无锡华尚环保科技有限公司专业致力于冶金行业、焦化行业、燃煤电力、垃圾发电及化工行业的固废、气废处理工程,期待能与同行一道为中国的环保行业做出贡献!
联系人:周经理
电话:18600635336
邮箱:huashanghuanbao@yeah.net
电站锅炉、工业锅炉、焚烧炉、燃气轮机等的烟气会向环境排放NO和NO2等氮氧化物(通称为"NOX"),氮氧化物(NOX)是造成大气污染的主要污染物,目前国内65%的NOX是燃煤产生的,而我国又是最大的煤炭生产国和消费国,因NOX对人体有害、引发酸雨、并且是光化学烟雾的重要产生原因,据专家预测,如不采取有效措施,随着工业的发展在未来5-10年内NOX的排放将超过SO2而成为第一大酸性污染物。使用的吸收剂? 石灰 NOX的排放受到越来越严格的限制,现有控制NOX排放的技术主要有三种:
1、分级燃烧,实施方式包括低NOX燃烧器(LNB)和燃料再燃。但分级燃烧技术对NOX的生成和排放控制有一定限度,LNB一般只有30-50%的效率,再燃的效率约为50-60%,单采用分级燃烧难以达到NOX的排放控制标准。 还原剂在最佳温度窗口的停留时间越长,则脱除NOx的效果越好。NH3的停留时间超过1 s则可以出现最佳NOx脱除率。尿素和氨水需要0.3 s~0.4 s的停留时间以达到有效的脱除NOx的效果。
2、选择性催化还原(SCR),即在催化剂表面、通过氨或尿素等含氮还原剂(N-agent)来还原NOX。一般SCR系统安装在420℃左右的烟气温度范围。 4NH3+5O2→4NO+6H2O虽然SCR系统能相对容易地实现80-90%的NOX降低率,但此方法存在的缺点是:需要设置催化剂反映塔、催化剂费用高、烟气中导致催化剂失效的因素较多,燃煤时催化剂的使用寿命仅约为四年,而且失效的催化剂是危险固废。甘南藏族自治州 SCR超低排放总包公司石灰石? 石灰?
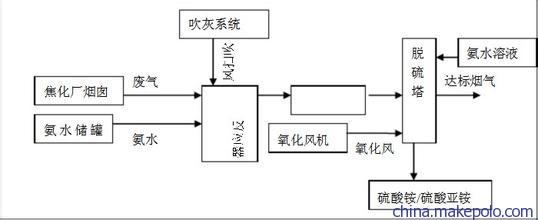
3、选择性非催化还原法(SNCR),在高温段将还原剂喷入从而将NOX还原为分子态的氮,现有技术中常用的还原剂是氨和尿素,此时SNCR只在一个很狭窄的温度范围内(氨:900-1100℃;尿素:900-1500℃)有效。温度更高的条件下,还原剂本身被氧化成NO;而低于最佳反映温度时,选择性还原反应速度很慢从而造成未反应的还原剂泄漏(如氨泄漏)。3)氨与空气的混合气体在反应器的适当位置喷入烟气,其位置通常在反应器的入口附近的烟气管路内;而且在现有的燃烧系统中,最佳温度范围(即通常被称为"温度窗口")可能随时燃烧工况的变化(如锅炉负荷的变动)和烟道内较大的温度梯度的变化而发生改变,这给还原剂的喷射位置的确定带来了很大的困难。该脱硫工艺以氨水为吸收剂,副产硫酸铵化肥。锅炉排出的烟气经烟气换热器冷却至90~100℃,进入预洗涤器经洗涤后除去HCI和HF,洗涤后的烟气经过液滴分离器除去水滴进入前置洗涤器中。在前置洗涤器中,氨水自塔顶喷淋洗涤烟气,烟气中的SO2被洗涤吸收除去,经洗涤的烟气排出后经液滴分离器除去携带的水滴,进入脱硫洗涤器。在该洗涤器中烟气进一步被洗涤,经洗涤塔顶的除雾器除去雾滴,进入脱硫洗涤器。再经烟气换热器加热后经烟囱排放。洗涤工艺中产生的浓度约30%的硫酸铵溶液排出洗涤塔,可以送到化肥厂进一步处理或直接作为液体氮肥出售,也可以把这种溶液进一步浓缩蒸发干燥加工成颗粒、晶体或块状化肥出售。除温度窗口外,影响SNCR的效果的因素还有烟气中的氧量等。湘西土家族循环硫化床超低排放总包公司费用
