
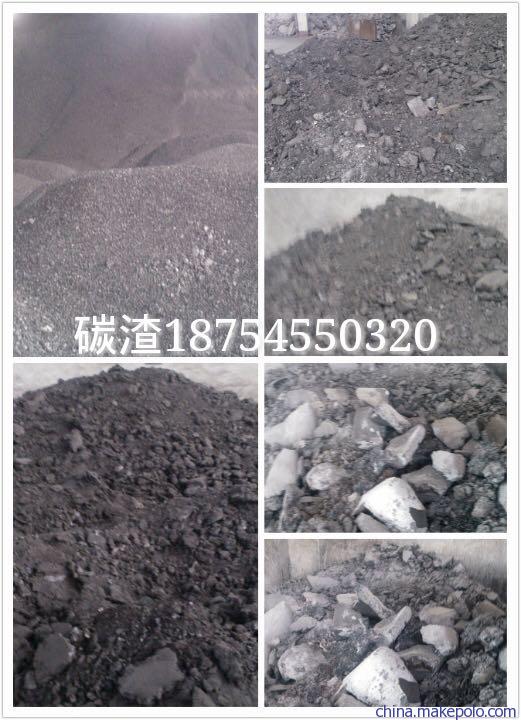


炭渣可以从阳极、阴极以及电解过程中铝的二次反应等途径产生。炭阳极在电解过程中的选择性氧化,阴极炭块的剥落掉渣,当电角质对炭渣湿润性较好时,两者分离能力差,炭渣悬浮在电解质中,与电解质混在一起不易分离,电解质熔体发黏,火焰喷出的电解质呈白色条状,可在固体电解质的断面上清楚地看到灰色或灰白色的夹渣,通过降低槽温,添加氟化铝、氟化镁,可促进炭渣与电解质的分离。
在电解生产正常时,电解质中的炭渣是以燃烧消耗的:
当电解质中炭渣生成量多,炭渣就不能完全燃烧,从而影响电解质的流动性,这时必须捞出炭渣。炭渣的产生也使阳极的消耗增大、阳极的消耗除了氧化产生的炭渣外,还有几种阳极的消耗方式。
(1)炭渣多,职工劳动强度大。
(2)烟气外泄,不利环境净化。
(3)电解槽人为干扰大,不利平稳调控。
(4)角部裸露,易氧化,易冷却,造成伸腿肥大。
(5)捞渣过程对侧部炭砖的影响很大。?
为解决上述问题,从2005年8月10日起,在两个铝厂进行了少捞炭渣的技术攻关。
减少炭渣的技术措施有:
(1)大面保温料收边宽度达到12~15cm。
(2)铝水平提高0.5~1cm。
(3)电解质水平提高0.5~1cm。
(4)捞完炭渣后,及时封严角部,防止空气流入槽大面,从而避免阳极氧化造成阳极炭渣脱落。
(5)确保效应后炭渣捞净,捞取炭渣后,及时封严出铝口和烟道端火眼,防止中缝内阳极氧化造成炭渣脱落。
减少炭渣的管理措施有:
(1)及时封堵好大面冒火。
(2)采取32h作业制度,每班仅捞取本班责任槽的炭渣。
减少炭渣的具体操作措施主要有:
(1)第一铝厂和第二铝厂当前的基本的责任槽划分方法:各工段责任槽按每人看4台槽、四班三倒的方式划分,从1号槽开始每4台槽为一组,4个运行班,每班1台责任槽。在一般槽温正常的情况下,看槽人只打捞自己责任槽的炭渣。
(2)调整槽出铝前平均铝液水平:第一名厂为21.5~22.5cm,第二铝厂为22~23cm。电解质水平调整为21~22cm。
(3)大面保温料收边宽度达到12~15cm,侧部炭块与侧部结壳间不能有缝隙,发现后要及时用氧化铝或阳极上细粉料封平。
(4)电解温度为952~962℃,分子比为2.25~2.35。
