
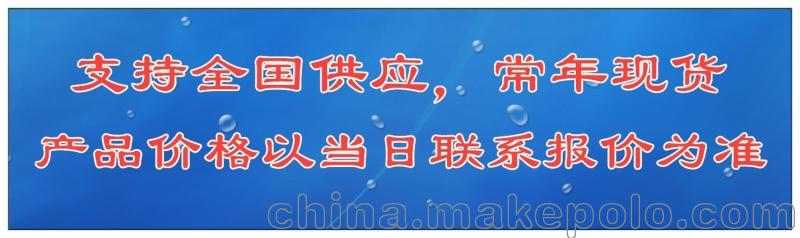

石墨增碳剂
1、增碳效果明显,吸收率高达90%以上,吸收速度快;
2、具有促进铸铁孕育形核的效果;
3、改善石墨形态,增加石墨数量,细化石墨,提高产品机械性能,改善加工性能。
使用方法:
1、炉内加入
配料时根据所熔炼钢(铁)水的含碳量要求调整增碳剂加入量,随金属炉料加入电炉中部偏下部位,碳的吸收率可达90—99%。
2、后期增碳
钢(铁)水熔化后,微量调整碳份,可以加在钢(铁)水表面,通过电炉熔炼时钢(铁)水的涡流搅拌使增碳剂溶解吸收,碳的吸收率在80—95%。
增碳剂根据不同标准分为不同种类
增碳剂的种类有很多,可以应用于不同的冶炼生产中。但正是由于增碳剂有很多种,不同的增碳剂,具备不同的特点,所以,广大用户对于增碳剂的了解并不全面。为了解答大家的疑惑,也为了能够加深对增碳剂的了解,将增碳剂按照不同的标准,分为不同的种类。
增碳剂可以根据铸造用途分为,球铁增碳剂,灰铁增碳剂,铸钢增碳剂,特种增碳剂。球铁增碳剂一般选用石墨化的高碳低硫产品,其主要材质是石墨化石油焦,石墨化电极等等。球铁增碳剂具有吸收率高,吸收时间快的特点。铸钢增碳剂的种类比较多杂,一般材料为煅煤,或者石墨球,也有用天然石墨碎的。特种增碳剂主要用于刹车片制造,包芯线制造,多采用0-0.5或者0.5-1MM粒度段的石油焦居多。
如果将增碳剂按照材质划分的话,可分为冶金焦增碳剂,煅煤增碳剂,石油焦增碳剂,石墨化增碳剂,天然石墨增碳剂,复合材料增碳剂。冶金焦增碳剂是冲天炉用的大焦,其作用除了熔炼之外,就是为金属炉料增碳。煅煤增碳剂主要用于炼钢企业使用,部分铸造企业用于灰铸铁。当然,缺点也是有的,如碳含量低,融化慢,浪费电能,残余量大。石油焦增碳剂主要生产弹丸焦,用于铸造不太好,但可用于铸造灰铸铁。
简单讲解增碳剂的应用
虽然,增碳剂的作用很好理解,就是增加碳含量,但是增碳剂的种类有很多,用户可以根据生产需求,选择不同种类的增碳剂。另外,通过总结增碳剂的应用范围可以清晰的了解到,增碳剂可分为炼钢增碳剂,铸造增碳剂。增碳剂属于外加炼钢、炼铁增碳原料。优质增碳剂是生产优质钢材必不可少的辅助添加剂。
增碳剂的原料有很多种,生产工艺也各异。市场上较常见的增碳剂,主要采用石墨粉剂经压制成型,这种生产方式需要添加过多的粘结剂成型,含碳量一般达不到优质增碳剂的要求。压制后的石墨粉,因为是固体块状,没有多孔隙结构,所以吸收速度和吸收率不如煅烧、焙烧成型的增碳剂。优质增碳剂一般指经过石墨化的增碳剂,在高温条件下,碳原子的排列呈石墨的微观形态,所以称之为石墨化。石墨化可以降低增碳剂中杂志的含量,提高增碳剂的碳含量,降低硫含量。
增碳剂在铸造时使用,可大幅度增加废钢用量,减少生铁用量或不用生铁。绝大多数增碳剂都适用于电炉熔炼,也有少部分吸收速度特别快的增碳剂用于冲天炉。电炉熔炼的投料方式,应将增碳剂随废钢等炉料一起往里投放,小剂量的添加可以选择加在铁水表面。但是要避免大批量往铁水里投料,以防止氧化过多而出现增碳效果不明显和铸件碳含量不够的情况。
分析高温石墨化增碳剂与增碳剂的区别
增碳剂作为铁水当中主要的石墨形核核心来源之一,其作用常常被忽略。通过合理的应用增碳剂,能得到更好的基体组织、机械性能。然而,并不是所有的增碳剂都可以达到这样的效果,前提条件是质量合格,适合的增碳剂。
