在整个耐磨损进口超大尺寸O型圈橡胶加工过程中,混炼胶质量对胶料进一步加工和最终的成品性能具有决定性的影响,混炼是最容易产生质量波动的工序之一。若混炼不好,胶料会出现配合剂分散不均,可塑度上下波动,甚至焦烧、喷霜等现象,导致硫化胶和成品性能下降。
进口超大尺寸O型圈半成品制备:O型橡胶密封圈的生产一般仍以磨压法为主,为了提高生产效率及进口超大尺寸O型圈产品质量,减少浪费,预先制备半成品是有必要的。传统的平板硫化半成品的制造过程是合格的混炼胶经充分反炼后压制成胶片,裁成胶条、胶块。对于量大或规格较大的制品,可以在挤出机上按需要的规格挤压成胶绳,裁成一定的长度,接头按45°搭接,制成O型圈半成品。近年来,国内不少厂家已采用精密预成型机来生产O型圈及其他制品的半成品。这样既提高了生产效率,又保证了半成品体积和重量的准确度,提高了橡胶制品生产工艺的水平。若用注射成型机生产,半成品无需特殊准备,只需将压制好的胶条直接喂料即可。
硫化:目前,进口超大尺寸O型圈模压制品的硫化方法主要有平板模压、传递模压和注射模压三种,平板模压法历史最为悠久,传递模压约在20世纪50年代前后开始使用,而注射模压则是自20世纪60年代起逐步由塑料工业进入橡胶工业的。