目前,国内外已开发出很多种NOX的脱除工艺,在各种NOX脱除工艺中,燃煤锅炉采用M型NOX低燃烧器及M型炉内燃烧脱NOX相结合的方法,可用于炉内主燃烧器燃烧区,未燃烧燃料和还原区,完全燃烧区,高温区和中温区脱除NOX,且能耐受烟气中氧量升高,脱NOX还原剂泄露少的炉内脱NOX新技术。2.3.1 高尘SCR系统具有不改变锅炉原有结构、无需巨额的前期改造资金、不改变现行的锅炉操作方式、无需占用大量的场地,占地面积小、脱NOX成本低、设施简单等优点,尤其适合老旧电厂进行脱NOX技术改造。实验数据表明,炉内脱NOX效率≥80%。该技术可达到较高的脱NOX效率而不需要昂贵的催化剂,比采用选择性催化还原法(SCR)和非催化性还原法(SNCR)技术的投资节省50%-70%,运行和维护费用节省60%-75%,脱NOX工艺简单,性能优越,省去了还原剂氨尿素及铵盐的添加,解决了催化剂堵塞和老化失效更换的问题,节约了大量的资源。 二、烟气生物脱硫原理烟气中的SO2通过水膜除尘器或吸收塔溶解于水并转化为亚硫酸盐、硫酸盐;在厌氧环境及有外加碳源的条件下,硫酸盐还原菌将亚硫酸盐、硫酸盐还原成硫化物;然后再在好氧条件下通过好氧微生物的作用将硫化物转化为单质硫,从而将硫从系统中去除。可以将烟气生物脱硫过程划分两个阶段,即SO2的吸收过程和含硫吸收液的生物脱硫过程。2.1吸收SO2的工作原理M型低NOX燃烧器与M型炉内燃烧脱NOX相结合的脱NOX方法,是一种无需大的设备投入,不用催化剂和免除还原剂氨泄漏,设备投资少,可用于炉内高温区和中温区脱除NOX且能耐受烟气中氧量升高、脱NOX还原剂泄露少的M型低NOX燃烧器和M型炉内燃烧脱NOX相结合的炉内脱NOX技术方法。顺流填料塔
一、NOX炉内燃烧控制技术
某燃煤电厂3台600MW燃烧锅炉辐射再热式、超临界压力、变压运行直流燃煤锅炉,额定蒸发量为1950t/h。炉内脱NOX系统采用M型低NOX燃烧器和M炉内燃烧脱NOX2部分组成。商业化石膏、堆入灰场、回填
当一次风的空气/煤粉比值在0-Cmax之间时,NOX的产生量随空气/煤粉比的增加而增大;在空气/煤粉比接近Cmax时(煤中挥发性物质完全燃烧所需要的理论空气量与煤粉量之比),NOX的产生量出现最高值;当空气/煤粉比在Cmax-Cmin之间时,NOX的生产量随空气/煤粉比的增加而减少;在空气/煤粉比接近Cmin时(煤粉完全燃烧所需要的理论空气量与煤粉量之比),NOX的产生量达到最低值;当一次风的空气/煤粉比>Cmin,NOX的产生量随空气/煤粉比的增加而急剧增加。(三)具备烟气脱硫工程总承包能力。截止2005年底,具备一定技术、资金、人员实力,且拥有10万千瓦及以上机组烟气脱硫工程总承包业绩的公司近50家;其中,合同容量超过200万千瓦装机的公司有17家,超过1000万千瓦装机的公司有7家。北京国电龙源环保工程有限公司总承包合同容量达到了2471万千瓦。
