'
脱硫增效剂简介
技术背景
石灰石-石膏湿法烟气脱硫工艺因其技术成熟、脱硫效率高,吸收剂来源丰富,价格低廉,副产品可利用等特点而被广泛采用,成为目前燃煤电厂烟气脱硫应用最广泛的方法。由于石灰石本身的性质及工艺限制,石灰石-石膏湿法烟气脱硫工艺也存在着能耗、效率等等问题。针对以上情况,我们开发了脱硫增效剂,用于优化脱硫过程,提高FGD系统的脱硫性能,使其能适应各种含硫量的煤种,降低系统能量损耗,给电厂带来良好的经济和社会效益。
脱硫增效剂的主要成份
脱硫增效剂主要成份有:CaCO3表面活化剂、反应催化剂、化学隧道形成剂。
★ 表面活化剂:改变固液界面湿润性,提高界面传质效率;
★ 反应催化剂:降低反应能,提高反应速度;
★ 化学隧道形成剂:形成CaCO3的微球内部化学隧道,将反应从平面推向立体,进一步提高吸收剂利用效率和加快反应速度。
脱硫增效剂原理
在脱硫过程中,石灰石与硫的反应速度受控于CaCO3的溶解速度,CaCO3在水中的溶解度较小,克服或改善CaCO3在水中的溶解问题,将会对整个脱硫工艺有较大的改善提高。由于CaCO3在水中的溶解度较小,在吸收塔中大量的CaCO3是以微小颗粒状存在的,经研究发现,在这些微球表面,存在着双膜效应,严重影响了液体中硫的传质,采用针对CaCO3表面物性的活性剂和催化剂来减弱和消除双膜效应,同时配合化学隧道形成剂来渗透进入CaCO3的微球表面遍布的微孔和裂纹,制造无数的从微球体表面到内部的隧道,使得液体中硫的传质从这些微孔和裂纹顺利引入,大大加快了石灰石与硫的反应速度。
电镜照片:CaCO3 微颗粒形状
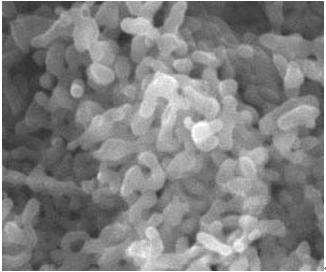
电镜照片:CaCO3 表面的固液界面
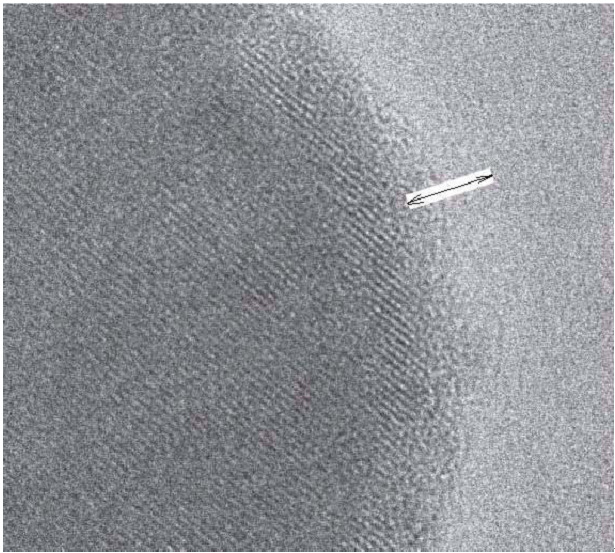
脱硫增效剂的应用效果
★ 提高脱硫效率
添加脱硫增效剂在一般情况下可提高烟气脱硫效率5%-10%左右,这对一直达不到设计脱硫效率的机组是一种很好的解决办法。
★ 减少浆液循环强度
在不降低脱硫效率的同时,添加脱硫增效剂后可降低浆液循环强度四分之一到三分之一,降低系统的液气比,显著降低脱硫系统能耗,并能减少烟气带出水滴对减轻后级设备的结垢堵塞有一定好处。
★ 适应广泛的煤种
可以适应高硫份的燃煤,当燃煤含硫量超过设计工况时,通过添加脱硫增效剂,使系统能适应燃用高硫煤的运行工况,从而降低发电成本。
脱硫增效剂的使用方法
★ 脱硫增效剂加入方法
可在浆液循环回路的任意位置加入,根据电厂实际情况提出具体方案。 推荐: 首次加入系统从浆液返回管处直接加入吸收塔内;后期补充投加时可在地坑中加入。
★ 脱硫增效剂的用量
一般首次加入量为一吨1kg-1.5kg,由于各厂脱硫系统各不相同,燃用煤种硫份含量不同,添加量需根据实际情况调整。 脱硫增效剂的用量由两部分组成:一是首次用量,二是补充用量。
脱硫增效剂应用案例简介
贵州某电厂:2012年9月在#3机组(330MW)脱硫系统(四层喷淋层,设计原烟气SO2浓度:1750mg/Nm3)进行了试验,试验结果如下:
① .提高脱硫效率的试验
机组负荷:315.5MW,原烟气SO2浓度:1935~2366 mg/Nm3
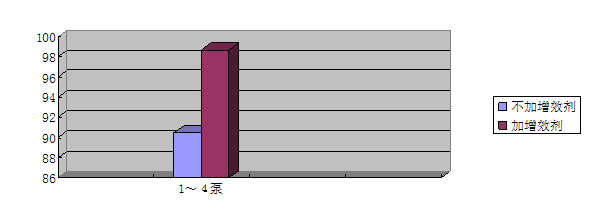
②. 节能试验
机组负荷:310.7MW,原烟气SO2浓度:1885~2235 mg/Nm3
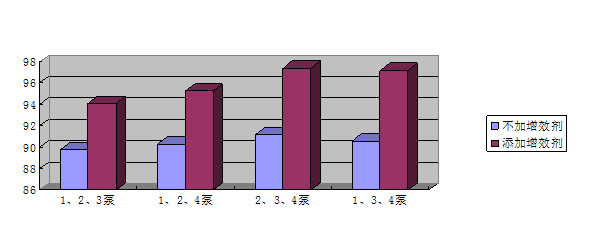
③. 试验结果
a.脱硫系统加入增效剂比不加增效剂提高脱硫效率5~10个百分点。
b.试验期间,浆液PH值稳定,未出现明显下降的状况。
c.脱硫系统加入增效剂后,可以停运至少一台浆液循环泵运行,其功率为450KW,按运行5000小时计算,约可节电225000KWh,折合金额90万元。
e.使用脱硫增效剂,提高了脱硫系统对燃煤含硫升高的适应能力,有利于降低燃煤的采购成本。
f.试验期间,未发现脱硫增效剂对石膏品质有不良影响。
'