当前发展趋势是逐步发展注压法,但由于各自适用的范围不同,三者并存并获得发展仍是现实,O型密封圈按其特点仍以平板模压为主要成型方法。
在
进口超大尺寸O型圈模压硫化过程中,必须严格争取掌握硫化的温度、时间和压力,并随时注意硫化过程中
进口超大尺寸O型圈温度等参数的变化情况,进行相应处理,否则会造成产品欠硫或过硫。若采用自动控制系统,这整个硫化过程中会自动记录和控制,以保证产品会达到正硫化程度。
180°分型多腔模模具设计:对于小规格O型圈,如果用户需求量是多次供货,每次每种规格150件以上,应设计多腔模。多腔模模具与单腔模模具设计收缩率一样,都是根据胶料收缩率确定。模具结构一般选择4腔,9腔,16腔,25腔等。
180°分型多腔模进口超大尺寸O型圈模具设计的重点仍然是想对尺寸的确定,其型腔尺寸与180°单腔模模具设计收缩率计算相同。撕边模具余胶槽必须是90°的V形,余胶槽玉型腔的距离在0.05-0.08mm。这里重点阐述一下180°分型多腔模模具的定位方式。
180°分型多腔模模具结构采用导柱,导套定位。导柱导套定位适用于多腔模局及定向定位。16腔以上