一般情况下,一次风的空气/煤粉比在C0附近,有时可能达到Cmax,这主要决定于干燥煤粉和输粉的条件。在煤的燃烧过程中,NOx的生成量和排放量与燃烧方式,特别是燃烧温度和过量空气系数等密切相关。燃烧形成的NOx可分为燃料型、热力型和快速型3种。其中快速型NOx生成量很少,可以忽略不计。因此,采用一次风不分股的低M型NOX燃烧器时,燃料燃烧所生成的NOX相当于(NOX)C0,NOX的生成量就有可能接近峰值;如果减少一次风的量,控制一次风的空气/煤粉比在较低水平,使煤粉在浓燃料条件下燃烧,虽然可以降低NOX的生成量,维持稳定燃烧,但飞灰中的未燃碳将很高。2.3 SCR反应系统的布置方式反之,如果增加一次风量,将一次风的空气/煤粉比控制在较高水平,使煤粉在稀燃料条件下燃烧,虽然可以减少NOX的生成量和飞灰中的未燃碳,但燃烧不稳定。甘南藏族自治州 SCR超低排放总包公司氮氧化物NOx可用燃烧前、燃烧中和燃烧后的方法脱氮。燃烧前脱氮是对燃料(主要是煤) 进行脱氮处理,其成本较高,也较困难,该项技术尚待进一步研究。现在用得较多的是煤在燃烧中和燃烧后脱氮。
为解决类似矛盾,在一次风不分股的SGR型低NOX燃烧器的基础上,研制了M型低NOX燃烧器,将一次风分成浓燃料和稀燃料2股,其一次风的空气/煤粉比与NOX的生成量的关系亦如图1所示。浓燃料燃烧的空气/煤粉比在C1附近,生成的NOX为(NOX)c1;稀燃料燃烧的空气/煤粉比在C2附近,生成的NOX为(NOX)c2;一次风与粉煤燃烧生成的总NOX相当于(NOX)PM;SGR型低NOX燃烧器生成的NOX为(NOX)c0, 该脱硫工艺在芬兰、美国、加拿大、法国等国家得到应用,采用这一脱硫技术的最大单机容量已达30万千瓦。 显然,(NOX)PM<(NOX)c0,由于浓燃料燃烧时的粉煤浓度大、着火温度低,产生了易于着火的粉煤气流,同时,浓相煤粉着火后产生集中的火焰,提供了稀相煤粉气流的着火能量,既提高了着火的稳定性,又降低了飞灰中的未燃碳。甘南藏族自治州 SCR超低排放总包公司目前,国内外已开发出很多种NOX的脱除工艺,在各种NOX脱除工艺中,燃煤锅炉采用M型NOX低燃烧器及M型炉内燃烧脱NOX相结合的方法,可用于炉内主燃烧器燃烧区,未燃烧燃料和还原区,完全燃烧区,高温区和中温区脱除NOX,且能耐受烟气中氧量升高,脱NOX还原剂泄露少的炉内脱NOX新技术。具有不改变锅炉原有结构、无需巨额的前期改造资金、不改变现行的锅炉操作方式、无需占用大量的场地,占地面积小、脱NOX成本低、设施简单等优点,尤其适合老旧电厂进行脱NOX技术改造。实验数据表明,炉内脱NOX效率≥80%。该技术可达到较高的脱NOX效率而不需要昂贵的催化剂,比采用选择性催化还原法(SCR)和非催化性还原法(SNCR)技术的投资节省50%-70%,运行和维护费用节省60%-75%,脱NOX工艺简单,性能优越,省去了还原剂氨尿素及铵盐的添加,解决了催化剂堵塞和老化失效更换的问题,节约了大量的资源。M型低NOX燃烧器与M型炉内燃烧脱NOX相结合的脱NOX方法,是一种无需大的设备投入,不用催化剂和免除还原剂氨泄漏,设备投资少,可用于炉内高温区和中温区脱除NOX且能耐受烟气中氧量升高、脱NOX还原剂泄露少的M型低NOX燃烧器和M型炉内燃烧脱NOX相结合的炉内脱NOX技术方法。
