隔膜是锂电池中的核心关键材料,是一个具有高技术壁垒的行业。 隔膜约占整个锂电池成本的 25%,其性能的好坏将直接影响到锂电池的安全性、一致性和稳定性。
隔膜在电池中的作用至关重要。隔膜是制造锂电池的四大原材料之一,位于锂电池的正负材料之间,承担着电池安全充电与放电的要务。由于锂电隔膜具有高技术壁垒,投入成本较其他锂电池材料更大,因此其毛利率高达 60%,是国家重点发展的产业之一。
隔膜的技术要求较高,需兼具安全性、一致性与稳定性。 锂电隔膜的耐热度、厚薄度、伸缩度等性能将直接影响锂电池的安全与稳定,若关键性能不达标,将会使锂电池内阻上升、导电性降低或正负极穿透,最终导致内部短路和引发事故。
锂电隔膜在安全性、一致性与稳定性方面技术要求高。隔膜技术壁垒高,进口替代空间大,隔膜成本占锂电池总成本约为 25%.
锂电池四大材料中,只有隔膜还未达到完全国产化,国产替代空间大,特别是高端隔膜缺口巨大。 据高工产研锂电研究所(GGII),我国 2016 年锂电池隔膜产量超过 10.84 亿平米。
国产替代从 2014 年的 65%上升到 2016 年85%, 但产品类型主要集中于中低端数码用隔膜,在品质要求高的数码产品及动力电池上,国内电池企业还是偏向进口隔膜。
湿法工艺得益于双向拉伸而使隔膜更薄,日后将成为高端隔膜主流。 目前隔膜主要有三种技术路线——干法单拉、干法双拉和湿法。 其中,干法双拉隔膜孔径的均匀性、一致性、稳定性相对较差, 只能用于中低端电池;干法单拉隔膜成本较低、热稳定性较好, 但只进行了纵向拉伸而没有进行横向拉伸, 使用时横向容易开裂而不能做薄(一般为 20 到 50 微米),且较容易短路;湿法隔膜因此拉伸强度和穿刺强度都比较高,产品可以做薄(大约到 5 微米),同时短路率也较低,但相对成本较高,熔断温度与热稳定性也较差。
指标检测:根据国标,行标等标准方法进行检测;
仪器共享:根据仪器标准或客户提供标准进行测试;
主成分分析:含量高成分或者您指定的某一个成分检测,5-7个工作日。
成分分析:根据成品进行逆向剖析,还原出原料化学名称和大概配比,10个工作日内。
深度分析:在成分分析基础上,购买原料标准品进行定性定量检测,再提供参考工艺和原料推荐厂家,20-40工作日。
模仿开发:在深度分析基础上,购买原料进行小样配制
专业配方分析,产品改进,质控测试
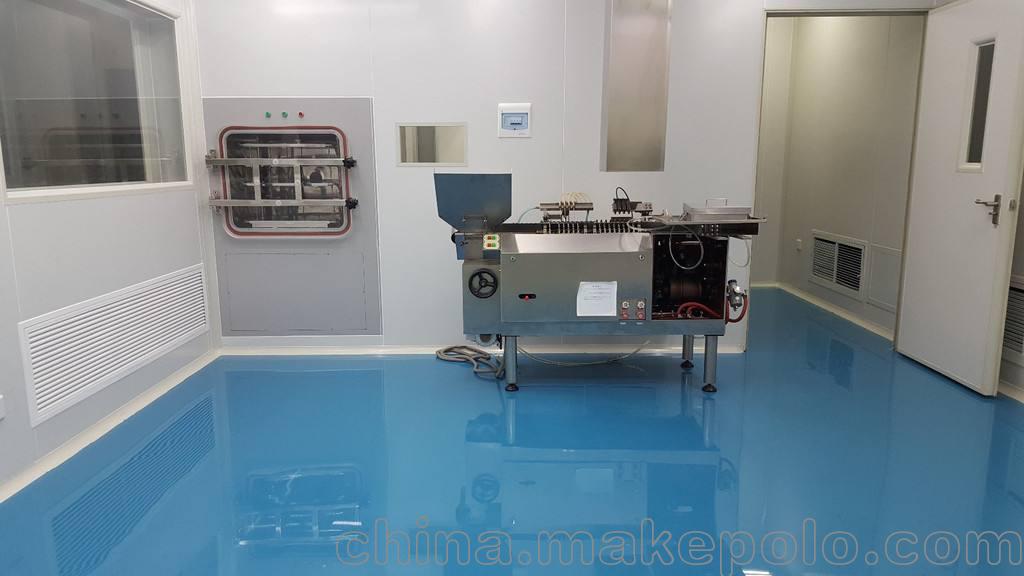
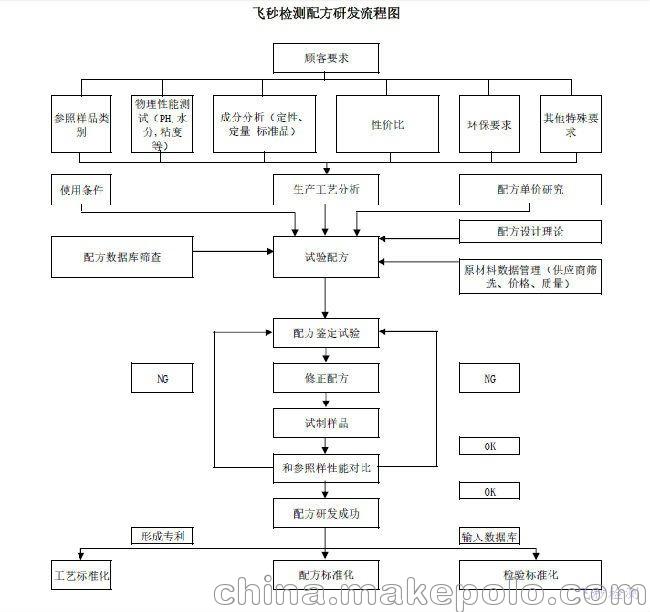