国内目前常用的干混砂浆运输车主要有两种结构,一种是与粉粒物料运输车结构相同的普通气卸式,该结构是在粉粒物料车的基础上加大流化床和侧滑板的角度改进而来的,该结构极易产生离析现象,同时还有残留率高、卸料时间长、消耗气量大等缺点。另一种是液压举升气悬浮椎体料仓卸料系统,该结构卸料是利用液压油缸将罐体举起,是物料集中在罐体椎体部位。此时气悬浮卸料装置将砂浆流化在椎体底部局部范围内,压缩气体对物料逐层剥落、流化同时形成二次混合,最后砂浆经管道快速卸出,避免了砂浆因长时间的搅拌产生的离析。此结构耗气量小、残留率接近为零,同时由于加装了卸料清理装置,实现了快速清理余料,有效的解决了运输余料不能清除而造成的混料问题,保证了干混砂浆的质量。
结构介绍
罐体总成
干混砂浆运输车罐体总成有筒体、椭圆封头、球形封头、圆台体、气室封头等部件组成。卧式内部是由侧滑板帆布流化床组成,分为两仓三盖结构。举升式只在气室封头处设计有圆形流态化装置,但该装置面积较小,主要用于产生一定混合比的固体二相流。罐体内的干混砂浆首先被罐体举升至设计角度,再利用重力流至后端椎体部分,此时向气室封头处充气,则流化态装置产生一定混合比的固气二相流,当罐内压力到达0.2Mpa后,打开卸料阀即可卸料。
副车架总成
副车架主要起缓冲作用,可以改善底盘的承载情况,避免底盘车架集中受力。
区别
卸料原理是卸料时利用液压举升缸将罐体举起,物料呈山体滑坡态势,气浮式缷料原理只是在锥体局部范围内,通过吹入压缩空气在缷料口座均匀分布的气流形成气垫,使浮化后的物料经管道均匀、平稳、快速缷料,避免产生物料本身之间的颗粒相互摩擦,避免大面积、长时间的搅动产生离析,空压机产生的压缩气体通过管道进入罐体尾部“奶嘴”式小气室,形成“气刀”,将尾部物料逐层排出,不影响物料结构,并形成二次混料。耗气量小,剩灰率低。 由于以上特点有效的解决了干混砂浆卸料过程中的离析问题。对于普通砂浆和特种砂浆以及生产原料中干沙散装运输都可以轻松完成。目前,国内对于干混砂浆的运输大致采用两种方式:一种是在普通散装水泥运输车上加大出料口后改制而成,这是干混砂浆发展初期的一种替代进口的产品;另一种我司在学习欧洲现有的干混砂浆运输车技术上消化吸收研制而成的产品,它是干混砂浆物流发展的必然趋势,下面我们就这两种不同结构产品做一下简单的对比:
离析问题
1、从两者的卸料原理看: 首先要说明的是传统的运输车是为解决粉粒状物质的散装运输而研制的。它的结构特点:卧式流化床式气体缷料 它的工作原理:通过取力器和传动轴将汽车底盘的动力传递给空压机,空压机产生的压缩空气经管道进入罐体底部气化室内,经气化床与水泥混合成流态后沿卸灰管输出。在这一过程中,气体透过帆布震动,由于干混砂浆由许多种大小、密度不同颗粒组成,容易形成分层,特别是卸料至1/3后,由于压缩空气在整个罐体的底部,对流化床,大面积、长时间的搅动干混砂浆,造成物料本身之间,大面积、长时间的颗粒相互摩擦。极易产生离析,降低干混砂浆的质量,而且耗气量大、剩灰率高。这样对于普通砂浆的散装运输存在一定的离析状况,对于特种砂浆的运输存在严重问题。
清理余料
根据国外对干混砂浆的运输要求:在每次运输卸料后,必须快速排尽剩余料,以避免运输不同品种的干混砂浆造成混料。 干混砂浆运输车配置了专用卸料装置,实现了快速清理余料,有效的解决了每车运输余料不能清除而造成的混料问题,保证了干混砂浆的质量。
运输介质
散装水泥车适用于粉煤灰、水泥、石灰粉、矿石粉等颗粒直径不大于0.1mm粉粒干燥物料的运输和气压卸料;而干混砂浆运输车的用途更加广泛,在运输空闲时间可以运输其他颗粒状和粉状生产原料。同时也可以用于高温(120°C-150°C)颗粒、粉粒物料的运输。
优势
1、干混砂浆运输车采用全封闭运输,整个物流过程清洁、环保、节能、高效。
2、卸料速度快,每分钟1.6吨,缩短了卸料时间,提高了运输效率;剩余率极低为万分之二,接近为零,节省材料。
3、为了满足国内对干混砂浆技术质量管理规范的要求,干混砂浆运输车配置了专用的取样装置,为确保实时监控和检测干混砂浆的质量提供了保障。
4、干混砂浆车底盘可选装空气悬架系统,对路况不好、长距离运输中容易产生的离析问题,也能有效的控制。 综合以上表述,干混砂浆散装运输车相比普通散装水泥运输车优势明显,是中国砂浆生产厂家的最佳选择。

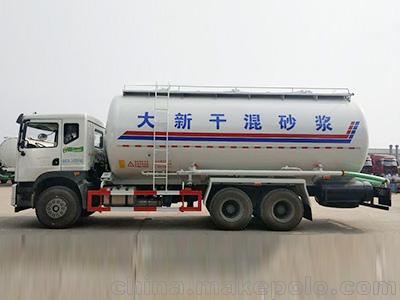