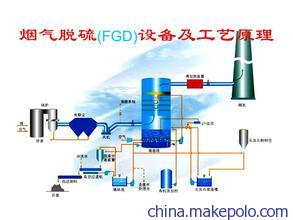
1、 M型炉内燃烧脱NOX法
(1)工作原理
锅炉燃烧所产生的烟气,大约95%的NOX是NO。在炉膛内,NO有可能发生2种截然相反的化学反应:a在较低的反应温度和较高浓度O2的条件下,NO与O2发生氧化反应,生成NOX。b在较高的反应温度和较低浓度O2的条件下,NO与煤炭发生还原反应,生成无害的N2。选择性催化还原法(Selective Catalytic Reduction,SCR)是指在催化剂的作用下,利用还原剂(如NH3)"有选择性"地与烟气中的NOx反应并生成无毒无污染的N2和H2O。选择性是指在烟气脱硝过程中烟气脱硝催化剂有选择性地将NOx还原为氮气,而烟气中的SO2极少地被氧化成SO3。这就叫选择性在发生NO还原反应的同时,由于空气量不足,将造成烟气中的碳氢化合物和CO等可燃性物质增加。甘南藏族自治州 SCR超低排放总包公司2、烟气/氨的混合系统 主要设备:稀释风机、静态混合器、氨喷射格栅(AIG)、空气/氨混合器。在这种情况下,应当在NO还原反应的下游区域,(6) 氨的逃逸量。分级供给燃料完全燃烧所需要的空气量,使得燃烧完全燃烧。二是对生成的NOx进行处理,即烟气脱硝技术。
M炉内燃烧脱NOX法的基本原理如图3所示。燃料燃烧所需要的空气通过燃烧器喷嘴(MB)、然尽风喷嘴(OFA)和增量风喷嘴(AA)分3次在3个不同的燃烧区域供给,在炉膛内形成1.主燃烧气燃烧区2.未燃烧燃料和还原区3.完全燃烧区等3个不同的燃烧区或使得燃烧在3个不同的空气/燃料区域内完成,以实现空气的分级燃烧,延长完全燃烧的时间,降低炉膛温度水平,从而有效的抑制NOX产生,并保证燃料的完全燃烧。SCR系统主要设备。
3、燃烧过程
如图3所示,M炉内燃烧脱NOX在各个燃烧区域的燃烧过程如下:
(1)主燃烧器燃烧区。在该区域,煤粉分成浓相燃料和稀相燃料2股,分别通过浓相燃料喷嘴和稀相燃料喷嘴由一次风送入燃料室,并与二次风在喷燃器口混合入炉燃烧,由于此燃烧区域内空气/燃料比较小,燃料供养不足、炉温较低,不仅减少了燃料型NOX的生成量,而且很少生成热力型NOX。其主要化学反映为:
CnHm+O2→CO2+H2O (1)
N+O2→NO (2)
(2)未燃烧燃料和还原区。当燃烧着的气粉流与燃尽风喷嘴(OFA)供给的燃尽风相遇时,燃烧进入未燃烧燃料和还原区域。在此区域内,燃料因接触到补充的空气而进一步燃烧,炉温相对升高,同时,煤炭参与燃烧。由于此区域内空气/燃料比刚刚接近于燃烧所需要的理论空气量,燃料供氧仍然不足,煤炭的还原能力很强,部分NOX被还原,因此,实际生成的NOX反而减少。 三、荷兰的Bio-FGD工艺 1992年,荷兰HTSE&E公司和Paques公司开发的烟道气生物脱硫工艺(Bio-FGD)标志着烟气生物脱硫技术领域达到了实用技术水平。3.1 Bio-FGD工艺流程90年代初,荷兰Wageningen农业大学在厌氧处理硫酸盐废水领域进行了大量研究,并开发了回收单质硫的生物脱硫工艺。