

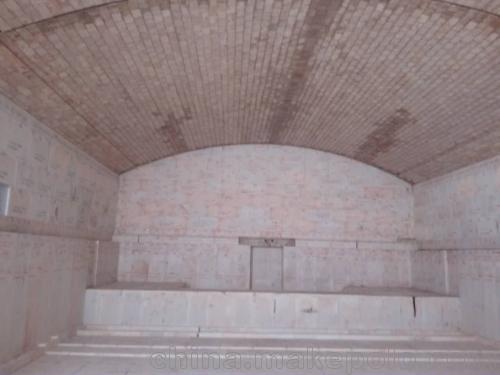
我国玻璃工业产能已连续多年高居世界首位。我国玻璃工业熔窑节能潜力是很大的。大力提倡玻璃熔窑节能,是我国玻璃窑炉科学工作者和企业的共同责任,玻璃窑炉节能新技术的开发和推广,将引领玻璃工业完成“工业企业普遍节能20%”的节能减排目标,具有良好的社会效益和经济效益。
目前,工业发达国家玻璃熔窑的热效率一般在30%~40%,我国玻璃熔窑的热效率平均只有25%~35%。燃料在玻璃制造成本中,已超过1/3的比重,能源价格的不断攀升,已经在严重影响着行业的经济效益。因此,利用发生炉煤气代替目前的主要燃料重油有很大的市场应用前景。
发生炉煤气及其应用发生炉煤气的产生方法是将煤在发生炉中燃烧后,将炉底的空气加以限制,使煤不能完全燃烧,因而产生大量的一氧化碳,这就是发生炉煤气。这种燃烧法使炉中排出的气体主要是CO、CO2和N2.在一般的煤气发生炉中,煤是由上而下、气化剂则是由下而上地进行逆流运动,它们之间发生化学反应和热量交换。这样在煤气发生炉中形成了几个区域,一般我们称为“层”。按照煤气发生炉内气化过程进行的程序,可以将发生炉内部分为6层,即灰渣层、氧化层(又称火层)、还原层、干馏层、干燥层、空层。
根据煤在气化过程中气化剂不同,可以得到成分和性质不同的发生炉煤气。煤气化常用的气化剂或空气或水蒸气或者两者合用,得到的发生炉煤气相应称为空气煤气、水煤气、混合煤气。
在蓄热室马蹄焰中的应用马蹄焰窑的优点一是热利用率高。马蹄形火焰在窑内呈“U”形,长度可达熔化池长度的1.3~1.5倍,行程较长,因而燃料燃烧充分,同时窑体表面积小,热散失量较少,这可提高热利用率,降低燃料消耗。目前先进的大型马蹄焰窑比相同熔化面积的横焰窑热耗量低15%~20%。二是结构简单,造价低,建一座马蹄焰窑的费用比建同等规模的横焰窑低25%~30%。马蹄焰窑的缺点是:(1)沿窑长方向难以建立必要的热工制度,火焰覆盖面积小,在炉宽度上温度分布不均匀。(2)一对小炉限制了炉宽,也就限制了炉的规模。(3)燃料燃烧喷出的火焰有时对配合料料堆有推料作用,不利于配合料的熔化澄清。
由于以上特点,马蹄焰窑已被广泛用于制造对玻璃质量无特别要求的各种空心制品如瓶罐、器皿、化学仪器、玻管等。
在横火焰平板玻璃池窑中的应用在浮法玻璃的生产过程中,熔化是至关重要的工序之一,而要想有好的熔化效果,其前提条件是要有高热值的燃料。经过几年来的发展,平板玻璃生产使用的燃料已由单一的发生炉煤气,发展到现在根据能源条件因地制宜地进行选择。除发生炉煤气之外,有重油、天然气、焦炉煤气、燃料油和全电力等多种途径。目前,玻璃企业已全面掌握了各种燃料的使用技术。
在各种燃料中,气体燃料的燃烧过程较容易控制,也较容易实现自动调节。另外,气体燃料可进行高温预热,因而可以用低热值燃料来获得较高的燃烧温度,以利于节约燃料、降低能耗。任何一种气体燃料都是由一些单一的气体混合而成的。其中可燃性的气体成分有CO、H2、CH4和其他气态碳氢化合物以及H2S;不可燃的气体成分有CO2、N2和O2,此外,在气体燃烧中还含有水蒸气、焦油蒸气及粉尘等固体颗粒。
目前的能量来源主要是重油和天然气,而在我国能源的构成中,煤的蕴藏量较丰富,所以如何利用煤气或将煤转化为高热值燃料如焦炉煤气等,具有十分重要的意义。以煤气为燃料的玻璃熔窑历史悠久,在我国早期的平板玻璃熔窑中,大部分是以煤或发生炉煤气为燃料。发生炉煤气就是将固体燃料在煤气发生炉中进行气化而得到的人造气体燃料,其热值较低。随着煤气发生炉的不断改进,燃煤气熔窑的低成本优势日益体现出来。目前,平板玻璃市场竞争日趋激烈,市场比较低迷,而重油价格见涨,各生产厂家在提高玻璃质量的同时,也都在想方设法降低玻璃的生产成本。
