二、 液压系统
搅拌筒的液压泵和液压马达的工作压力为40~45Mpa,液压系统的压力,应符合液压件使用说明书中的规定,不得随意调整,液压油的油质和油量应符合原定要求。
在换油时,头一次换油时间在接车工作500小时后进行,第二次以后换油周期应在一年左右;值得注意的:每次换油必须运转后达到工作温度时才可更换,每次换油后必须检查整个系统的密封性能,重新旋紧所有螺栓,排放螺堵和软管连接,这里也应注意在拆下液压系统的任何部件时,均应立即封好接口,以免灰尘进入。
三、 供水系统
冬季运行有结冰危险时,供水系统部件的水必须排尽,只要打 开所有的控制阀使水流尽即可,再次加入水时逐个旋紧。
车辆行驶之前,关闭供水系统的进气控制阀,以免影响车辆的 制动性能。
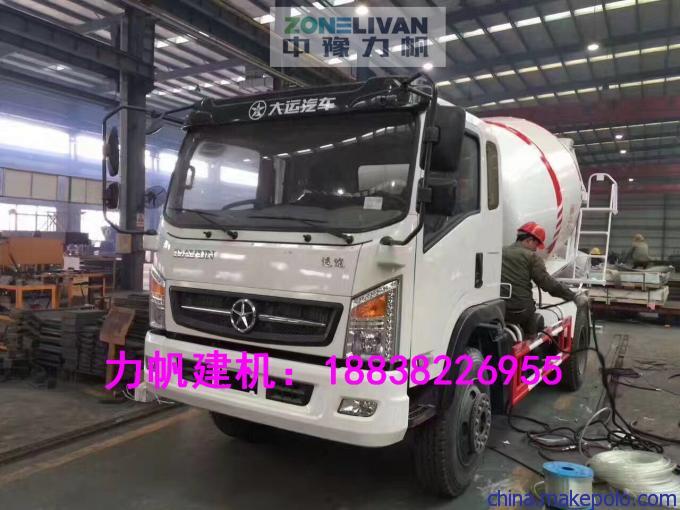
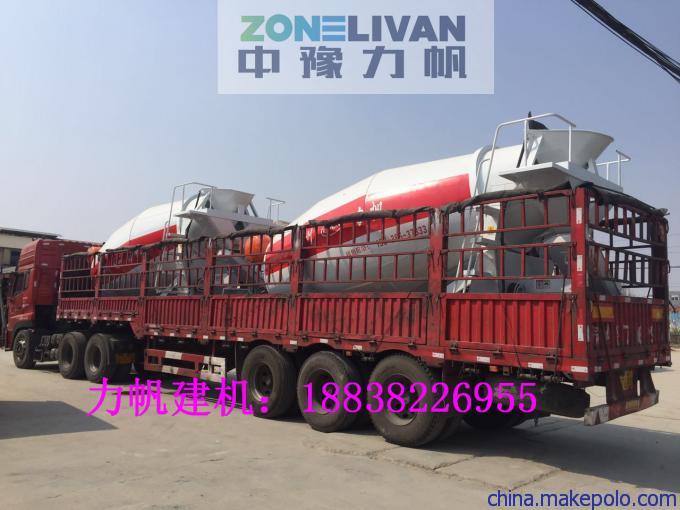
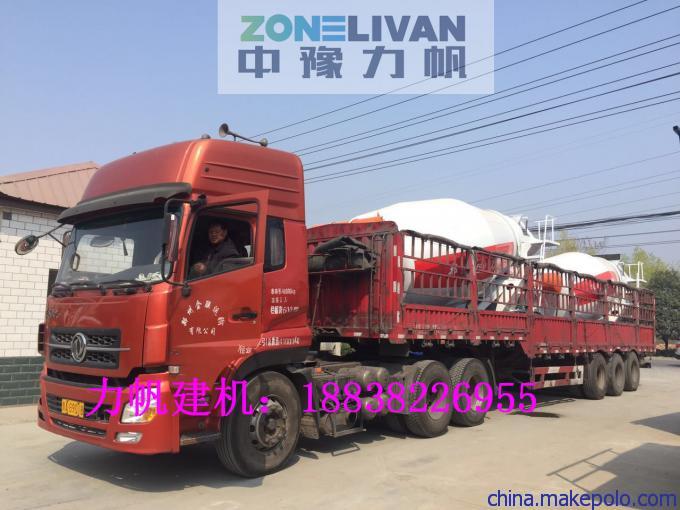
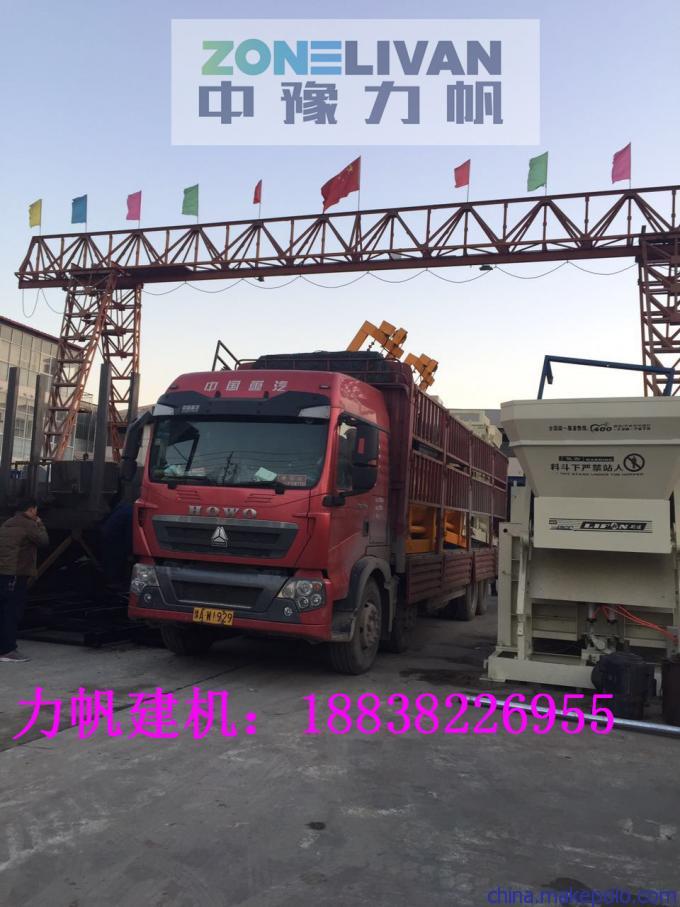
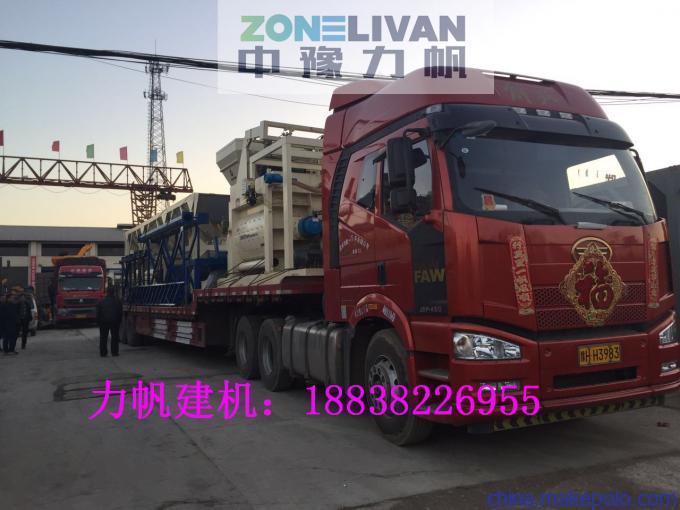
1.起动罐车之前,应把搅拌筒操作手柄放在“停止”位置。
2.起动发动机后,应使搅拌筒在低速下转动10分钟左右,使液压油温升到20℃以上后方可工作。
3.罐车在露天停放时,装料前应将搅拌筒反转,将积水和杂物排出,以保证混凝土的质量。
4.在运输混凝土时,要保证滑斗放置牢固,防止因松动造成摆动,在行进中打伤行人或影响其它车辆正常运行。
