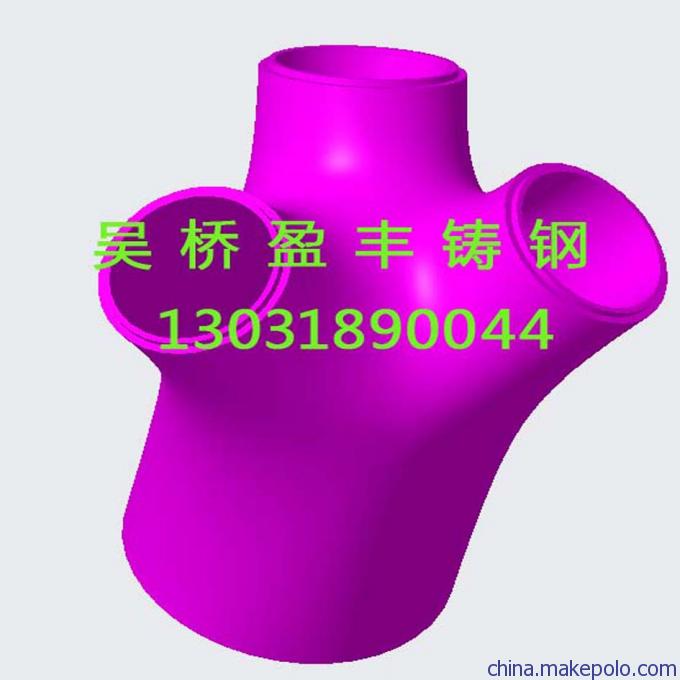
公司将严格按照SO9001-20[量管理体系要求]组织原材料的采购,进行生产过程控制及产品质量控制,并针对铸钢件的质量提出如下保证措施.
1、优化铸件工艺设计,制定生产铸造,机加工,热处理工艺,焊接工艺。关键工序设置监控人,生产时严格按工艺流程操作,保证满足用户使用要求。

2、确定合理的铸件浇注位置,采用阶梯式浇注系统及保温冒口,实现铸件的顺序凝固,确保铸件内部组织致密,无疏松缺陷
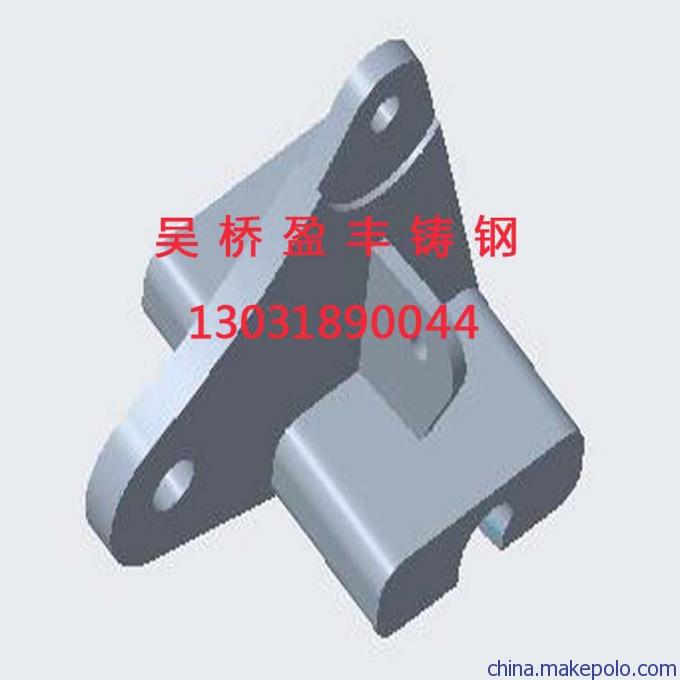
3、采用整体实样,选择合适的木模结构,采用三维建模技术,获取模具关键尺寸,保讧模具尺寸的正确性,从而保障铸件尺寸的精度。着重检查木模衷面质量、角度、尺寸,从首要程序控制加工精度。
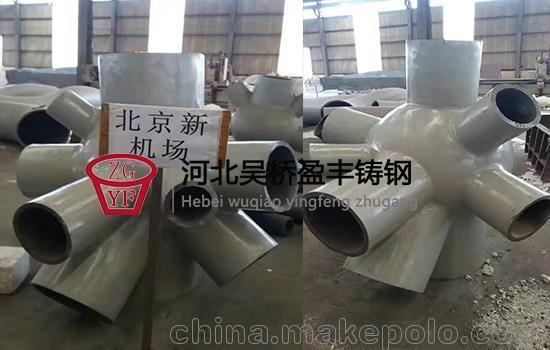
1. 2 铸钢空心球管节点的设计
由于本工程的网壳结构外形特殊 , 跨度大 , 使网壳中的个别节点汇交杆件数量多、杆件截面大、节点构造复杂 , 采用焊接空心球节点根本无法满足设计要求 , 因此在这些节点处采用了铸钢空心球管节点 .本文以工程中规格最大的铸钢空心球管节点为例,说明其设计与分析过程 . 该节点汇交 10 根杆件 , 杆件数量多、直径大 , 其中最大杆的直径为 720 mm , 节点的几何形状如图 1 所示 . 该铸钢空心球管节点的球径为 900 mm , 球壁厚为 70 mm. 综合考虑安全、经济以及铸造工艺等方面的因素, 铸钢管上部 ( 与钢管连接处 ) 的厚度取为与之相连钢管厚度的 1. 5 倍 , 铸钢管下部 ( 与球连接处 ) 的厚度取为钢管厚度的 2. 5倍 . 各铸钢管由球面上的伸出长度结合由满足施焊构造要求所需的最小长度并考虑铸造尺寸的统一 ,取为 650 mm. 节点在铸钢管与球相交处的内外侧以及铸钢管与铸钢管搭接处的倒角半径都取为50 mm.