想要生产出合格的增碳剂,必须要对生产原料进行严格把控,再经高温石墨化处理,过程中不单把硫、气体(氮、氢、氧〉、灰分、挥发分、水分等杂质降低,将其纯度提高。有效地避免产生氮气孔,同时使碳原子从原来的无序杂乱排列变成有序层状排列,大部分的碳原子才能成为石墨化的驱动力,这样的一个过程就是为石墨化处理。
未经过高温石墨化处理的增碳剂,表面会覆盖一层很薄的粘性灰层,使其在铁水当中直溶现象基本不存在,只能随着时间的推移,碳在铁液中逐渐扩散溶解。增加了增碳剂的溶解时间,降低了增碳剂的吸收。只有经过石墨化处理的增碳剂,碳原子才可以在铁液当中迅速熔解,并在铁水凝固时较强的行核驱动力作用下吸附在孕育产生的形核核心上成长为石墨。如果选用的增碳剂没经过高温石墨化处理,碳原子的石墨化驱动能力就大大降低,石墨化能力减弱。
增碳剂
通过对比,可以更直观的了解到经过高温石墨化的增碳剂与普通增碳剂还是有很大的区别的,除此之外,增碳剂的种类也有很多。因此,用户在挑选及使用增碳剂时一定要格外的注意,只有用到适合的,适量的,品质合格的增碳剂,才能达到很好的效果。
增炭剂又称低硫微氮增碳剂,是炼钢和铸造行业使用用以增碳、脱硫等的辅助材料。在其它行业也有使用,譬如刹车片中用做摩擦材料,生产电极糊时用做添加原料。目前所指增炭剂主要是石油焦石墨化之后的石墨化石油焦。
通过特殊的装炉工艺将石油焦装入石墨化炉,依照一定的送电曲线给石墨化炉送电,在高温环境下,石油焦发生一系列的理化反应,并排出其中的硫分、水分、挥发份、灰分等杂质,然后将其冷却,根据粒度需求进行破碎、筛分,包装入库。
石墨化增炭剂:是石油焦在石墨化炉中经过高温石墨化发生理化反应并除硫除灰分等杂质之后的产品。该种产品品质优良,目前国内冶炼行业大批使用,并出口到欧美等发达国家和地区。
钢铁冶炼行业最初的增碳材料是用石墨电极、石墨块及其它炭素制品的下角料,杂质较多,来源贫泛,价格昂贵,冶炼的钢铁品质不好。后来改为煅后石油焦做增炭剂,产量可以保证,成本也较低,国内一些冶炼厂家普遍采用,但用该种增炭剂生产的产品仍然是比较普通的民用钢材。
随着科技的发展,高档轿车、舰艇、航空航天等高、精、尖领域对钢铁的质量要求也越来越高。上世纪九十年代初河南新郑一家炭素企业研制出了一种新型的增炭剂生产方法,就是将石油焦装入石墨化炉,在高温环境下,碳原子的排列呈石墨的微观形态,同时也可降低增炭剂中杂质的含量,提高增炭剂的碳含量,降低硫、挥发份、灰分等含量。经过国内外多家钢铁企业实际应用,用该种增碳剂做添加剂生产出的钢材,能够大大提高钢材质量和性能,可以满足特种行业对优质钢、特种钢的需求。这也就是国内外市场比较认可的优质增炭剂。
一、石墨粒增碳剂
增碳剂分炼钢用增碳剂,铸钢用增碳剂和铸铁用增碳剂,以及其他一些添加材料也有用到增碳剂,譬如刹车片用添加剂,作摩擦材料。增碳剂属于外加炼钢、炼铁增碳原料。优质增碳剂是生产优质钢材必不可少的辅助添加剂。
增碳剂的原料有很多种,生产工艺也各异,有木质碳类,煤质碳类,焦炭类,石墨类等,其中各种分类下又有很多小种类。优质增碳剂一般指经过石墨化的增碳剂,在高温条件下,碳原子的排列呈石墨的微观形态,所以称之为石墨化。石墨化可以降低增碳剂中杂质的含量,提高增碳剂的碳含量,降低硫含量。
