什么是切片试验?
切片试验(Cross-section Test)是一种通过取样、固封、研磨、抛光等步骤,将电子元器件或电路板的样品制成薄片,以观察其内部结构和缺陷的检测方法。其核心目的是通过显微镜或电子显微镜等工具,分析样品的微观结构、材料分布、工艺缺陷等,从而评估产品的质量、可靠性和失效原因。
切片试验的基本流程:
-
取样:从电子元器件或电路板上选取具有代表性的区域(如关键电路、焊接点等)。
-
固封:用液态树脂包裹样品,固化后形成稳定的块状样品。
-
切割与研磨:使用精密切割机将样品切割成薄片,并通过不同粒度的砂纸逐步研磨至表面平整。
-
抛光:用抛光膏使样品表面达到镜面效果,便于观察。
-
腐蚀处理(可选):通过化学腐蚀增强微观结构的对比度。
-
观察与分析:利用金相显微镜、扫描电镜(SEM)等设备观察样品的微观结构,记录缺陷并测量参数(如镀层厚度、焊点尺寸等)。
切片试验在电子元器件质量管控中的应用
切片试验广泛应用于电子元器件和电路板的生产、检测及失效分析中,具体场景包括:
1. PCB/PCBA结构缺陷检测
-
层间分离:检查多层PCB的层间对齐度、压合质量是否合格(如分层、孔铜断裂等)。
-
镀层质量评估:检测PCB表面及内部的镀层厚度、均匀性、附着力,防止因镀层缺陷导致电气性能下降。
