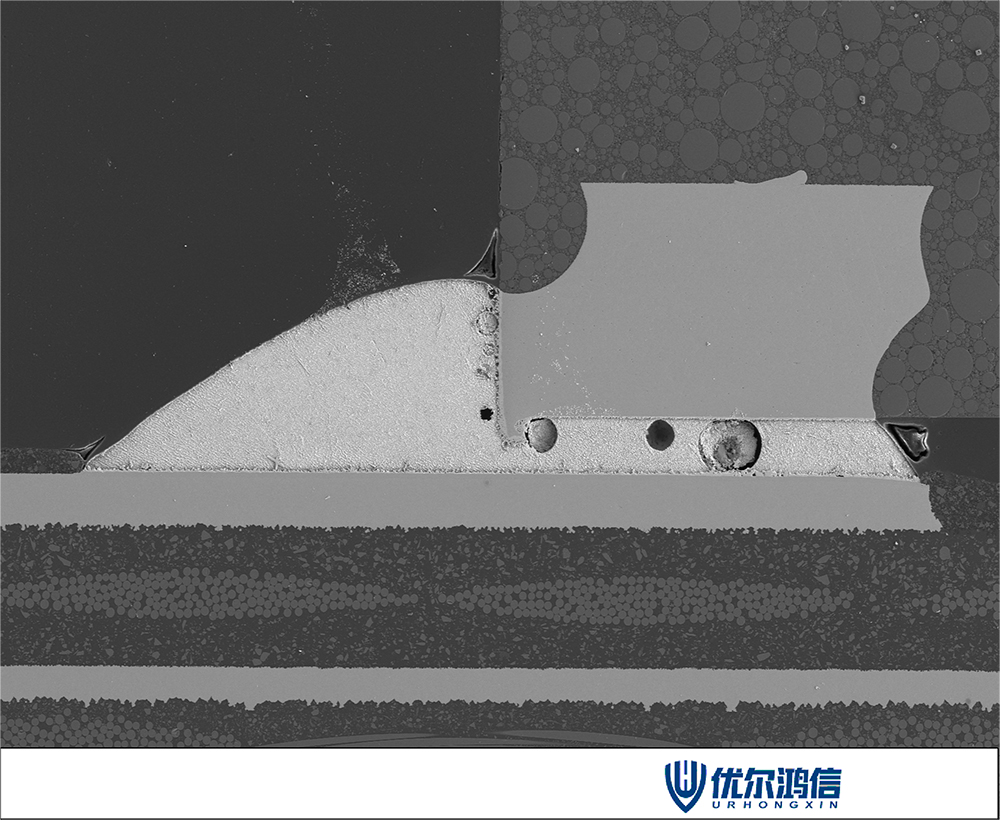
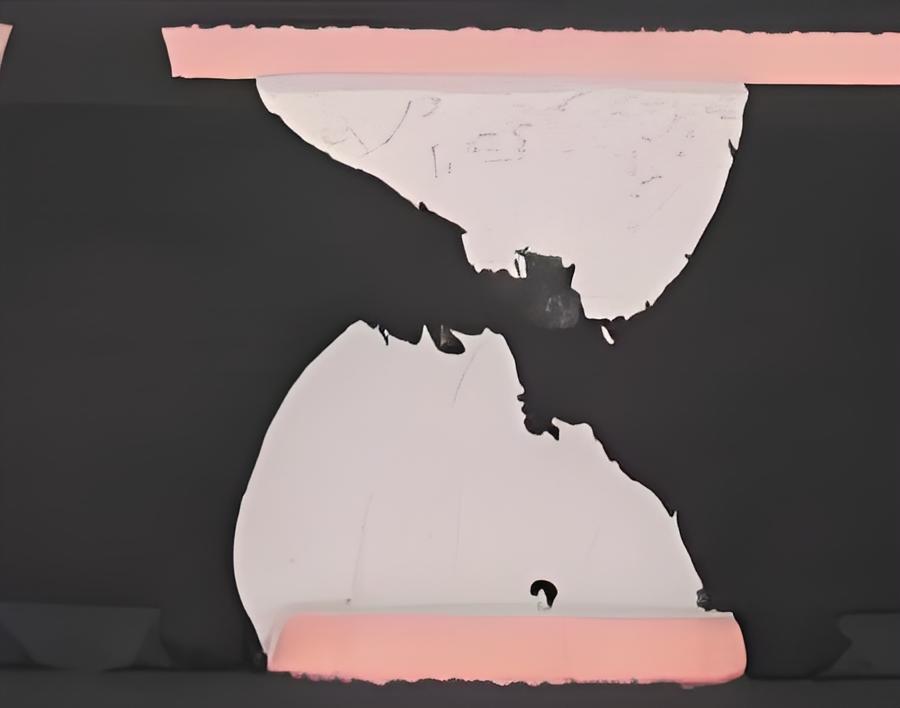