增碳剂在铸造时使用,可大幅度增加废钢用量,减少生铁用量或不用生铁。电炉熔炼的投料方式,应将增碳剂随废钢等炉料一起往里投放,小剂量的添加可以选择加在铁水表面。但是要避免大批量往铁水里投料,以防止氧化过多而出现增碳效果不明显和铸件碳含量不够的情况。增碳剂的加入量,根据其他原材料的配比和含碳量来定。不同种类的铸铁,根据需要选择不同型号的增碳剂。增碳剂特点本身选择纯净的含碳石墨化物质,降低生铁里过多的杂质,增碳剂选择合适可降低铸件生产成本。
适用:【铸造厂】球墨铸造、灰铁铸造
固定炭:80以上%,灰份:10%-20%,挥发份:4.2%,水份:1.0-1.8%,硫含量:0.09-0.5%,磷含量:0.01一0.05%,氢.氮含量200ppm一500ppm,
吸收率在90%左右。
石墨粒增炭剂固定炭虽然低,吸收率却高,
而煅煤增炭剂固定炭虽然高,吸收率却低,且硫、磷、氮都高!
另:92煤质吸收率在70%左右,
所以石墨粒是铸造理想的增碳剂
三、95石墨增碳剂
【废钢+增碳剂需要补“短”】
用电炉熔炼废钢(铁屑)+增碳剂生产球墨铸铁,欲想稳定产品质量,需要补的“短”,主要是解决金属液在凝固结晶时,自发晶核少、铁液过冷度大、石墨化能力差、铸件硬度高而不便于机械加工的问题。具体的“补短”操作方法是:
1.在冶炼后期要注意“自发晶核”的培养。加入适量的废钢使铁液激冷,同时适量的加入硅铁以及细颗粒的增碳剂,上面覆盖保温剂,降低功率或停电保温一段时间,以促使析出微细的晶态石墨。
2.在出炉或浇注过程中,进行充分的多次孕育处理,以补充“外来晶核”,可以添加小颗粒的增碳剂、碎硅铁粉粒以及复合孕育剂,虽然加入量很少,但是促进生核的效果很好。
3.如果含硫量过低(特别是生产HT时)可适量加入些硫铁,但必须控制在要求的范围内。总之优化操作程序指的就是:炉料入炉的先后顺序、熔炼中的温度和出炉温度的控制、化学成分的选控、以及强化孕育和复合孕育。
四、95石墨化增碳剂 200目
优质增碳剂一般指经过石墨化的增碳剂,在高温条件下,碳原子的排列呈石墨的微观形态,所以称之为石墨化。石墨化可以降低增碳剂中杂质的含量,提高增碳剂的碳含量,降低硫含量。
增碳剂在铸造时使用,可大幅度增加废钢用量,减少生铁用量或不用生铁。目前绝大多数增碳剂都适用于电炉熔炼,也有少部分吸收速度特别快的增碳剂用于冲天炉。电炉熔炼的投料方式,应将增碳剂随废钢等炉料一起往里投放,小剂量的添加可以选择加在铁水表面。但是要避免大批量往铁水里投料,以防止氧化过多而出现增碳效果不明显和铸件碳含量不够的情况。增碳剂的加入量,根据其他原材料的配比和含碳量来定。不同种类的铸铁,根据需要选择不同型号的增碳剂。增碳剂特点本身选择纯净的含碳石墨化物质,降低生铁里过多的杂质,增碳剂选择合适可降低铸件生产成本。
五、石墨粒增碳剂
【石墨粒增碳剂】——性价比高的增碳剂
适用:【铸造厂】球墨铸造、灰铁铸造
固定炭:80以上%,灰份:10%-20%,挥发份:4.2%,水份:1.0-1.8%,硫含量:0.09-0.5%,磷含量:0.01一0.05%,氢.氮含量200ppm一500ppm,
吸收率在90%左右。
石墨粒增炭剂固定炭虽然低,吸收率却高,
而煅煤增炭剂固定炭虽然高,吸收率却低,且硫、磷、氮都高!