5. 装运搅拌好的混凝土时,搅拌筒转速为2-10转/分,在运输过程中,平坦路面上搅拌筒转速保证在2-3转/分,行驶在侧倾坡度大于50的路面,或左右晃动较大的路面时,应停止搅拌旋转,待路况好转后再恢复搅拌旋转。
6. 混凝土罐车运送混凝土的时间不能超过搅拌站规定的时间。运送混凝土途中,搅拌筒不得长时间停转,以防混凝土产生离析现象。司机应时常观察混凝土情况,发现异常及时通报调度室,申请做出处理。
7. 车内装有混凝土时,在现场停滞时间不得超过1小时,如超时应立即要求现场负责人给予及时处理。
8. 罐车运送混凝土塌落度不得低于8cm。从混凝土入罐到排出,气温高时不得超过2小时,阴雨天气温度低时,不得超过2.5小时。
9. 在排出混凝土之前,应使搅拌筒在10-12转/分的转速下转动1分钟,再进行排料。
10. 混凝土罐车出料完毕,应立即用随车的软管放水将进料口、出料斗及出料溜槽等部位冲洗干净,排去粘结在车身各处的污物及残留混凝土,再向搅拌筒内注水150-200L的清水,在返回途中要让搅拌筒慢速转动,以清洗内壁,避免残余料渣附在筒壁和搅拌叶上,并在再一次装料前将这些水放掉。
11. 运送混凝土时,发动机转速在1000-1400转/分范围内工作,以使发动机有较大扭距,在运送混凝土过程中,车速不得超过40km/h,以保行车安全。
12. 在水泵工作时,禁止空转,连续使用时不要超过15分钟。
13. 水箱的水量要经常保持装满,以备急用,冬季停机后,应将水箱、水泵、水管、搅拌筒内的水放净,并停放在朝阳、不积水的地方,以免冻坏机械。
14. 冬季应及时安装保温套,并使用防冻液对罐车加以保护,根据天气变化更换燃油标号,确保机械的正常使用。
15. 在检查、修理液压传动部分时,应使发动机和液压泵在没有压力的情况下进行。