荷兰HTSE&E公司和Paques公司将这一新技术应用于烟气生物脱硫工程:从1992年5月开始实验室运行,到1993年7月的中试运行,积累了不少经验,使工艺的发展日趋成熟。目前Bio-FGD工艺对中小型锅炉烟气治理已进入实用化阶段,其示范工程处理电厂废气量达200万m3/h。Bio-FGD工艺主要通过1个吸收器和2个生物反应器去除气体中的SO2。吸附器首先吸收烟气中的SO2,并且是唯一与气体接触的单元。在第1个反应器通过厌氧生物处理形成硫化物,在第2个反应器通过好氧生物处理将硫化物氧化成高质量的单质硫,其工艺流程如下图所示:Bio-FGD工艺包括4个主要部分:吸附器、厌氧反应器、好氧反应器、硫回收。(1)采用立式的喷淋塔作为吸附器,该吸附器与传统的氢氧化钠洗涤器作用相同。吸附器提供了雾化水滴,从而加速了气液传质过成,提高了液气比;该吸附器中SO2去除率与气液接触密切相关,同时pH的影响也至关重要。(2)厌氧反应器采用内循环反应器,在厌氧反应器中亚硫酸盐和硫酸盐被硫酸盐还原菌还原成硫化物,烟气吸收液中的烟尘与重金属硫化物的沉淀也被增长的生物物质所捕获并与剩余生物污泥一起除去。含有污染物的污泥可以在电厂与煤一起燃烧而不会产生另外的污染源。(3)好氧反应器采用气提反应器,在好氧反应器中好氧微生物将前一步形成的硫化物氧化成硫元素。与此同时,废液中的pH值得以回升这与吸附器中SO2吸附到水中引起pH值降低的反应互逆。吸收液由于相互抵消变成中性,从而可以减少药剂投加量,并削弱吸收液对吸附器的腐蚀。(4)将好氧反应器出水中的单质硫进行回收,回收工艺由气浮池、斜板沉淀池、真空转鼓过滤器等组成。回收硫中只有少量的微生物,其纯度达92%。3.2 Bio-FGD工艺的中试结果 1993年HTSE&E和Paques公司首先将Bio-FGD工艺应用于规模为50MW电厂的烟气治理,在该处理系统顺利运转的基础上,Bio-FGD工艺被进一步放大——在荷兰南部Ceertridenberg的600MW火力发电站建立了烟道气生物脱硫中试工厂。设备尺寸:吸附塔高6m;厌氧内循环反应器高10m、直径1m;好氧气提循环反应器高8m;利用斜板沉淀池以浓缩回收硫。烟气流量:2000~8000m3/h;SO2含量:3000mg/m3(这一规模相当于国内3t锅炉产生的废气水平)。 中试系统在启动6周内能培养出稳定的高温微生物并有75%的SO2转化为单质硫,剩余的25%转化为多联硫酸盐。经过6周后,系统满负荷运行在6.0kgSO2/h下,SO2几乎全部转化为单质硫。中试系统吸收液大部分循环利用,只生产少量的废水。根据中试研究可以得出,煤炭火力发电厂生产的高温有毒烟气用微生物处理是非常合适的。3.3 Bio-FGD工艺的技术经济比较在假定电厂用煤含硫率1.5%、系统SO2去除率90%的条件下,对Bio-FGD和LSFO两种工艺在300MW和600MW火力发电厂的投资和运行费用进行核算,最后最后确认Bio-FGD工艺的总投资费用比LSFO大约低30%。Bio-FGD工艺投资低的主要原因是所需的吸收器容积负荷高得多,另外制造工艺处理设施的用料也大量减少。Bio-FGD工艺的费用与烟气中硫含量的大小有关,硫含量的大小与系统的外加碳源(如甲醇)的用量成正比;对于600MW发电厂,Bio-FGD工艺与LSFO工艺相比在浓度3g/Nm3时的费用最占优势。