另:92煤质吸收率在70%左右,
所以石墨粒是铸造理想的增碳剂
七、低硫低氮石墨增碳剂
低硫低氮石墨增碳剂产品介绍
含量:
固定碳 硫份 含氮量
大于92% 小于0.05% 220ppm
建议使用使用方法:
1、电炉底部放置炉料三分之一后,将计算好的本产品放置炉料上,然后把剩余炉料按要求放在上面,如上面的炉料较大时应把一些碎的炉料压在增碳剂上,以防止漂浮影响吸收率。
2、加料顺序少量铁削、增碳剂、废钢、回炉料。基本上增碳剂吸收量为88%以上,******达到95%,升温达到1560°扒渣出炉即可。
炉内铁水不要出完,预留部分铁水,然后加增碳剂,再加铁屑,废钢等.增碳剂直接加到炉底会对增碳剂的烧损过大,在炉底预留一部分铁水加入更好些,或者炉底放一部分铁销也可以,那样吸收更高一些!
不建议用冲入法,它会降低本产品的吸收率,增碳剂在溶化时不要打渣,否则易裹在废渣里影响碳的吸收。
与传统生铁相比:
(1)、本产品使用中无残留,利用率高;
(2)、便于生产使用,节省企业生产成本;
(3)、磷硫含量大大低于生铁中含量,性能稳定;
(4)、使用石墨化增碳剂可以大幅度降低铸件生产成本。
石墨增碳剂使用方法
1、炉料要求:无油无锈, 废钢要求表面不许有过度氧化现象。
2、一般按每加入100公斤废钢加入增碳剂4.1-4.3公斤准备。
3、出炉温度控制在1550℃,预计球化降温100℃,手包降温50℃。
4、第一炉生产时采取在电炉底加入20公斤优质铁削。第二炉起生产时采取上一炉剩余铁液20-40公斤。
5、铁削加入后用塑料口袋装入规定配入的增碳剂放入铁削上。
第二炉起在剩余铁液20-40公斤上投入塑料口袋装得增碳剂投入铁液面。
6、加入碳素小颗粒(小于50×50面积)废钢50公斤,紧密覆盖整个炉塘。
7、启动熔化,加入剩余废钢→加配入生铁→加配入回炉铁(注意回炉铁的表面粘砂不要过多防止增碳剂与砂粘合影响吸收)。
8、铁液熔化完毕后用覆盖剂覆盖,温度达到1400℃时反复2-3次清理炉渣。
9、球化处理吊包装入球化剂、硅铁后用优质铁削覆盖表面。
10、熔炼完毕用优质除渣剂清理炉内液面溶渣2-3次,检测铁液温度1550℃-1600℃。
11、铁液出炉采用出铁三分之二铁液时,立即在炉嘴处顺流加入二次硅钡孕育剂。
12、用优质除渣剂清理溶渣。
八、柱状石墨增碳剂
增碳剂的类型
按照铸造用途分为:球铁增碳剂、灰铁增碳剂、铸钢增碳剂、特种钢增碳剂