-
过孔缺陷分析:观察过孔的镀铜均匀性、裂纹、空洞等问题,评估其对导电性和机械强度的影响。
2. 焊接质量检测(PCBA)
-
BGA/SMT焊接缺陷:分析焊点是否存在空焊、虚焊、桥接、焊料球等问题。
-
润湿性与焊料填充:评估焊料的润湿效果、填充程度,判断焊接工艺的可靠性。
-
焊点尺寸与形态:测量焊点高度、宽度等参数,确保符合设计要求。
3. 材料与工艺分析
-
材料内部结构剖析:解析电容、LED、传感器等元件的内部结构(如铜箔层数、电镀工艺等)。
-
微小尺寸测量:检测气孔大小、上锡高度、铜箔厚度等微米级参数(通常大于1μm)。
-
镀层工艺验证:评估电镀或化学镀层的均匀性、覆盖范围及结合力。
4. 失效分析与故障定位
-
开裂、分层定位:通过切片验证无损检测(如X-ray、SAM)发现的疑似异常(如开裂、异物嵌入等)。
-
失效机理研究:结合化学分析(如EDS)和显微观察,确定失效的根本原因(如腐蚀、污染、工艺缺陷等)。
-
软件与硬件协同诊断:对于复杂嵌入式系统,切片试验可辅助定位硬件缺陷,排除软件逻辑错误的影响。
5. 工艺优化与质量控制
-
制程改善验证:通过切片试验验证改进后的工艺(如焊接温度、镀层参数)是否有效减少缺陷。