对于图示的1 ,3 ,5 号杆因钢管管径较小、管与管之间的夹角较大 , 直径 900 mm 的铸钢球可满足焊接空间的要求 , 因此将钢管直接焊在铸钢节点上 .由于节点的球体直径较大 , 在球内设置十字形加劲肋以提高节点强度 . 该铸钢节点的材质参照德国DIN17182 标准中的 GS20Mn5 , 其机械性能指标为 :屈服强度 230 MPa 、极限强度 450 MPa 、延伸率 22 % ,D 级冲击功 37J.
1. 3 铸钢空心球管节点的有限元分析
为了了解节点的应力分布情况 , 确定最大应力区 , 采用大型通用有限元软件 ANSYS 对节点进行有限元分析 . 对于 3 根焊接杆件为了避免或消除边缘效应对节点力学性能的影响 , 分析时将焊接钢管的根部与铸钢节点作为整体参与计算, 焊接钢管材质为 Q345 钢 .
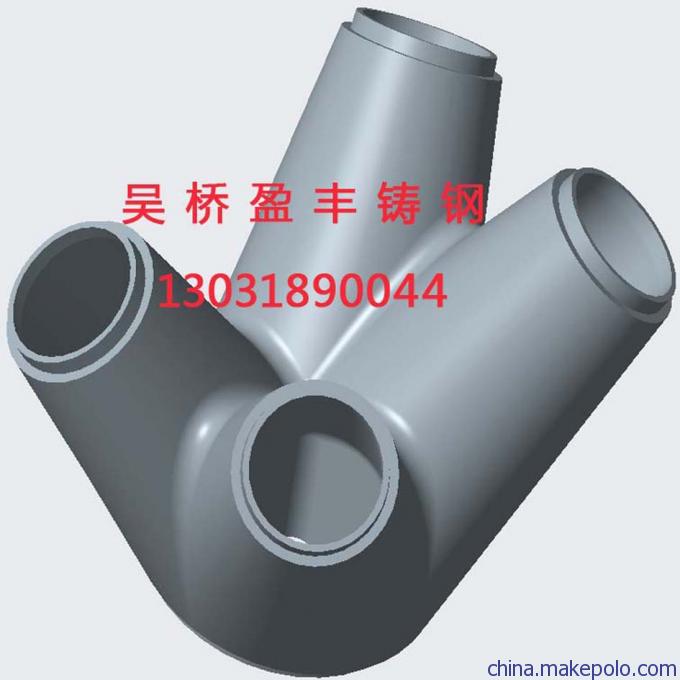
1. 3. 1 模型建立
由于节点与多根空间杆件相连 , 而且在铸钢管与球、铸钢管与铸钢管相交处都存在倒角, 而 ANSYS的前处理器无法对体进行倒角 , 因此为了使计算结果符合节点的真实受力状态 , 我们用 AUTOCAD建立节点的实体模型 , 然后将其存为 SAT 文件 , 直接输入到 ANSYS 中 .
1. 3. 2 单元类型与网格划分
由于铸钢球管节点的球壁及铸钢管壁都比较厚 , 节点建模采用十节点的四面体单元 , 单元类型为SOLID187 , 该单元的每个节点有三个自由度 , 即 X ,Y , Z 方向的线位移 . 单元大小对计算结果的精确度有一定影响 , 单元小 , 虽然求解精确 , 但会增加计算时间 ; 单元大 , 势必降低分析的计算精度 . 综合以上因素 , 网格划分控制单元边长 , 采用自由网格划分 ,划分精度为 6.