1.球铁增碳剂一般选用石墨化的高碳低硫产品,对硫含量要求的比较严,一般控制在:S:≤0.1%,S:≤0.05%
2.灰铁增碳剂和球铁增碳剂的主要技术指标区别在于对硫的控制,一般指标要求是S:≤0.5%就可以
3.铸钢(炼钢)增碳剂的种类比较复杂,一般大型钢厂按照不同的钢种会选择多种增碳剂,但一般材料为煅煤和石墨粒或者石墨球,也有用天然石墨碎,含量从75%-99%不等。
固定碳和灰分是增碳剂中此消彼长的两个对立参数,也是影响增碳效率的两个最重要的参数。增碳剂中的固定碳含量高、灰分低,则增碳效率高,反之则增碳效率低。
增碳剂的加入方式对增碳剂吸收率有很大影响
1、【增碳剂在装料时加入炉内】
装料时将增碳剂与炉料混匀,置于感应电炉的底层和中部,增碳剂在装料时随金属炉料一同加入炉内,由于作用的时间长,增碳效率比出铁时加入铁液时高的多。增碳效率较高。
2、【增碳剂在装料时加入炉内】
出铁时在包内加增碳剂,增碳效率比加入炉内者低得多。
九、石墨粉
材料简介:
石墨粉质软,黑灰色;有油腻感,可污染纸张。硬度为1~2,沿垂直方向随杂质的增加其硬度可增至3~5。比重为1.9~2.3。在隔绝氧气条件下,其熔点在3000℃以上,是最耐温的矿物之一。
常温下石墨粉的化学性质比较稳定,不溶于水、稀酸、稀碱和有机溶剂;不同高温下与氧反应,生成二氧化碳或一氧化碳;在卤素中只有氟能与单质碳直接反应;在加热下,石墨粉较易被酸氧化;在高温下,还能与许多金属反应,生成金属碳化物,在高温下可以冶炼金属。
材料特质:
石墨粉是化学反应很灵敏的物质,在不同的环境里面他的电阻率都会变,也就是他的电阻值会变,但有一点是不会变的,石墨粉是很好的非金属导电物质之一,只要在绝缘的物体里面保证石墨粉不间断,像一条细线那样也会通电的,但是,电阻值是多少,这个数值也没一个准确的数,因为石墨粉的粗细不一样,用在不同的材料和环境石墨粉电阻值也会不一样。石墨由于其特殊结构,而具有如下特殊性质:
1) 耐高温型:石墨的熔点为3850±50℃,沸点为4250℃,即使经超高温电弧灼烧,重量的损失很小,热膨胀系数也很小。石墨强度随温度提高而加强,在2000℃时,石墨强度提高一倍。
2) 导电、导热性:石墨的导电性比一般非金属矿高一百倍。导热性超过钢、铁、铅等金属材料。导热系数随温度升高而降低,甚至在极高的温度下,石墨成绝热体。
