在铝工业的生产流程中,精炼剂作为一种关键的辅助材料,扮演着至关重要的角色。它不仅关乎铝液的质量,还直接影响到产品的性能与成本。本文将深入探讨铝业精炼剂的用量标准、作用机制、使用方法、使用效果及其影响因素,以及不同类型精炼剂的应用场景,旨在为铝业从业者提供一份详尽而实用的指南。


### 精炼剂的用量标准
铝业精炼剂的用量标准通常为铝液重量的0.1%~0.5%,这一范围并非一成不变,而是需要根据铝液的具体情况进行灵活调整。在实际操作中,每吨铝液精炼时所需的精炼剂大约在100~200公斤左右。这一用量的确定,需综合考虑铝液的质量、所含杂质的种类和含量、精炼目的及预期效果等多方面因素。例如,对于杂质含量较高的铝液,可能需要适当增加精炼剂的用量,以确保精炼效果;而对于质量要求极高的高端铝合金,则需更为准确地控制精炼剂用量,以避免过度精炼带来的负面影响。
### 精炼剂的作用与使用方法
精炼剂的主要作用是清除铝液内部的氢和浮游的氧化夹渣,使铝液更加纯净。氢是铝液中的主要气体杂质,它的存在会降低铝材的力学性能和耐腐蚀性;而氧化夹渣则会影响铝材的表面质量和加工性能。精炼剂中的部分组元在高温下极易分解,生成的气体与铝液中的氢发生反应,形成气泡并上浮至液面,从而将氢和氧化夹渣一并带出。
使用精炼剂时,通常将其以粉末或颗粒状均匀撒入铝液中,并伴随适当的搅拌或吹气操作,以促进精炼剂与铝液的充分接触和反应。精炼时间、温度以及精炼剂的撒入方式等因素均会影响精炼效果。一般而言,精炼应在铝液温度达到适宜范围(通常高于液相线温度50~100℃)后进行,且应持续至铝液表面无明显气泡冒出为止。
### 精炼剂的使用效果与影响因素
精炼剂的使用效果直接决定了铝液的质量,进而影响产品的性能。然而,精炼效果并非仅由精炼剂本身决定,还受到多种因素的影响。铝液的纯净度是基础,若铝液中原有杂质含量过高,即使使用再多的精炼剂也难以达到理想的精炼效果。熔炼炉的大小和形状也会影响精炼剂的分布和反应效率。此外,精炼时间、温度以及精炼剂的撒入方式等工艺参数同样对精炼效果有着重要影响。
值得注意的是,过多的精炼剂不仅会增加生产成本,还可能对铝液造成不必要的污染。这是因为精炼剂在高温下分解产生的气体和残留物可能残留在铝液中,影响铝材的纯净度和性能。因此,在使用精炼剂时,应严格控制用量,避免过度精炼。

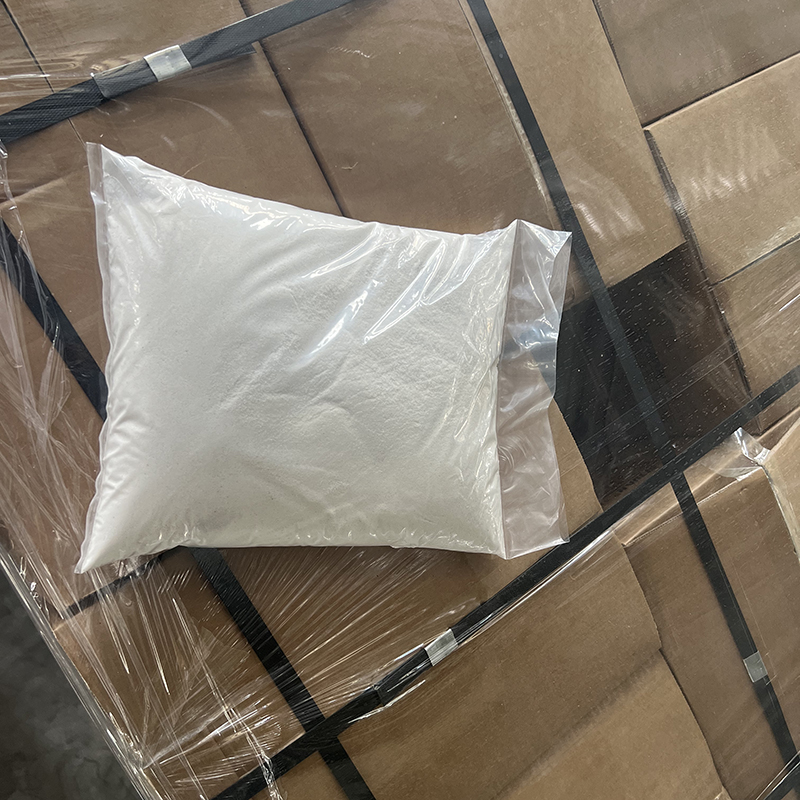
### 不同类型精炼剂的应用场景
随着铝工业的发展,市场上出现了多种类型的精炼剂,以满足不同铝合金和纯铝熔炼的需求。其中,无钠精炼剂以其独特的优势在高强度铸造铝合金熔炼中得到了广泛应用。由于钠元素在铝合金中可能引发“钠脆”现象,降低材料的强度和韧性,因此无钠精炼剂成为了高强度铸造铝合金的理想选择。它不仅能有效去除铝液中的氢和氧化夹渣,还能避免“钠脆”现象的发生,提高产品质量。
此外,一些品牌的精炼剂还兼具环保经济的优点。它们通过优化配方和生产工艺,减少了精炼过程中产生的烟雾和烧损,提高了金属液的收益率。这类精炼剂不仅有助于降低生产成本,还能减少对环境的影响,符合当前绿色制造的发展趋势。
在实际应用中,选择何种类型的精炼剂需根据具体铝合金的成分、熔炼条件以及产品要求等因素综合考虑。例如,对于要求高强度和良好耐腐蚀性的铝合金产品,应优先选择无钠精炼剂;而对于追求低成本和环保效益的铝合金熔炼过程,则可考虑使用环保经济型的精炼剂。

### 结语
综上所述,铝业精炼剂在铝工业生产中发挥着举足轻重的作用。其用量标准的确定、作用机制的理解、使用方法的掌握以及使用效果的评估均需基于科学的分析和实践经验的积累。同时,随着铝工业的不断发展和技术的不断进步,精炼剂的性能和种类也将持续优化和创新。作为铝业从业者,我们应紧跟时代步伐,不断学习新知识、新技术和新方法,以推动铝工业的持续健康发展。