总之,多方面研究表明,对于规模50~600MW发电厂,脱硫率90%时Bio-FGD比LSFO工艺的费用低得多,而小型发电厂的优势则更为突出。3.4 烟气生物脱硫的优点(1)费用比石灰/石膏强制氧化工艺(LSFO)工艺低30%;(2)高脱硫率(高达98%);(3)高价值的副产品单质硫;(4)吸收液全部循环利用;(5)改进现有的LSFO工艺费用低;(6)使用范围广,能够解决环境问题。3.5 Bio-FGD工艺的深入研究领域 Bio-FGD工艺从实验室经中试并最终应用于实际的烟气治理,其处理装置的最优化、运行条件的最优化、微生物物种的筛选确定、活性污泥附着状态的选择、外加碳源的进一步开发等等仍然是发展Bio-FGD工艺必须进行的研究项目。其中外加碳源即“电子供体”的筛选本着价格低廉、有机废物回用的原则进行,已确定乙醇、甲醇、合成气(即H2、CO、CO2的混合体)等可以作为SRB的外加碳源。Houlen研究表明,小规模装置(5~10kmolSO2/h)中实用合成气要为便宜。3.6 Bio-FGD工艺的应用领域Bio-FGD工艺可以应用于以下领域的脱硫:火力发电厂脱硫和中小锅炉的脱硫;硫酸生产厂(在这种情况下,产生的元素硫也可作为原料);焚烧炉废气脱硫;化学和石油化学装置(炼油的酸性废气)。利用改进的Bio-FGD工艺从气体中去除硫化氢,这样的工艺适合于:天然气的净化;煤气净化。主要化学反应为:
CnHm+O2→H2+CO+Cn′Hm′ (3)
Cn′Hm′+NO→Nhi+N2+Cn′′Hm′′ (4)
(3)完全燃烧区。在炉膛上部,通过增量风喷嘴(AA)将燃料燃烧所需要的过量空气送入炉膛,形成完全燃烧区。在该区域内,由于过量空气的存在,保证了煤粉的完全燃烧及锅炉的效率,将飞灰的含碳量控制在合理的范围内。联合脱硫脱硝技术的脱硫和脱硝分步进行,NOx的脱除仍以传统的SCR 和SNCR 为主;国外的研究开发较早,相关工艺研究较为成熟,已有成套的工艺设备;但该法在实现商业化运营中遇到一定的困难,主要是因为相关政策导向不够和技术竞争力不强。同时,由于过量空气的存在烟气中存在的过剩氧气与游离氮结合生成部分NOX。但是,此时燃烧温度已降低,NOX的生成量是有限的。甘南藏族自治州 SCR超低排放总包公司 4NH3+5O2→4NO+6H2O主要化学反应为:
Cn′′Hm′′+ O2→CO2+H2O (5)
Cn′Hm′+O2→CO2+H2O (6)
CO+H2+O2→CO2+H2O (7)
Nhi+ O2→NO+N2 (8)
3、技术特点
(1)对燃料的适应性强,适用于煤、油、汽等燃料:
(2)不增加机组运行费用,不用触媒,也不需要喷氨;
(3)不增加新的环境污染物;全尺寸电厂应用实例较少、若干运行经验
(4)锅炉效率和烟气量不发生变化;
(5)锅炉运行状况好,燃烧稳定,能保证锅炉的安全运行;
(6)脱NOX效率高,最高可达50%; 喷雾干燥法脱硫工艺具有技术成熟、工艺流程较为简单、系统可靠性高等特点,脱硫率可达到85%以上。该工艺在美国及西欧一些国家有一定应用范围(8%)。脱硫灰渣可用作制砖、筑路,但多为抛弃至灰场或回填废旧矿坑。?