3) 润滑性:石墨的润滑性能取决于石墨鳞片的大小,鳞片越大,摩擦系数越小,润滑性能越好。
4) 化学稳定性:石墨在常温下有良好的化学稳定性,能耐酸、耐碱和耐有机溶剂的腐蚀。
5) 可塑性:石墨的韧性好,可连成很薄的薄片。
6) 抗热震性:石墨在常温下使用时能经受住温度的剧烈变化而不致破坏,温度突变时,石墨的体积变化不大,不会产生裂纹。
应用案例
1、作耐火材料: 石墨及其制品具有耐高温、高强度的性质,在冶金工业中主要用来制造石墨坩埚,在炼钢中常用石墨作钢锭之保护剂,冶金炉的内衬。
2、作导电材料: 在电气工业上用作制造电极、电刷、碳棒、碳管、水银正流器的正极,石墨垫圈、电话零件,电视机显像管的涂层等。
3、作耐磨润滑材料: 石墨在机械工业中常作为润滑剂。润滑油往往不能在高速、高温、高压的条件下使用,而石墨耐磨材料可以在(一) 200~2000 ℃温度中在很高的滑动速度下,不用润滑油工作。
许多输送腐蚀介质的设备,广泛采用石墨材料制成活塞杯,密封圈和轴承,它们运转时勿需加入润滑油。石墨乳也是许多金属加工(拔丝、拉管)时的良好的润滑剂。
十、煤质增碳剂
增碳剂介绍
增碳剂的原料有很多种,生产工艺也各异,有木质碳类,煤质碳类,焦炭类,石墨类等,其中各种分类下又有很多小种类。优质增碳剂一般指经过石墨化的增碳剂,在高温条件下,碳原子的排列呈石墨的微观形态,所以称之为石墨化。石墨化可以降低增碳剂中杂质的含量,提高增碳剂的碳含量,降低硫含量。
增碳剂在铸造时使用,可大幅度增加废钢用量,减少生铁用量或不用生铁。电炉熔炼的投料方式,应将增碳剂随废钢等炉料一起往里投放,小剂量的添加可以选择加在铁水表面。但是要避免大批量往铁水里投料,以防止氧化过多而出现增碳效果不明显和铸件碳含量不够的情况。增碳剂的加入量,根据其他原材料的配比和含碳量来定。不同种类的铸铁,根据需要选择不同型号的增碳剂。增碳剂特点本身选择纯净的含碳石墨化物质,降低生铁里过多的杂质,增碳剂选择合适可降低铸件生产成本。
增碳剂作用
用于铸造,铸铁、铸钢,铸件会有对碳的一个要求,那么增碳剂顾名思义就是来增加铁液中的碳含量,又比如说,在熔炼中常用炉料为生铁、废钢、回炉料,生铁的碳含量高,但是却采购价格相对废钢来说是要高出一节的,所以增加废钢投放量,降低生铁投放量,加增碳剂,能起到一定的降低铸件成本的作用。
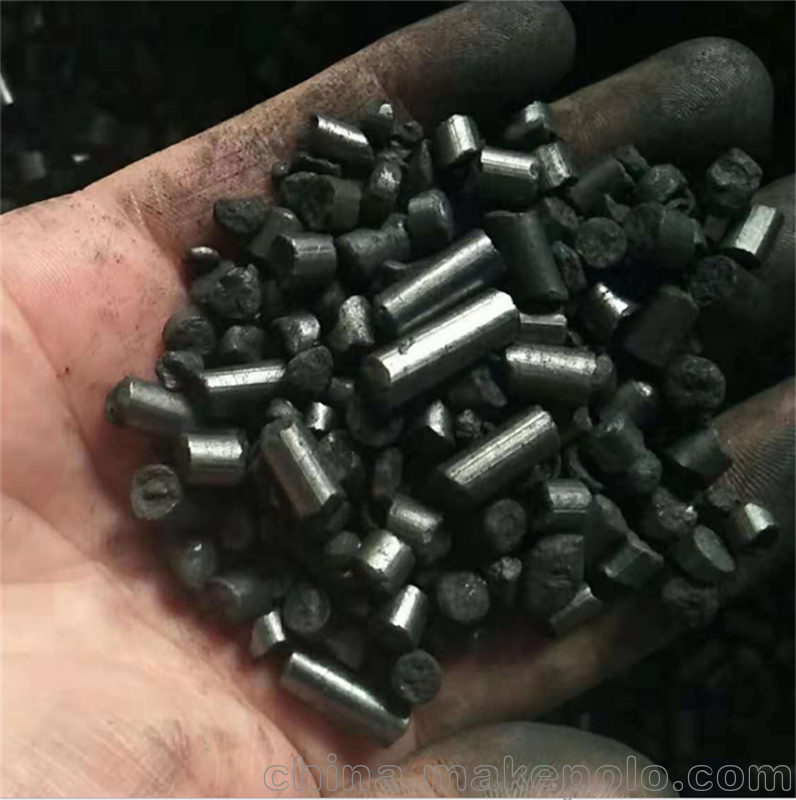
