一. 机床性能、特性、规格
1. 机床性能简介
l 床身(坚实铸铁结构)
A) 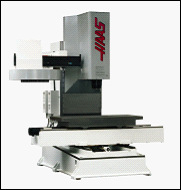
采用美国先进的电脑技术及最优化设计方法设计分布在机床内部的各类加强筋及床身、立柱、工作台等各大部件的尺寸, 使之以尽可能低的重量承载最大的负荷。
B) 采用铸件优化设计软件对铸件的结构形式、尺寸进行优化分析和检测。
C) 采用最先进的“密烘”铸造技术成形各部分构件,使之达到高抗振性及高刚性, 其吸震能力比普通铸铁高10倍.提高了机床的稳定性。在取走一个调平螺丝的情况下,机床仍能平稳地进行精密切削, 并且在安装时不需任何专门的地基.
D) 机床底座为三角形受力设计, 有6只粗大螺栓支承并定位。
E) 机床立柱为A型结构,彻底排除机床在加工过程中立柱产生的偏移摆动。
l 主轴箱
A) 主轴箱内有一包围主轴的外套, 通向切削区的冷却液经此外套预先带走主轴的热量, 而不是等热量传至加工区内再冷却, 这样可以保证机床的整体温度、精度的稳定.
B) 主轴电机为矢量控制, 全封闭系统能够在最大的速度范围内保证主轴的最大力矩输出. 另外, 提供了更快的加速度、减速度, 及更快的主轴定位.
C) 主轴承前后两端各有二个径向上推轴承承受很高的轴向负载, 以提高其径向稳定性, 使机床可以对钢进行重载切削.
D) 外形是对称结构设计,外面分布有铸铁加强筋, 因而增强了主轴刚性,保证机床在超重切削时仍能稳定运行。此外, 还减少了热膨胀变形(在超重切削时,热膨胀变形是0.0016英寸), 膨胀性质是单一线性膨胀,非复合性膨胀。
l 导轨
A) 采用THK、NSK或STAR淬硬滚动导轨组件, 固定在整体铸造出并精密加工完成的矩形导轨上.
B) 滚动导轨组件在上下左右都按同一额定负荷设计, 使其具有高刚性, 适合重型切削.
C) 滚动导轨组件安装时除底面固定外, 左右两面也有固定使其精度非常稳定.
D) 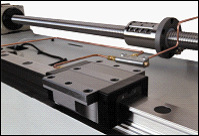
采用名厂生产的优质导轨,经过淬硬和精密磨削而成。滑块与导轨间在各个方向均为零间隙并可承受全负荷。其优点是消耗功率小,不象带有镶条的导轨那样需经常调整。实践证明,这种导轨在精度和速度方面都优于滑动导轨。为了保证其使用寿命, 每一导轨面均采用独立的自动润滑.
l 双支座滚珠支承丝杠
采用机械行业中最高质量标准的优质丝杠和导轨以保证机床的高精度和长寿命。丝杠在两端紧固并加以预应力,且经严格检测确保丝杠百分百平行于导轨。
l 进给机构
A) 三轴均为高速无刷伺服电机, 可获得更高速度、加速度及功率, 运动的平稳性和精度的保持性也大大增强.
B) 伺服电机用钢盘联轴器直接与丝杆连接, 即使在重负荷下也不会有弹性变形, 加工时能切削出更尖的角度及插补出更精确的圆孔.
C) 对机床的定位精度有大幅度提高, 机床沿各轴最小的移动距离为0.001mm, 机械系统的分辨率高达0.18μ(0.00018mm).
D) 各坐标轴, 特别是Z轴都装有全封闭罩, 保证加工时切屑及切削液不会飞溅其中.
l 固定式,双轴耳轴转台
哈斯耳轴转台倾斜轴±120?,旋转轴360?,可提供完全五轴联动,几乎可将工件定位于任何角度.耳轴转台的程序可直接通过加工中心的控制器.
l 强力20马力矢量驱动
高性能马达与哈斯设计的矢量驱动的结合产生了最快、最强有力的主轴输出. 真正的
闭环系统使低速扭矩和加速度提高了一倍. 产生的最大扭矩是102 Nm /1,400 rpm.
l 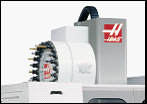
高速侧挂式刀库
A. 刀库由伺服电机驱动的电气控制换刀装置, 不同于大多数厂家的液压换刀机构, 从而提高了换刀的稳定性及速度.
B. 换刀采用正弦波式加减和减速运动, 避免了与刀具与机床的冲突,拥有更快的换刀速度,刀对刀的换刀时间只需2.8秒.
l 
高速加工(HSM)
减少循环时间和提高精度的有力工具。哈斯的HSM选件采用“插补前加速”运算法则及高达80程序块的全前瞻功能,连续进给可达500ipm, 同时不会发生编程路径的失真。该功能与ISO标准G代码兼容,成本仅为其它类型高速控制的几分之一。
l 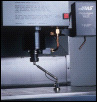
装运前进行100% 球杆检测
哈斯采用严格的球杆检测,不仅检测机床的线性精度,还检测机床
的几何精度,因此可确保每台机床的三维垂直度和精度。
.
2. 其它性能
l
l 易于排屑的机床罩壳设计
l 宽底面三角形铸件布局
l 水冷主轴头
l 直接耦合伺服电机
l 高切削能力的主轴部件
l 便于维护的带滚轮的冷却液箱