熔窑设计结构随着计算机技术的飞速发展,通过数字和物理仿真,模拟玻璃熔窑实际工作状态,通过分析熔窑结构对工作状态的影响,可以设计出更加合理的熔窑结构,从而实现熔窑的节能。
在结构上可以考虑以下几个方面:
(1)增大蓄熔比,一般超过50比1,具体做法一是加高蓄热室,或采用三三通道蓄热室。二是采用高蓄热效率的八角筒型或十字型格子砖,增加有效蓄热面积。尽量提高空气预热温度至l300℃以上,这样可以提高燃料的燃烧速度,节约燃料以达到节能效果。
(2)燃烧器在窑炉前端横向排列,小炉设汁合理,喷火口采用扁平式,燃烧完全,火焰覆盖面积大。
(3)加料口采用预熔池结构,同时采用密封式投料技术。
(4)采用深澄清池倾斜流液洞结构和小工作部结构,减少玻璃液回流和工作部散热。
(5)窑炉进行全保温,蓄热室墙、小炉、大碹、池壁、池底、胸墙采用全保温,蓄热室墙、小炉、胸墙、大碹应增加保温涂料,以减少窑体散热。
(6)在熔化部池底设置窑坎,通过窑坎稳定窑池中投料回流和成型回流,避免因熔化温度的波动而造成玻璃液的质量不均。同时提高玻璃的澄清效果和均化质量,减少熔化池底层往回流动的玻璃液量,降低能耗。
(7)在熔窑热点部位设置鼓泡装置,加速玻璃液的澄清和均化。
(8)流液洞与分隔墙将窑炉分隔成熔化池与工作池两部分,这种形式允许在工作池用一定的加热方式单独调解温度,稳定玻璃液的成形温度。
提高材料质量,延长熔窑使用寿命选用优质、匹配良好的熔窑各部位耐火材料,是熔窑节能工作的基础和保证。
(1)空气蓄热室上部格子砖采用电熔再结合镁砖较适应,小炉、胸墙、大碹须用96-A优质硅砖,大碹硅质火泥要选择得当,应具有一定的黏结性和抗火焰侵蚀能力。
(2)池壁采用无缩孔或倾斜浇铸AZS电熔砖,投料口拐角、流液洞、电极砖等关键部位采用无缩孔AZS电熔砖。熔化部、冷却部均须用电熔砖铺底。
(3)硅砖和电熔砖之间要有烧结锆刚玉砖过渡,以避免发生接触反应,另外黏土火泥和硅质火泥不能混用。
目前,我国耐火材料行业已取得了长足进展,设计使用合理,采用国产耐火材料完全可以达到5年以上的熔窑使用寿命。
熔窑余热利用在玻璃熔窑的各项热损失中,由蓄热室排出烟气的余热量占有很大比例。如何提高熔窑排烟余热的回收利用,一直是国内外热门的研究课题。现阶段,人们对排烟余热回收的途径主要有余热发电、余热制冷、余热锅炉和余热预热玻璃配合料等几种途经。
采用电辅助加热技术可以解决颜色料或部分难熔料的熔化问题,同时在需要时达到提高玻璃质量和产量的目的,而且可以延长熔窑使用寿命,节约能源。
采用富氧燃烧或纯氧助燃节能新技术富氧燃烧的基本原理是:在燃烧时将助燃空气中含氧量增加,一般在23%~32%的O浓度下进行燃烧,这样可使燃烧速度加快和燃烧完全。富氧燃烧减少了N2及其他不参加燃烧反应的气体比例,减少了由废气带走的热量。同时,由于助燃气体中N2含量降低,水蒸汽和CO2的含量和分压增大,火焰黑度增加,富氧燃烧使燃料在火焰区域的燃烧完全度提高,火焰温度提高,增加了火焰向配合料或玻璃液的传热能力。面靠近大碚火焰上部非富氧区温度降低,大碹向外散失热量减少,在减少热损失的同时提高了熔窑熔化率,从而实现富氧燃烧熔窑的节能。另外,燃烧产物中的NOx含量降低,减少了废气污染,改善了环境。一般来说玻璃熔窑采用局部增氧-梯度燃烧富氧燃烧节能专利技术,预计可以取得6%以上的节能效果。