进口超大尺寸O型圈采用两种不同规格的定位销,其作用是能够便于操作,核膜的时候不容易发生差错。如果多腔模模具较大,最好采用3腔定位方式。
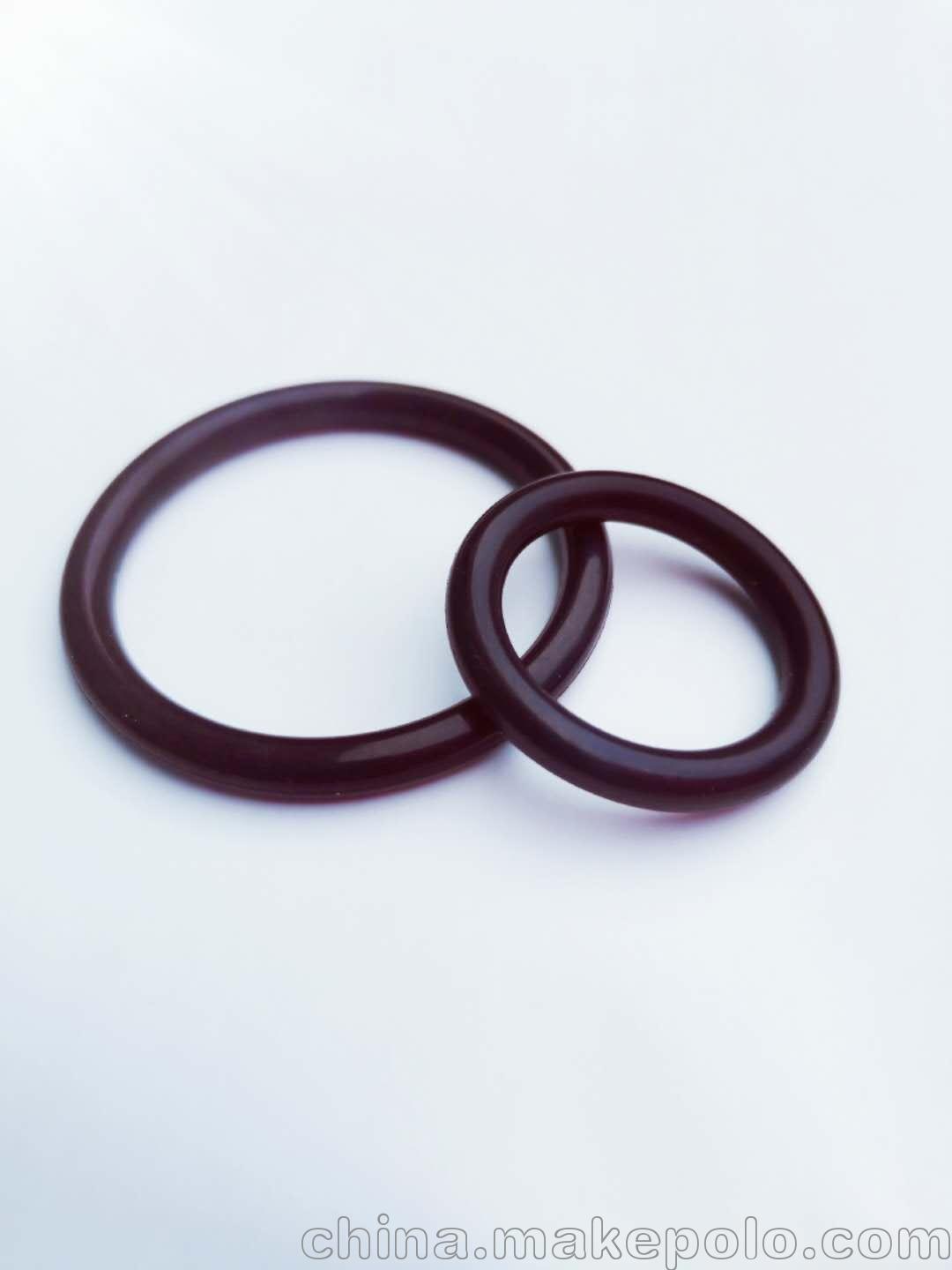
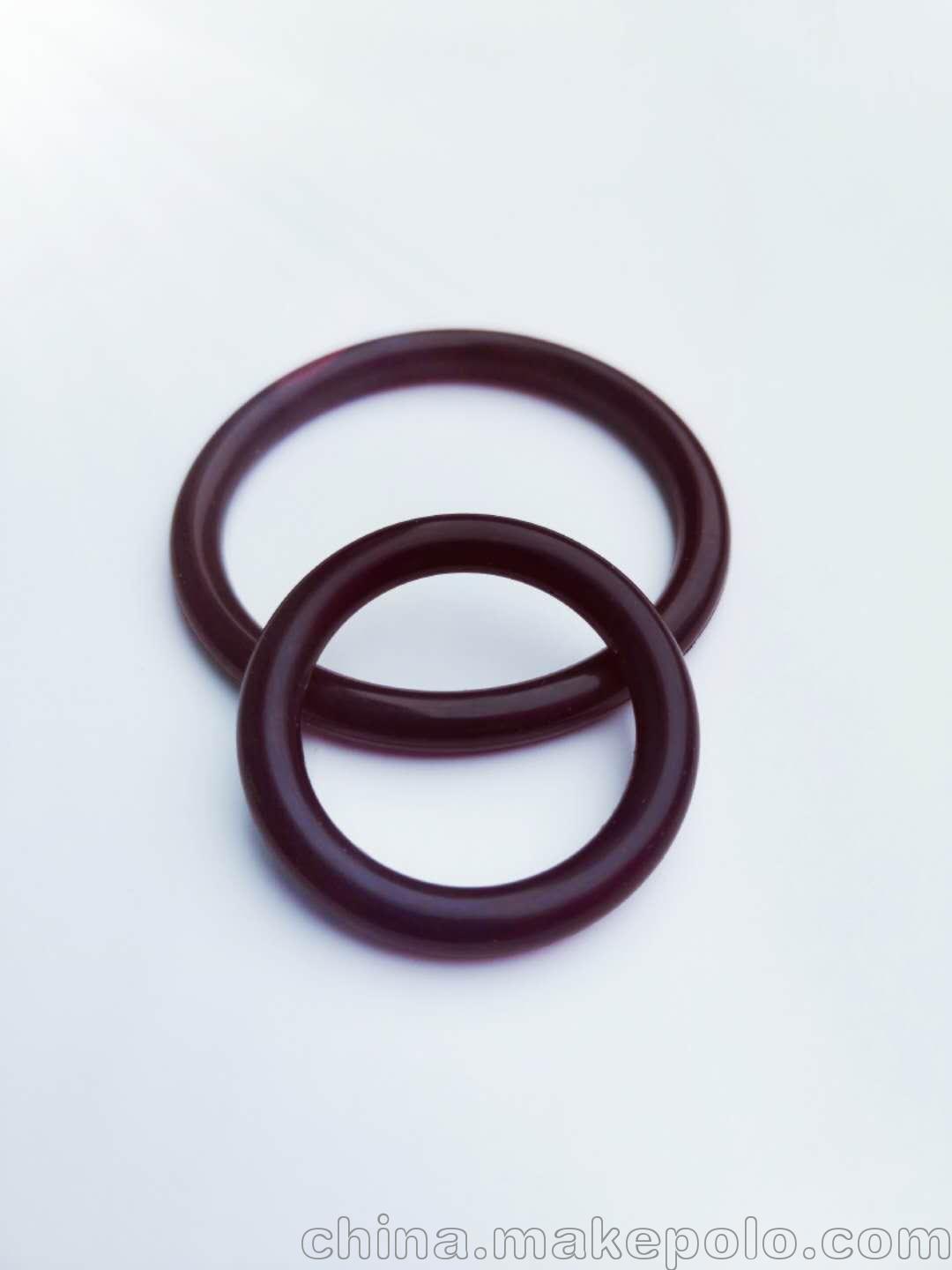
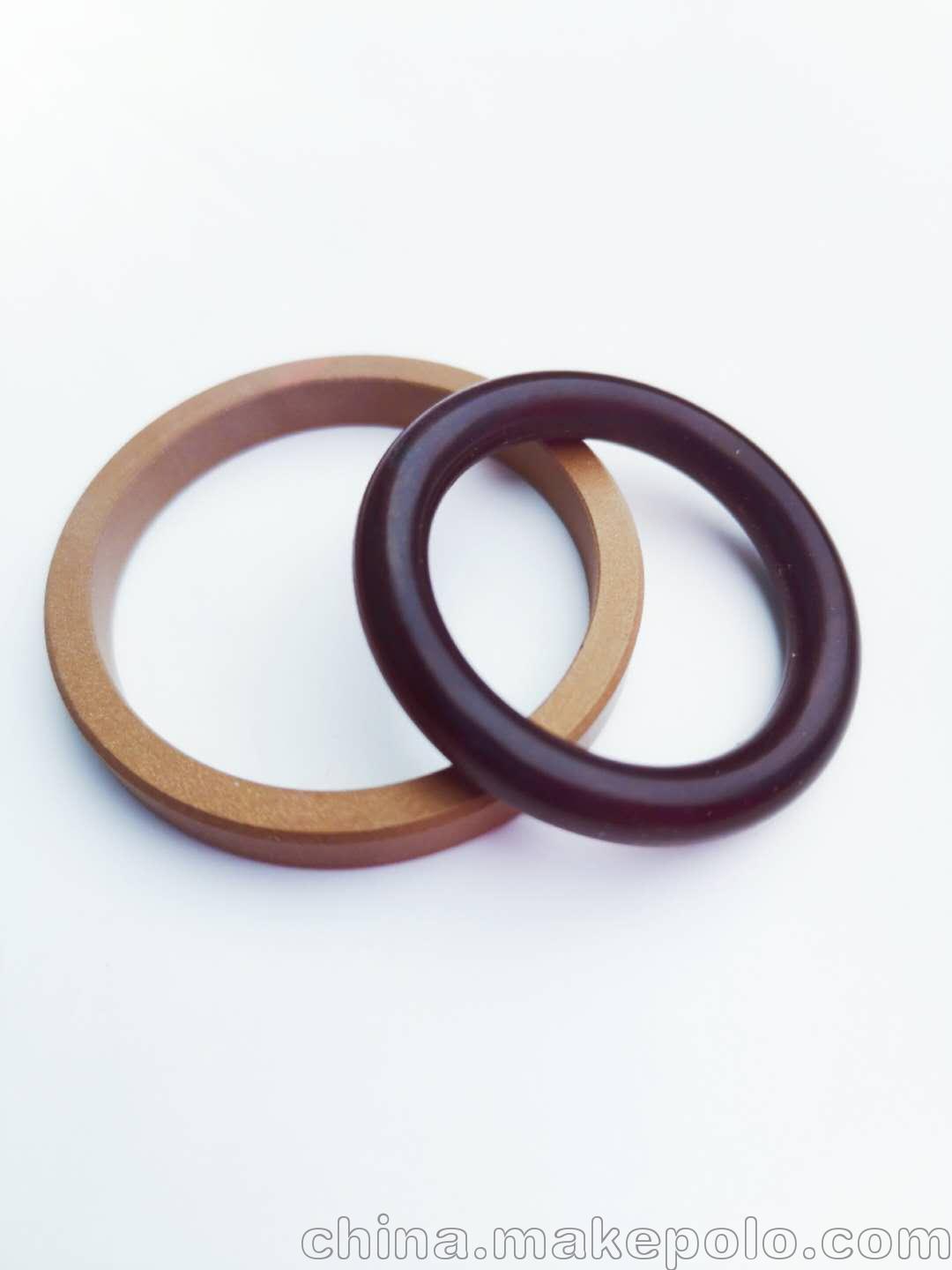
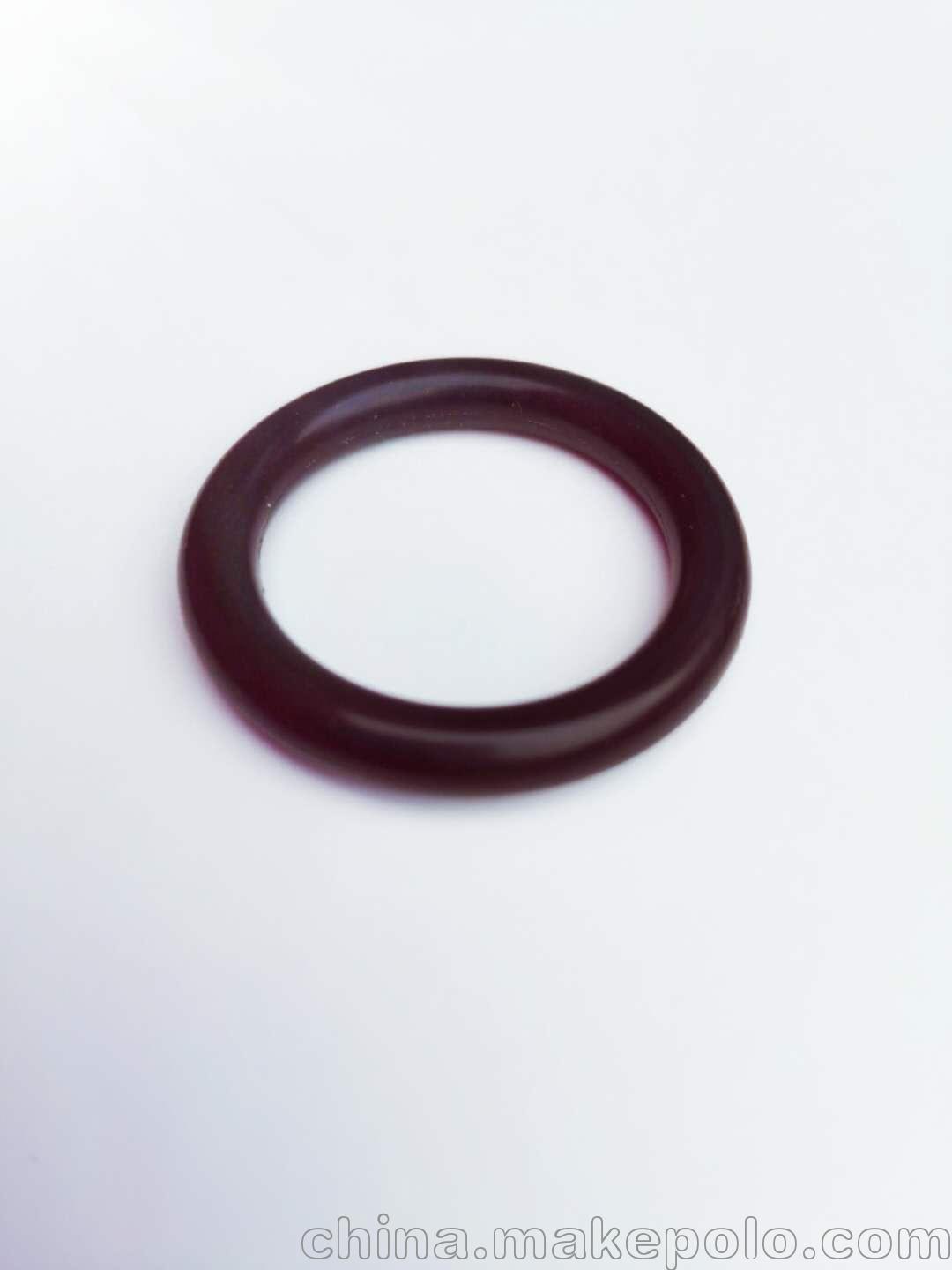
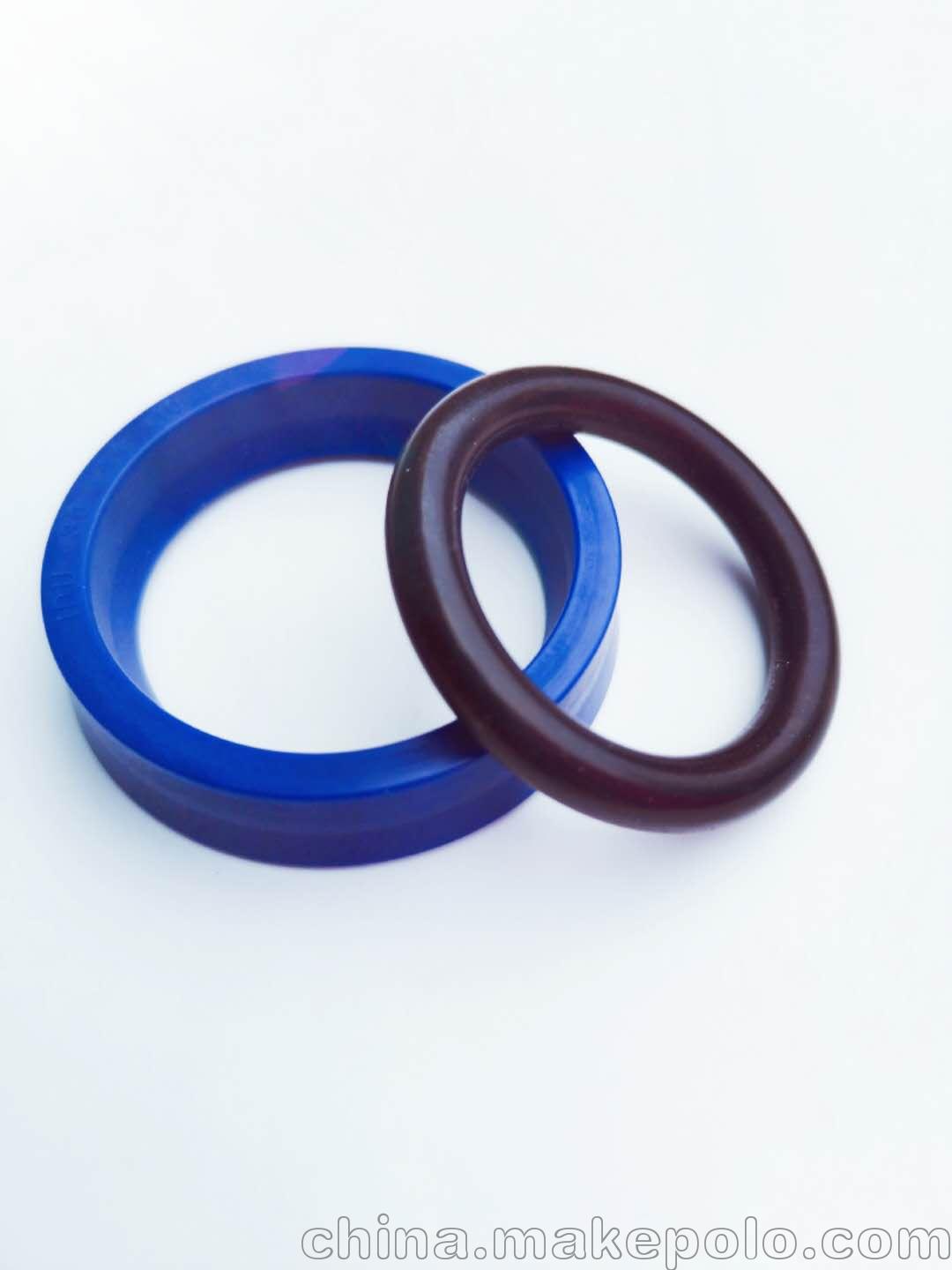