内圆磨床是利用车加工的高效率,对产品端面和内孔进行车削,端面直接车到要求尺寸,内孔车削时留0.03-0.05mm余量,然后用砂轮进行磨削。
这样既能提高产品加工的效率,又能满足产品使用时内孔要求磨削纹路,达到油膜润滑的目的。
将原来加工方式(先粗磨内孔,修砂轮,再精磨内孔,再磨端面或者在别的车床上涨内孔车端面,或者采用专用的端面磨床进行端面磨削。)简化为车端面、车内孔、精磨内孔,一次装夹完成一个端面和内孔的加工。
由于精磨余量很小,砂轮不需要每个产品休整,可以间隔10-20件休整一次,具体视产品有所变化。既节约时间又节约人力,同时节省耗材及产地面积。如果不了解可以咨询gesete.net官方看看。
内圆磨床主要技术参数:
项目 | 参数 | 项目 | 参数 |
可磨内孔直径 | Φ15∽100mm | 工件转速 | 200-1000r/min(无级调速) |
最大磨削深度 | 125mm | 砂轮转速 | 可选配 |
最大研磨外径(双磨头设备) | 300mm | 床头箱回转角度 | 20° |
工件最大回转直径 | 450mm | 机床总功率 | 40KW |
工件主轴(X轴)最大行程 | 700mm | 机床外形尺寸 | 2700X2500X2000 |
工件台(Z1轴)最大行程 | 480mm | 机床重量 | ≈8000Kg |
工件台(Z2轴)最大行程 | 480mm | 圆度 | 0.003 |
工件主轴(X轴)进给速度 | 0-5m/min | 圆柱度 | 0.003 |
工作台(Z1轴)进给速度 | 0∽10m/min | 内孔表面粗糙度 | Ra0.32 |
工作台(Z2轴)进给速度 | 0∽10m/min | 内孔对端面垂直度 | ≤0.01 |
工件主轴(X轴)分辨率 | 0.0005mm | 端面跳动 | ≤0.01 |
工作台(Z1轴,Z2轴)分辨率 | 0.001mmm | 使用电源 | 3∽50/HZ,380V |
可磨内孔直径 | 0.001mm |
|
|
此内圆磨床与传统内圆磨床对比优势
项 目 | 传统设备 | 古思特设备 |
车削功能 | 无 | 有 |
一次装夹完成端面内孔加工 | 不能 | 能 |
加工效率 | 低 | 高,内孔加工是传统设备的约2倍 |
耗材消耗量 | 大 | 小 |
劳动强度 | 高 | 低 |
用工量 | 大 | 小 |
同样产能使用面积 | 大 | 小 |
1. 进口高精度套筒主轴
机床采用进口高精度套筒主轴,主轴由3精密角接触球轴承7016CP4及1个精密双列滚柱轴承NN3015K所组成,组装后通过精度检验、温升测试、主轴鼻端采用A2-5规格设计,适合搭配各式手动或者油压夹头。
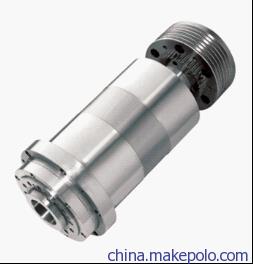
2. 合理的内部布局
机床X轴采用高精度滚珠丝杆副,并配以滚柱重载直线导轨副,具有超重负载,低噪音,高速,高精度等特点。床头箱固定在X轴滑板上,随滑板作进给运动。
机床Z1和Z2采用高精度滚珠丝杆副,导轨采用十字交叉滚柱钢导轨,刚性好,进给灵敏。电主轴或车刀固定在往复滑板上,随滑板作往复运动。
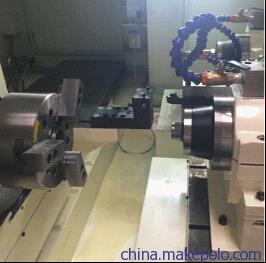
3. 西门子828D控制系统
机床采用西门子828D控制系统,结构紧凑,极其坚固耐用,并且非常容易维护,具有强大的数控功能,能够在很短的加工时间内实现绝佳的工件加工精度。

4. 电柜
电柜在机床左上侧,外观平整,柜门开启自如,柜内密封良好,走线规范,线号清晰,电柜内电气元件采用进口件。
5. 内部多条冲水装置
床身内部有淌水的斜槽,并在每条斜槽上配以冲水装置,有利于磨灰,切屑的清理,使机床床身台面保持干净。
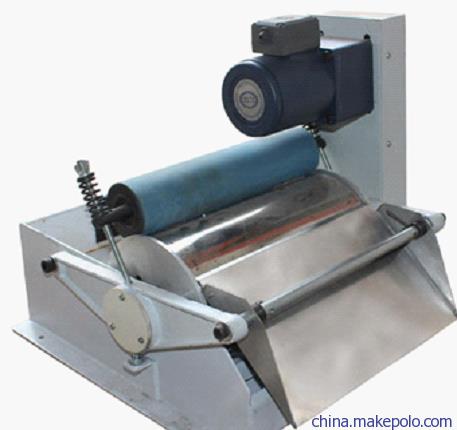
6. 磁性分离器
机床采用磁性分离器对冷却液进行净化,通过磁性分离器的磁性滚筒把冷却液中的铁屑吸出,使冷却液保持干净。使用磁性分离器可以减少砂轮修整次数、提高工件的表面粗糙度、延长砂轮和冷却液的使用寿命。
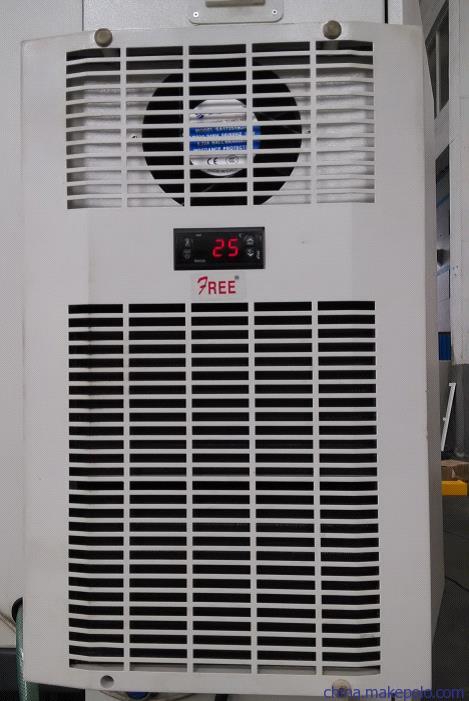
7. 电柜空调
机床采用电气箱空调,可以带走电气元件消耗电能发出的热量,为电箱提供理想的湿、温度环境,同时隔离了外界的灰尘、腐蚀性气体,延长电气元件的使用寿命,提高机床系统运行的可靠性。