16. 工作完毕,应把搅拌筒内部和车身清洗干净,不能使剩余的混凝土留在筒内。
混凝土搅拌车主要由底盘与上装两部分组成,简单地可以分为:底盘系统、液压传动系统、搅拌罐体、出料系统、清洗系统、副车架、操纵系统、托轮系统、进料系统、电路系统十个部分组成。
1)底盘系统:搅拌车的主要组成部分,整个混凝土搅拌车的运输功能就是由底盘来实现的。底盘一般采用定型生产的二类专用底盘加装上装后改制而成。
2)液压传动系统:将经取力器取出的发动机动力,转化为液压能(排量和压力),再经马达输出为机械能(转速和扭矩),为搅拌筒转动提供动力。
3)搅拌罐体:搅拌筒是整个搅拌运输车的关键部件,是存储混凝土的容器,对防止混凝土固化、离析起着决定性的作用。罐体内部有叶片,主要起搅拌与导料的作用。
4)出料系统:主要由主卸料槽、副卸料槽、锁紧杆等组成,副卸料槽起延长主卸料槽的长度的作用。
5)清洗系统:清洗系统主要由压力水箱、水枪、水管、阀等组成。采用气压供水,主要作用是在装完料后冲洗料斗及出料完毕后冲洗拌筒、卸料槽,防止混凝土粘结。
6)副车架:搅拌车副车架是主要的承重部分,作业时的载荷几乎都是通过它来支撑再传递给底盘。副车架还起缓解路面颠簸、衰减冲击载荷的作用。整个副车架由主梁、前台支撑架、后台支撑架组成。
7)操纵系统:操作系统由控制器、联动轴、软轴及连杆机构组成,主要控制搅拌筒的转速及旋转方向。
8)托轮系统:搅拌罐后部与副车架连接的部位,主要起支撑滚筒体的作用。
9)进料系统:主要由进料斗与支架组成,进料斗由于受冲击磨损较大,材料要求耐磨性好,支架主要起减轻冲击力的作用。
10)电路系统:主要指搅拌车的整个的电路,包括整车的尾灯,侧标志灯、示廊灯、冷却风扇电机等。