(5)接班时,检查电解槽大面冒火情况,要及时封好。
(6)接班后,将自己责任槽的4个角部打开,认真清理干净结壳块,开始打捞炭渣。打捞时尽量不带出电解质或结壳块,捞出的炭渣以冷却后不发白且不结块为准。捞完后洒上氧化铝,结壳后再彻底封好火眼,凡有块状的炭渣必须回槽循环使用。
(7)在不捞炭渣时,4个角部及烟道端火眼均应封好,出铝口火眼应尽量小,直径不能超过10cm。?(8)不论是否是责任槽,效应后30min,要及时在出铝口呼烟道端将该槽炭渣打捞干净。如太多时,应打开角部打捞,捞完后及时封好火眼。
(9)在槽温超过963℃以上时,打开角部捞净炭渣,捞完后及时封好火眼。
技术应用后的效果与分析
采用上述各项措施后,电解槽的炭渣明显减小,氟盐消耗降低,电流效率明显提高,而且保证了电解槽炉膛规整及技术条件正常。第二铝厂从2005年9月29日,第一铝厂从2005年10月8日开始推广此种技术以来。从8月份平均每天捞取20~25t炭渣到目前平均每天2t,每天少捞18~23t炭渣,若每吨炭渣按含30%电解质,电解质按回收价2393元/t计算,少捞的炭渣每年可节约资金500余万元。实行32h作业制后,捞渣次数更少,人为干扰更少,电解质波动小,二次反应小,从而提高电流效率。若电流效率按提高0.2%计,单台槽日增产5kg,铝价按平均价16000元/t,每年可创效益150余万元。
炭阳极掉渣除由电解工艺影响外,从炭素工艺分析主要是一次焦与二次焦性能及其氧化速度的差别而引起的。因此,抓好阳极炭块质量是解决掉炭渣的根本措施。当沥青焙烧形成的二次焦质量差、氧化快时,其差别更明显,就会使一次骨料残焦在运动电解质的冲刷下脱落进入电解质,即成炭渣。
二次焦质量差的原因可有以下两种情况:
(1)煤沥青与石油焦中微量元素的差别。煤沥青的成焦率仅为60%左右,煤焦油中加碳酸钠脱氨的钠会明显富集提高,从而增大氧化性。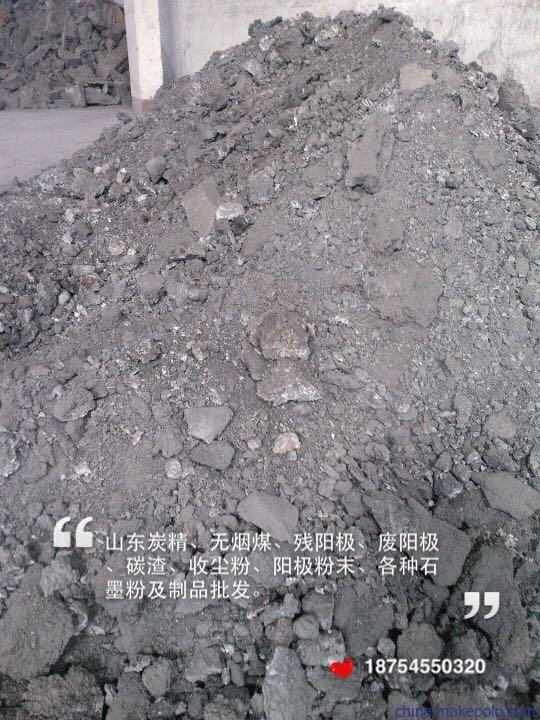
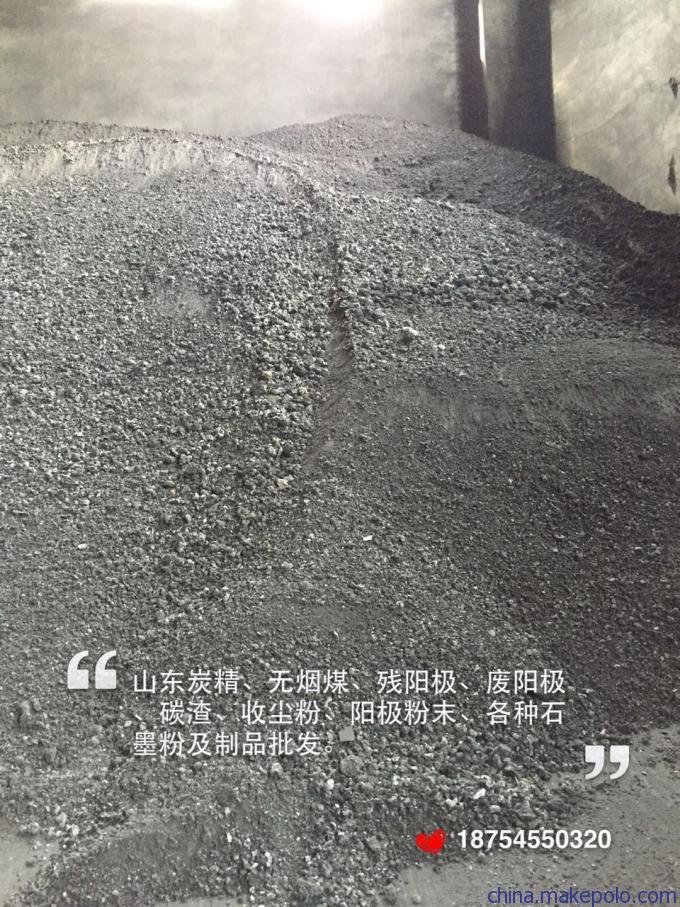

(2)配料不合理、煅烧质量差造成炭块强度低,不耐冲刷而掉渣。这主要是因为阳极黏结剂质量及焙烧质量差而导致阳极抗氧化性差或裸氧化。