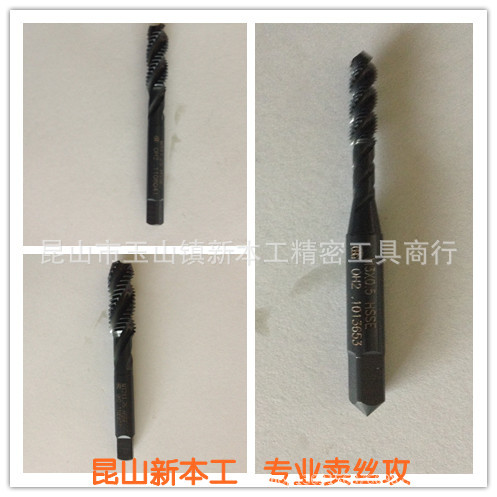
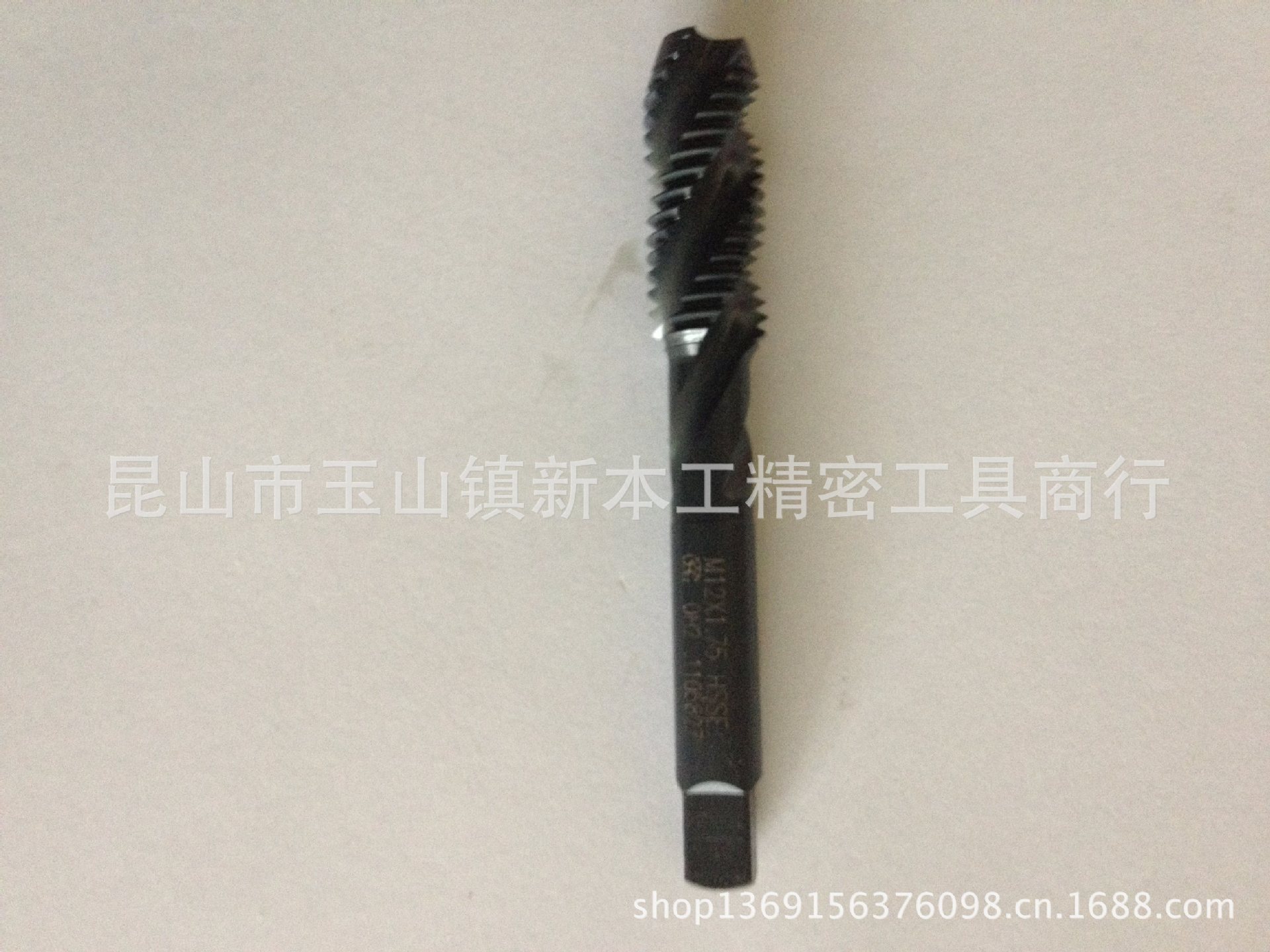

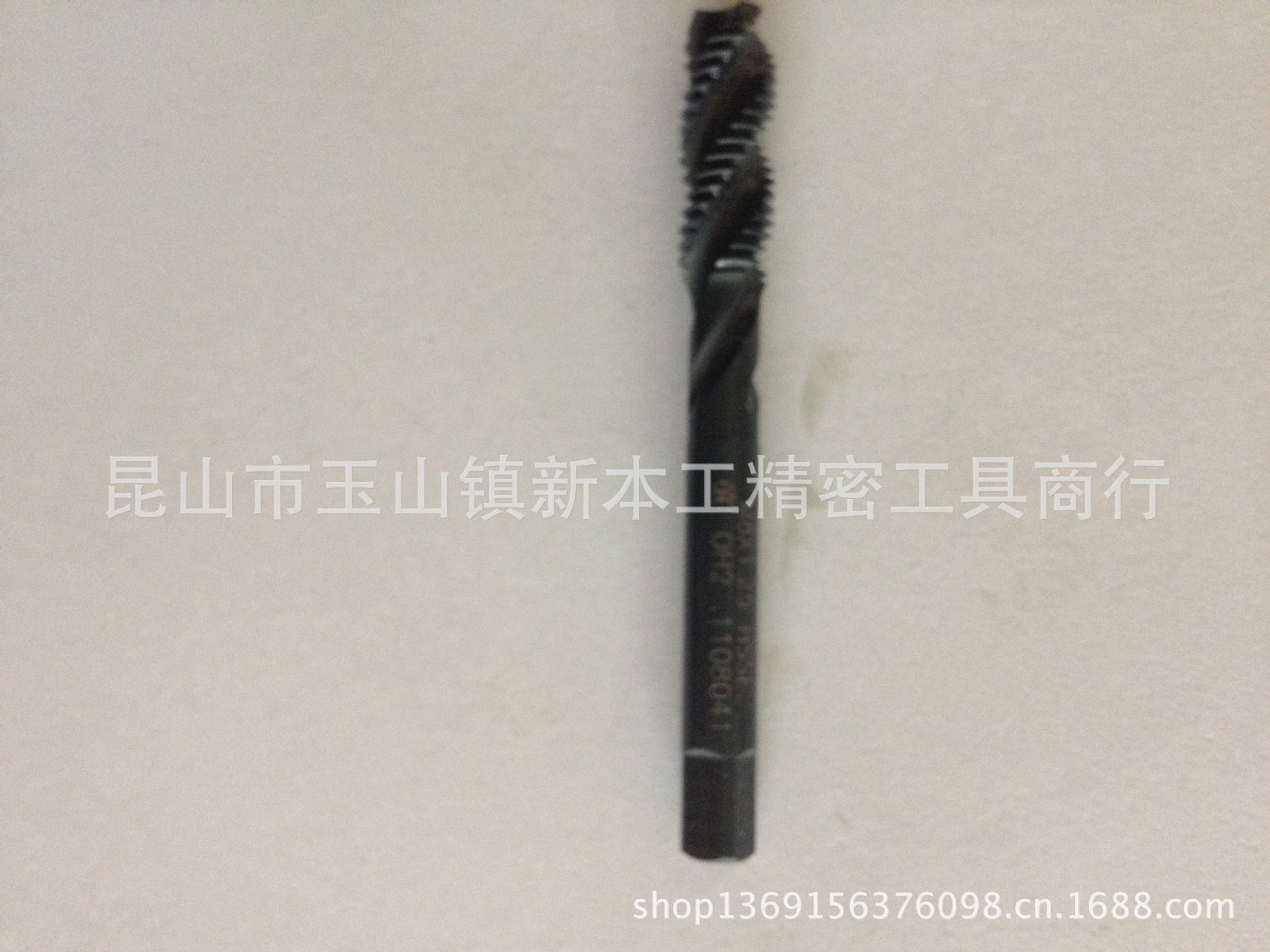
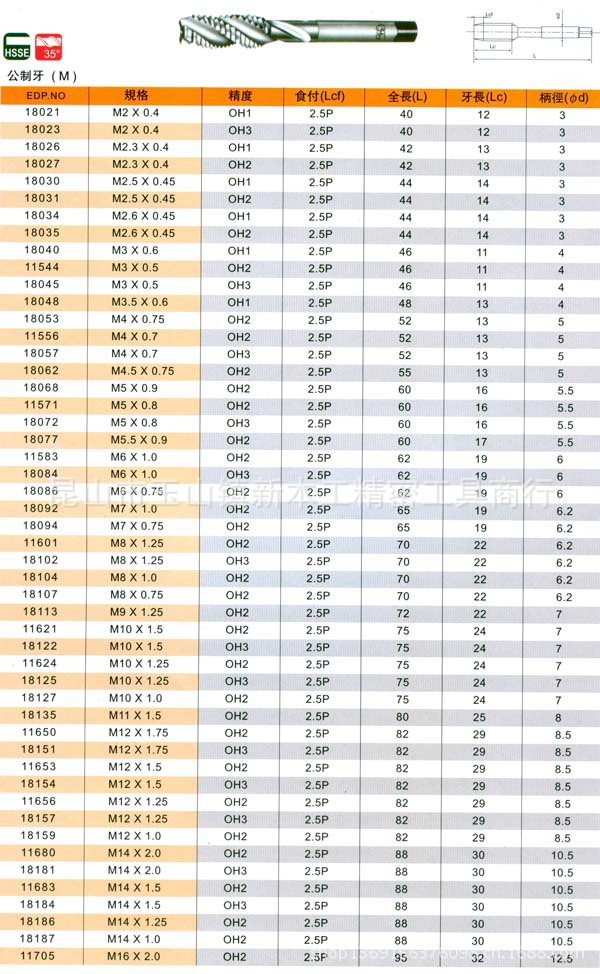
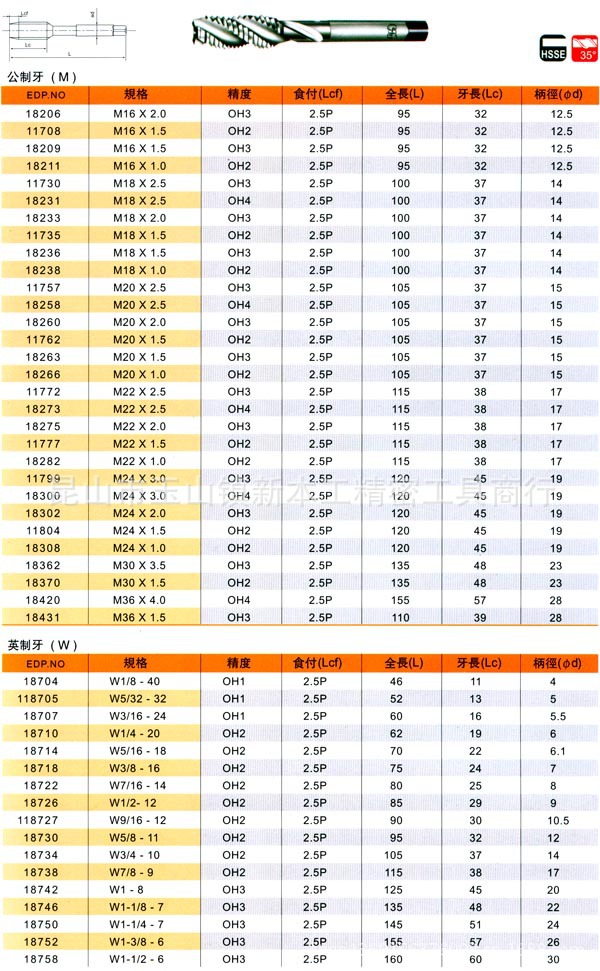
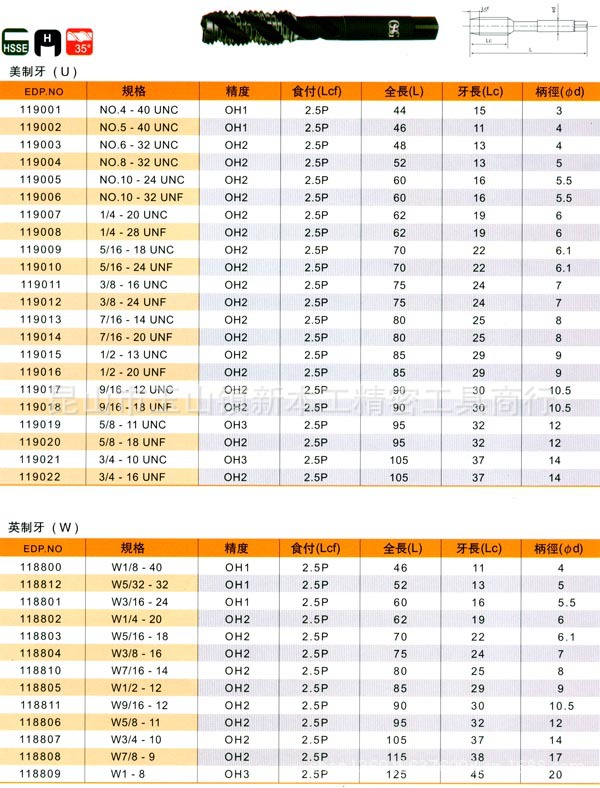
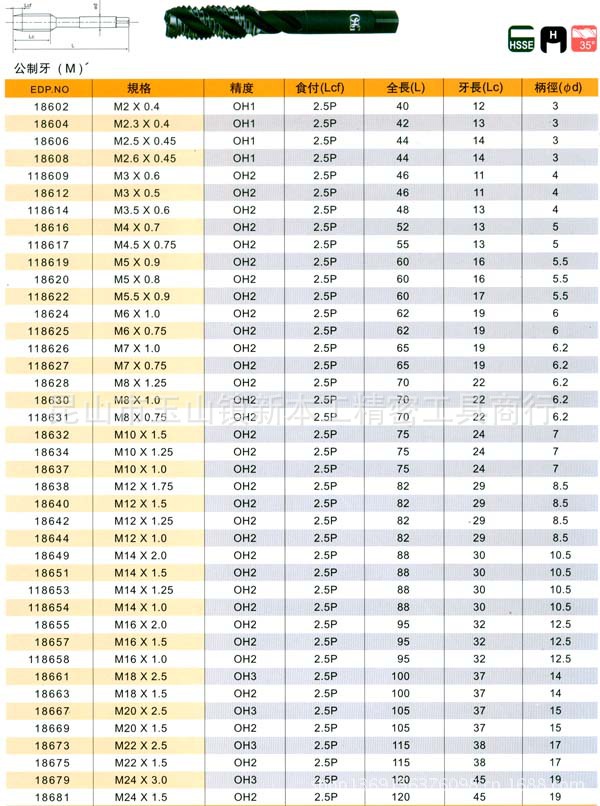
丝锥在攻丝过程中常见问题包括:1、丝锥折断;2、丝锥崩齿;3、丝锥磨损过快;4、螺纹中径过大;5、螺纹中径过小;6、螺纹表面粗糙度值过大。