-
供应商质量管控:对采购的电子元器件进行切片抽检,确保其符合设计规范和行业标准(如IPC-TM-650)。
-
研发阶段验证:在新产品开发中,通过切片试验验证设计合理性及工艺可行性。
切片试验的典型检测标准
-
IPC-TM-650 2.1.1:金相切片的制备和检验方法。
-
IPC-TM-650 2.2.5:焊接质量检测标准。
-
IPC-A-600/610:PCB及PCBA的可接受性标准。
-
ASTM E3:金属材料的金相检验标准。
切片试验是电子元器件和电路板质量管控中不可或缺的技术手段,尤其适用于以下场景:
-
缺陷检测:如分层、空洞、焊点不良等。
-
工艺验证:优化焊接、电镀等关键工艺参数。
-
失效分析:定位故障根源,指导设计改进。
-
质量追溯:通过微观结构分析追溯生产过程中的问题。
通过切片试验,企业能够显著提升产品可靠性,降低故障率,并满足认证(如CE、RoHS)的要求。
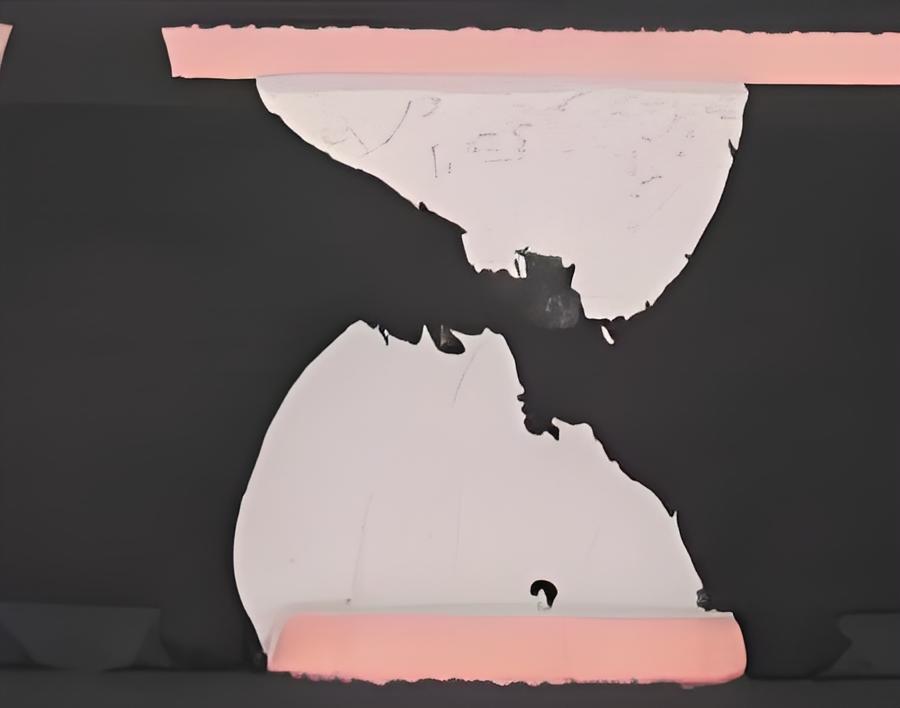
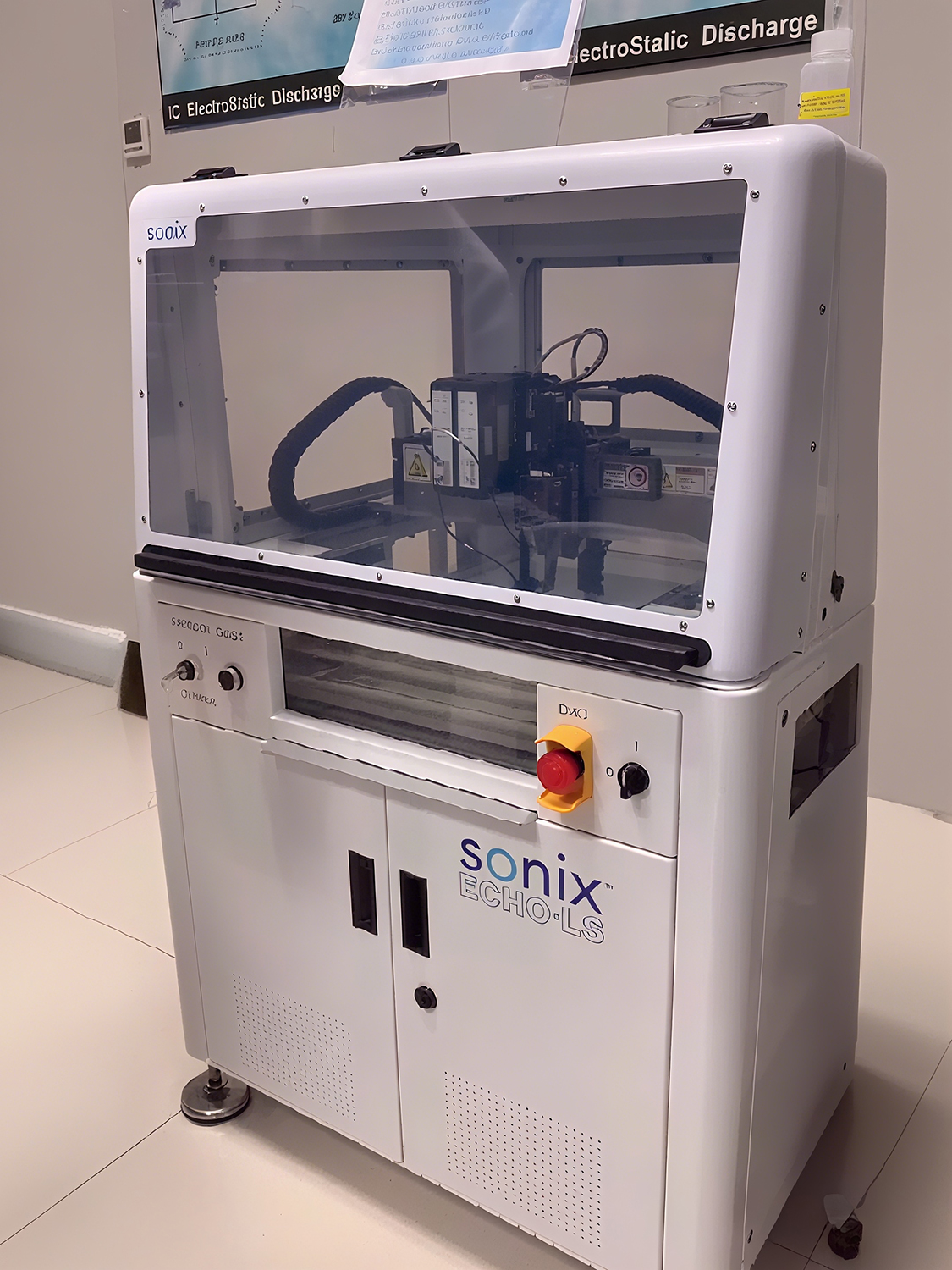
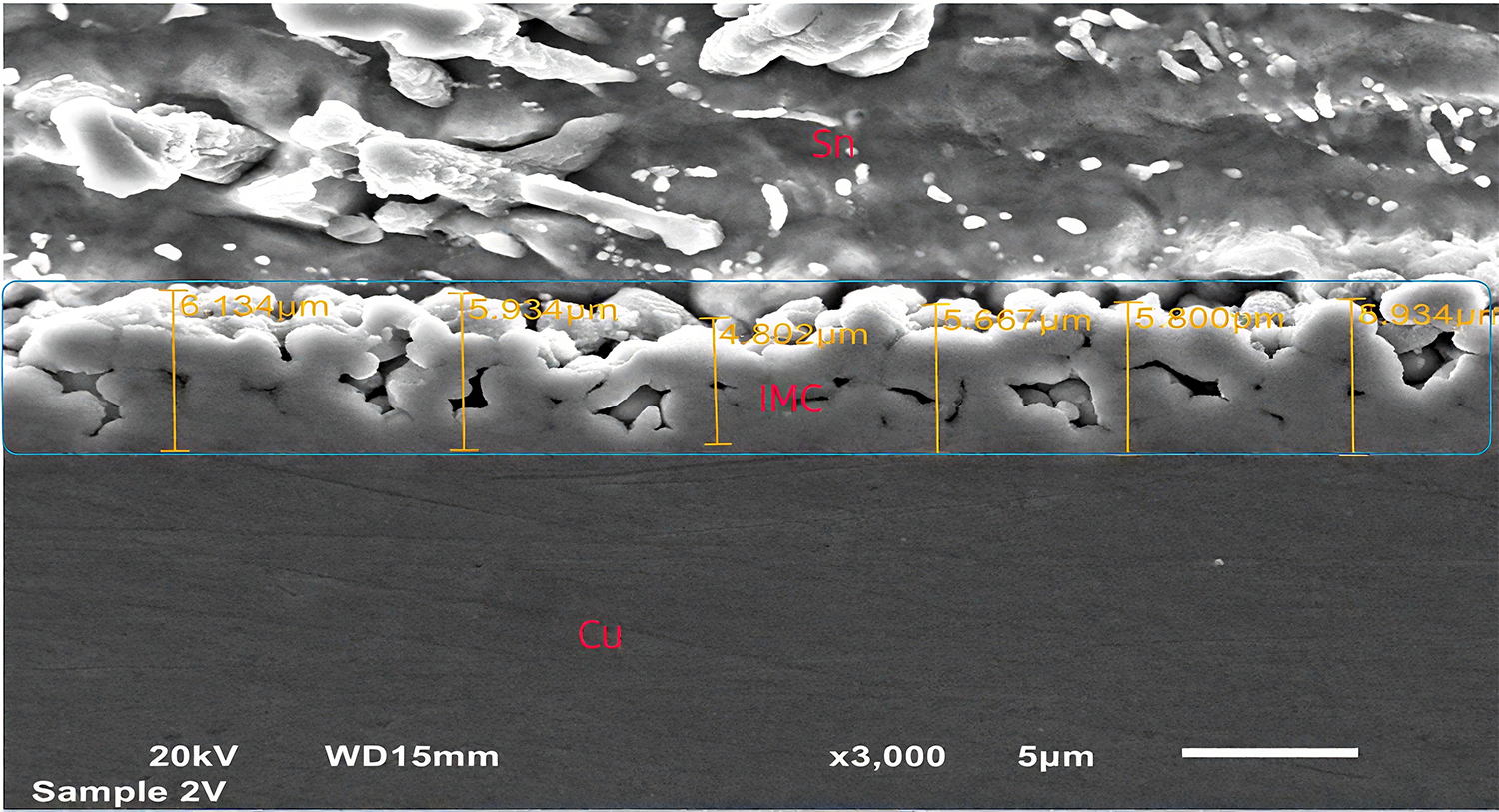