The DS-25 is a member of the DS series of Electric
Encoders?, based on Netzer Precision proprietary
technology. The Electric Encoder? offers many
advantages - some unparalleled
Low profile (7 mm).
Hollow, floating shaft.
No bearings or other contacting elements.
High resolution and precision.
High tolerance to temperature extremes , shock,
moisture, EMI, RFI and Magnetic fields.
Very low weight.
Holistic signal generation
Analog or Digital interfaces.
The Electric Encoder? is unique in being holistic, i.e., its
output reading is the averaged outcome of the whole area
of the rotor , This feature makes the Electric Encoder?
forgiving to mounting tolerances, mechanical wander etc.
The absence of components such as ball bearings , flexible
couplers, glass disc, light sources and detectors, along
with very low power consumption makes the Electric
Encoder? virtually failure free.
Coarse and Fine channels
The DS-25 has two operational modes: a Coarse-mode
and a Fine-mode - equivalent to two separate encoders
in a common housing. The modes are selectable by a logic
C/F command; logic “0” (0V to +0.5V) selects the Coarsemode,
which has 3 Electrical Cycle/Revolution (EC/R)
while logic ”1” (+3V to +5V) selects the Fine-mode which
has 16 EC/R.
The switching time is less than 1 ms.
The Coarse-mode outputs need to be read only upon
system initiation after which the encoder is permanently
switched to the Fine mode. Coarse and Fine sine / cosine
pairs are used to calculate the initial absolute position,
from that point tracking the Fine-channel outputs provides
the absolute mechanical rotation angle with the specified
accuracy and resolution.
All output signals are referenced to an internally generated
voltage Vr (~2.25V)
Absolute Position calculation:
The analog Sine / Cosine outputs convey the Electrical
angle of the Coarse or Fine signals. The Absolute
mechanical angle is computed by digitizing the analog
signals and applying factory-supplied algorithms. Please
refer to AN-02 and AN-03
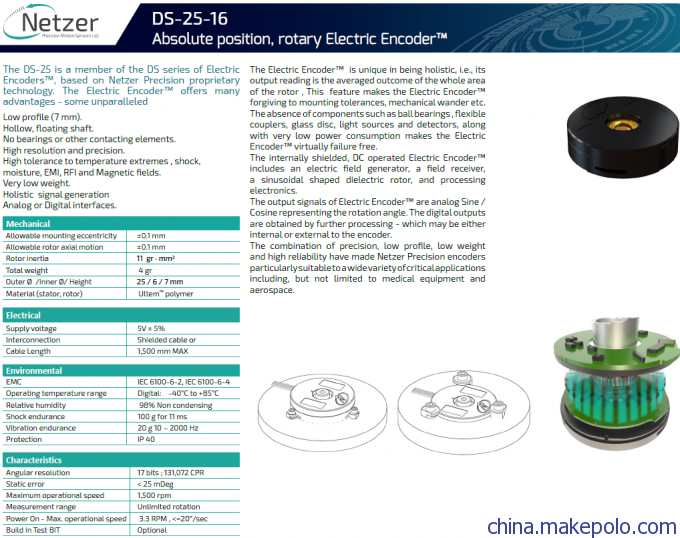



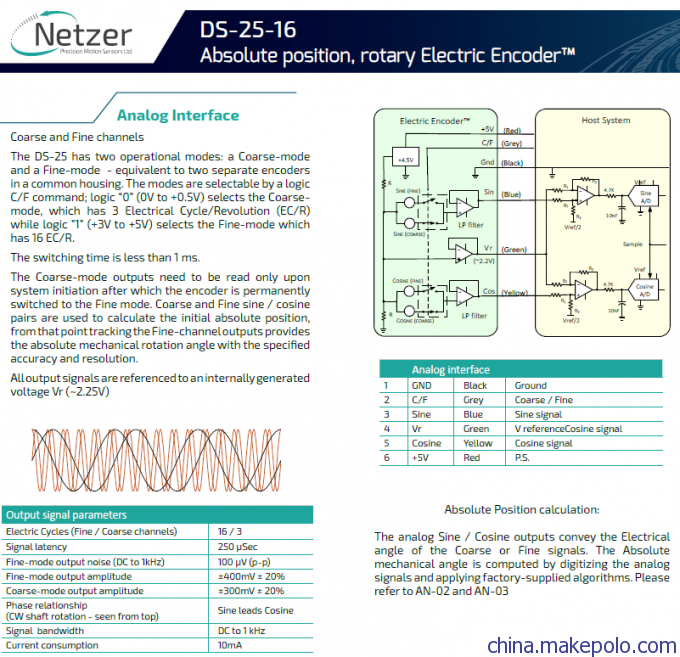
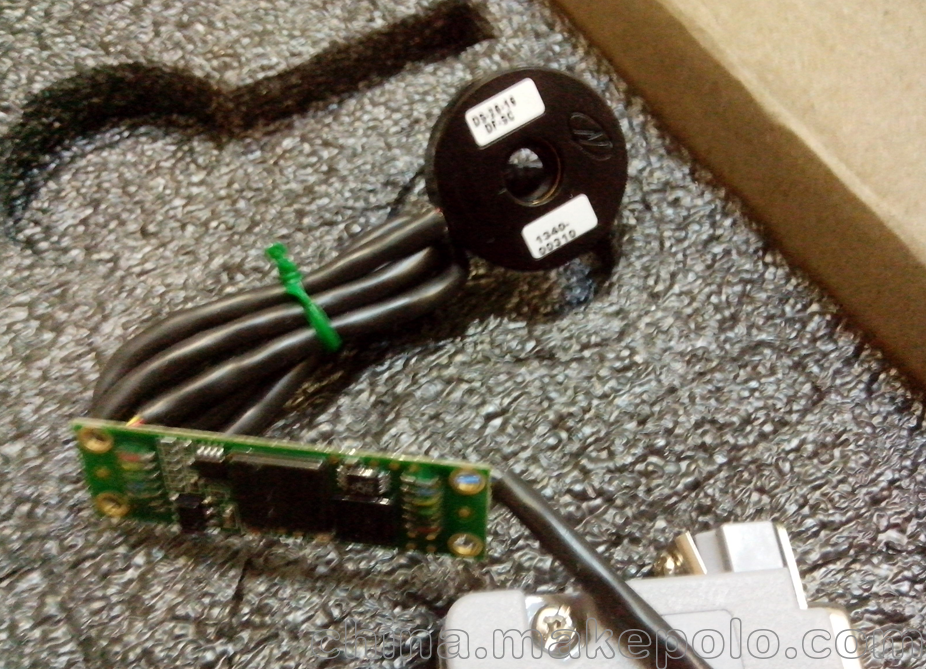
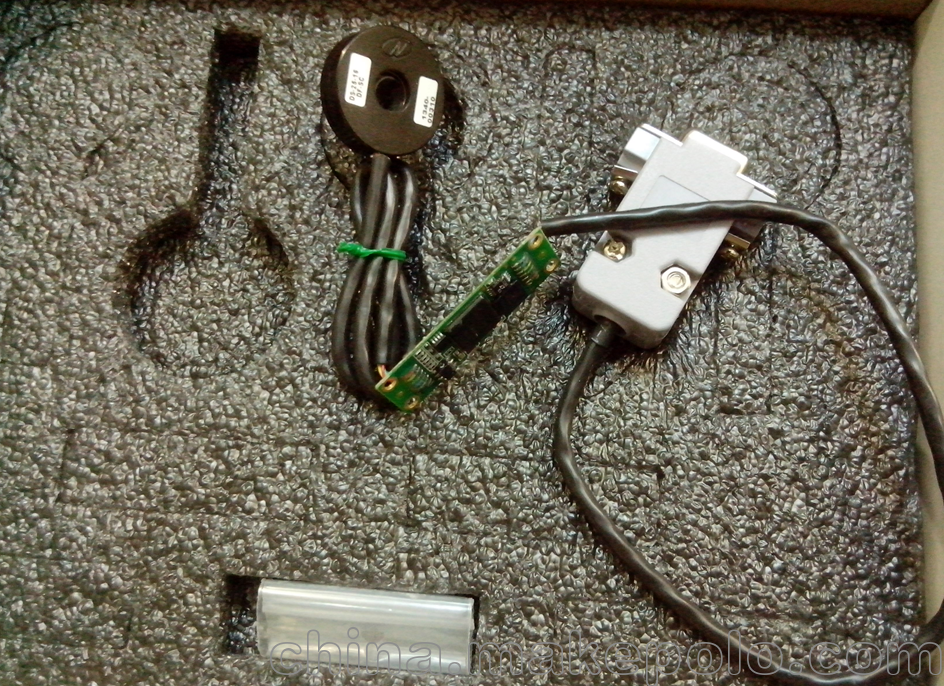