二、M型炉内燃烧脱NOX法的运行与控制效果
某燃煤厂1~3号机组600MW燃煤锅炉采用双炉膛、双火球设计,同时采用M型低NOX燃烧器和M型炉内燃烧脱NOX法控制NOX。某燃煤电厂3台600MW燃烧锅炉辐射再热式、超临界压力、变压运行直流燃煤锅炉,额定蒸发量为1950t/h。炉内脱NOX系统采用M型低NOX燃烧器和M炉内燃烧脱NOX2部分组成。每台炉有5层,每层布置8只,共40只,M型低NOX燃烧器,16只油燃烧器。 选择性非催化还原(SNCR)脱除NOx技术是把含有NHx基的还原剂(如氨气、氨水或者尿素等)喷入炉膛温度为800℃~1 100℃的区域,该还原剂迅速热分解成NH3和其它副产物,随后NH3与烟气中的NOx进行SNCR反应而生成N2。每台锅炉共设计80个一次风喷嘴、24个二次风喷嘴、16个带油枪的二次风喷嘴、8个燃尽风喷嘴(OFA)/24个增量风喷嘴(AA),以实现空气的分级燃烧,有效地抑制NOX的产生,同时保证燃料的完全燃烧。M炉内燃烧脱NOX法的基本原理如图3所示。燃料燃烧所需要的空气通过燃烧器喷嘴(MB)、然尽风喷嘴(OFA)和增量风喷嘴(AA)分3次在3个不同的燃烧区域供给,在炉膛内形成1.主燃烧气燃烧区2.未燃烧燃料和还原区3.完全燃烧区等3个不同的燃烧区或使得燃烧在3个不同的空气/燃料区域内完成,以实现空气的分级燃烧,延长完全燃烧的时间,降低炉膛温度水平,从而有效的抑制NOX产生,并保证燃料的完全燃烧。1~3号锅炉实际运行中NOX排放质量浓度、锅炉效率、飞灰中未燃烧质量分数、省煤器出口CO、省煤器出口氧量等的测试结果见表1.
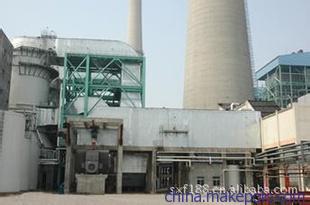
1、NOX的控制效果
据调查,我国燃煤电厂中采用常规燃烧器的固态排渣锅炉中的NOX排放质量浓度一般在600~1200mg/m3之间;而采用低NOX燃烧器的固态排渣锅炉中,NOX的排放质量浓度一般在400~500mg/m3之间。据介绍,单独采用M型低NOX燃烧器,可以将NOX的排放质量浓度控制在410mg/m3以内;采用M型炉内燃烧脱NOX法,其脱NOX效率最高可达50%。若同时采用M型低NOX燃烧器和M炉内燃烧脱NOX相结合的方法,可以将锅炉排烟中的NOX排放质量浓度控制在308mg/m3以下,表1的结果表明:同时采用M型低NOX燃烧器和M型炉内燃烧脱NOX相结合的方法,锅炉烟气中NOX的质量浓度在250~300mg/m3之间,不仅达到锅炉设计的NOX<308mg/m3的性能保证值,而且远低于采用常规燃烧器或仅采用低NOX燃烧器的固态排渣锅炉的排放水平。融合创新开拓市场其NOX排放浓度仅相当于《火电厂大气污染排放标准》(GB13223-1996)规定值的38.46%~46.15%。具有十分显著的NOX控制效果。甘南藏族自治州 SCR超低排放总包公司
联系人:周经理
电话:18600635336
邮箱:huashanghuanbao@yeah.net