产生的原因
丝锥折断:螺纹底孔加工时直径偏小,排屑不好造成切屑堵塞;攻不通螺纹时,钻孔的深度不够;攻螺纹时切削速度太高过快;攻螺纹用的丝锥与螺纹底孔直径不同轴;丝锥刃磨参数的选择不合适,被加工件硬度不稳定;丝锥使用时间过长,过度磨损。
丝锥崩齿:丝锥前角选择过大;丝锥每齿切削厚度太大;丝锥的淬火硬度过高;丝锥使用时间过长而磨损严重。
丝锥磨损过快:攻螺纹时切削速度过高;丝锥刃磨参数选择不合适;切削液选择不当,切削液不充分;工件的材料硬度过高;丝锥刃磨时,产生烧伤现象。
螺纹中径过大:丝锥的中径精度等级选择不当;切削选择不合理;攻螺纹切削速度过高;丝锥与工件的螺纹底孔同轴度差;丝锥刃磨的参数选择不合适;刃磨丝锥中产生毛刺,丝锥切削锥长度过短。
螺纹中径过小:丝锥的中径精度等级选择不当;丝锥刃磨参数选择不合理,丝锥磨损;切削液选择不合适。
螺纹表面粗糙度值过大:丝锥的刃磨参数选择不合适;工件材料硬度过低;丝锥刃磨质量不好;切削液选择不合理;攻螺纹时切削速度过高;丝锥使用时间过长磨损大。
解决的方法
丝锥折断:正确地选择螺纹底孔的直径;刃磨刃倾角或选用螺旋槽丝锥;钻底孔的深度要达到规定的标准;适当降低切削速度,按标准选取;攻螺纹时校正丝锥与底孔,保证其同轴度符合要求,并且选用浮动攻螺纹夹头;增大丝锥前角,缩短切削锥长度;保证工件硬度符合要求,选用保险夹头;发现丝锥磨损应及时更换。
丝锥崩齿:适当减少丝锥前角;适当增加切削锥的长度;降低硬度并及时更换丝锥。
丝锥磨损过快:适当降低切削速度;减少丝锥前角,加长切削锥的长度;选用润滑性好的切削液;对被加工件进行适当的热处理;正确地刃磨丝锥。
螺纹中径过大:选择合理精度等级的丝锥中径;选择适宜的切削液并适当降低切削速度;攻螺纹时校正丝锥和螺纹底孔的同轴度,采用浮动夹头;适当减少前角与切削锥后角;清除刃磨丝锥产生的毛刺,并适当增加切削锥长度。
螺纹中径过小:选择适宜精度等级的丝锥中径;适当加大丝锥前角和切削锥角;更换磨损过大的丝锥;选用润滑性好的切削液。
螺纹表面粗糙度值过大:适当加大丝锥前角,减少切削锥角;进行热处理,适当提高工件硬度,保证丝锥前刀面有较低的表面粗糙度值选择润滑性好的切削液;适当降低切削速度;更换已磨损的丝锥。